A few years ago, someone mentioned to me that many of his machines were not good candidates for oil analysis because they used little oil that wasn’t worth saving. He added that by the time you flushed the sampling port and pulled a proper oil sample, you’ve almost done an oil change. Why bother with oil analysis?
I’m sure you recognize the misguided purpose of oil analysis in the mind of this individual. While oil analysis can certainly aid in better timed oil changes, it has so much more to offer. In fact, for machines that are mission-critical, the cost of changing the oil is small potatoes in comparison to the value gained from averting a catastrophic machine failure.
If oil analysis was only about tracking the remaining useful life of the lubricant, only a fraction of the oil samples analyzed every year could be economically justified.
Think of the oil more as an information messenger of numerous failure modes and root causes of failure. As I’ve said many times, it’s hard for a machine to be in trouble without the oil knowing about it first. For most labs, the number of non-conforming samples from oil analysis will generally exceed 20 percent.
In other words, more than one out of every five samples has a reportable condition that requires a corrective response. For this reason, you must be prudent about which machines are selected for oil analysis as well as the sampling frequency.
Like most reliability decisions, being wise in selecting machines to include in an oil analysis program requires a strategy of precision and optimization. This selection is a critical attribute of the Optimum Reference State (ORS) and demands careful consideration. Included in this is an assessment of machine and lubricant criticality, as described below.
The Importance of Saving the Machine
So many reliability and maintenance decisions hang on the assessment of Overall Machine Criticality (OMC). This includes oil analysis and all other machine condition monitoring methods. Critical equipment should be checked more frequently than less critical equipment. Based on the definition of “critical,” this refers to the machines with the highest importance to you, your company and your process.
Of course, it is essential to know how to define an asset as critical. There are many approaches to determine an asset’s criticality. Some plants employ a simple 1 to 10 grading scale and subjectively assign numbers.
The OMC assesses criticality in the context of lubrication. It is calculated at the multiplied product of the Machine Criticality Factor (MCF), which relates to the consequences of machine failure, and the Failure Occurrence Factor (FOF), which corresponds to the probability of failure. For a more detailed discussion of these factors and the OMC, see www.machinerylubrication.com/Read/29346/machinery-criticality-analysis.
Using the OMC, a machine’s candidacy for oil analysis is known by influencing factors such as:
- whether the machine is exposed to failure-inducing conditions (loads, speeds, shock, contamination, etc.);
- whether the machine is a bad actor (chronic problems);
- whether the consequences of failure are high (safety, downtime, repair costs, environmental effects, etc.);
- whether failures can be lubricant-induced (degraded or contaminated oil);
- whether failures can be revealed by the oil (e.g., wear debris from shaft misalignment); and
- whether early detection is important.
The Importance of Saving the Oil
The importance of saving the oil is best assessed by the Overall Lubricant Criticality (OLC). The OLC defines the significance of lubricant health and longevity as influenced by the probability of premature lubricant failure and the likely consequences (for both the lubricant and the machine).
The proposed method for calculating the OLC is shown above. Like many such methods, this approach is not an exact science but nevertheless is grounded in solid principles in applied tribology and machine reliability.
The Lubricant Criticality Factor (LCF) defines the specific economic consequences of lubricant failure separate from machine failure consequences. The LCF is influenced by the cost of the lubricant, the cost of downtime to change the lubricant, flushing costs and system disturbance costs (e.g., the fishbowl effect).
For instance, machines that use large volumes of expensive, premium lubricants will understandably have high LCF values. Studies have shown the true cost of an oil change can far exceed 10 times the apparent cost (labor and oil costs).
The Degradation Occurrence Factor (DOF) defines the probability of premature lubricant failure. The conditions that influence this probability are shown below.
Lubricant Robustness - Synthetics and other chemically and thermally robust lubricants lower the DOF.
Operating Temperature - Lubricants exposed to high operating temperatures, including hot spots, can experience accelerated oxidation and degradation. The presence of such conditions will raise the DOF.
Contaminants - Contaminants such as water, dirt, metal particles, glycol, fuel, refrigerants, process gases, etc., can sharply shorten lubricant service life. The presence of such exposures will raise the DOF.
Lubricant Volume and Makeup Rate - Lubricant volume relates to the amount of additives available to fight oil degradation, the estimated runtime to complete additive depletion and the density of contaminants. In normal service, it can take years to burn through the additives in systems containing thousands of gallons of lubricant.
The makeup rate refers to the introduction of new additives and base oil. New additives replenish depleted additives, and new base oil dilutes pre-existing contaminants. High oil volume and a high makeup rate will reduce the DOF.
Machines to Include in Your Oil Analysis Program
Machines that are good candidates for oil analysis have high OMC or OLC values (say, above 5). Even marginal OMC/OLC machines may be well-suited for a streamlined oil analysis program (fewer samples, fewer tests, etc.).
Using this methodology, much of the guesswork is taken out of the first major decision related to any oil analysis program. Once your machines are selected, you can then use the OMC and OLC values to determine the oil sample location, oil sample frequency, test slate, alarms and limits, and data interpretation strategy.
37% | of lubrication professionals say machines at their plant are selected for oil analysis based on the amount of lubricant they hold, according to a recent survey at MachineryLubrication.com |
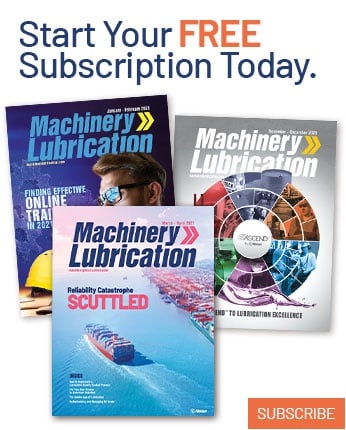