The well-known KISS principle (keep it simple stupid) was first coined in the 1960s and began widespread use in the U.S. Navy shortly thereafter. While it started as a design principle for engineers, it has since been applied to any activity or creative endeavor that has had the propensity to become unnecessarily complicated.
What becomes overly complicated also becomes, by default, poorly understood and sparsely used. Conversely, the greater genius in design and engineering lies in achieving the design objective through simplicity and pureness of form.
This can be applied to the world of oil analysis in many ways. Increasingly, oil analysis has become engulfed by complex analytical chemistry and mathematical algorithms. This science is successful when it takes the complicated, such as an array of particles of varying shapes, sizes, textures, colors and compositions, and puts their formation into plain English (e.g., cutting wear on cylinder walls).
It is less successful when it does the opposite, i.e., overanalyzes and overdetails. If someone asks you for the time, there is no need to give an explanation on how a watch works.
Don’t get me wrong, I’m very proud of the technical progress of the oil analysis field and the tremendous value it has brought to the world of machinery reliability. That said, oil analysis should always be viewed in terms of its many forms. These are not competitive but rather should form a focused and unified activity, each with inherent strengths and weaknesses.
Collectively, they enable oil analysis to function at its best. Like all reliability initiatives, this should deliver reliability at the lowest possible cost. It optimizes reliability, not maximizes it. It’s about making the right choices.
For instance, for a given machine, how frequently should you conduct laboratory analysis? How frequently should you perform wear particle characterization? These are necessary questions needed to achieve the desired optimum reference state (ORS). The four principle forms of oil analysis are identified and described in Figure 1.
Figure 1. The four principle forms of oil analysis
In recent issues of Machinery Lubrication magazine, I’ve introduced Inspection 2.0 as an important reinvention of conventional inspection practices. I see so many low-hanging fruit opportunities for simple, daily, penetrating machine inspections that often go unnoticed and certainly unexploited.
It’s far better to do 100 frequent “screening” inspections than one monthly or quarterly laboratory analysis. Laboratory analysis should still be performed, but it is not a substitute for frequent quality inspections. When this happens, reliability is marginalized and maintenance budgets are wasted.
As a review, Inspection 2.0 can be summarized by the following tenets:
- Culture of reliability by inspection (RBI)
- Advanced, tactical inspector skills
- Machine inspection readiness with inspection windows
- Advanced inspection tools and aids
- Inspection protocol that is aligned to failure modes
- Early fault and root cause emphasis
- Origin of more than 90% of unscheduled work orders
Tactical Inspections Are Purposeful Inspections
With the exception of taste, our four other senses can be effectively used, individually or collectively, for frequent tactical inspections. The concept of tactical inspections is inspection with a purpose. It is not just going through the motions down a checklist. For instance, you don’t just look at oil but rather examine it for specific reasons. The inspectors must know the reasons.
This examination seeks to answer several questions about the health of the oil, the health of the machine and the state of the oil to protect the machine from premature failure. Inspectors should be hunting for something that often is inherently hard to find or notice. The machine, through the oil, will telegraph a signal. The strength of that signal increases as functional failure approaches. Early fault detection is the objective and is best achieved by tactical inspections. I’ll talk about how this can be done visually.
There are no scientific instruments, sensors, algorithms or computers that can outperform the eyes and mind of a human inspector. To get the most out of your sense of sight, you need to know what you’re looking for. Start by constructing a list of root causes and symptoms.
Inspection seeks to find critical states of the oil that cause failure (roots of failure) or reveals active failure in progress (symptoms). As an example, for a diesel engine oil this might be the oil level, soot dispersancy, fuel dilution, coolant contamination and sludge. For an industrial gearbox, you might want to look for a wrong oil level, dirty oil, water contamination, excessive wear debris, aerated oil and an overextended oil drain.
By knowing the questions, you can work backward to define the tactical inspection protocol that provides the answers. This is a two-step process:
- Causes and Symptoms (C&S) - For every machine or system component, list what is important to find (ranked by importance).
- Critical Occurrence States (COS) - For each item on this list, create an inspection protocol that would reveal the state of occurrence (the earlier the better).
A Well-trained Eye
Using the industrial gearbox example, let’s rank the causes and symptoms guided by past experience and help from technical advisors. After each item on the following list are one or more ways to enable earlier alerts by visual inspection.
-
Wrong Oil Level: Level gauge inspections
-
Dirty Oil: Exposed headspace (vents, breather, hatch, etc.), filter in bypass, rapid rise in the filter pressure differential, entrained air problems, sediment in bottom sediment and water (BS&W) bowls, blotter test sediment
-
Water Contamination: Cloudy oil, free water in BS&W bowls, rust on the corrosion gauge, hydrated desiccant breather, entrained air problems, positive result from a crackle test
-
Excessive Wear Debris: Metallic sediment in BS&W bowls, laser pointer inspection, loaded magnetic plug, metallic debris on the filter’s surface, magnet inspection of oil sample
-
Aerated Oil (Entrained and/or Foam): Sight glass inspection (cloudy or frothy oil), sudden rise in the oil level, hatch inspection, rise in the oil temperature, emulsified water
-
Overextended Oil Drain: Sight glass inspection (dark, sludgy oil), dirty oil, excessive wear debris, soft insolubles on blotter, air-handling problems
After each inspection (that passes), the inspector should have a high level of confidence that there are no active or abnormal C&S conditions related to the oil or machine. This is done by skillful inspection in search of the COS. If you engineered your inspection protocol properly, it would be extremely difficult for there to be an active C&S in progress without a positive alert from an inspection of each of the COS. These critical occurrence states are designed to effectively reveal C&S events.
Routine Inspections
A routine inspection consists of quick and frequent inspection events not generally requiring the use of tools, pulling a sample or special inspection aids. The following are examples of routine visual inspections related to lubricating oil:
Oil Level - Visually inspect the dipstick, level gauge or sight glass.
Oil Color and Clarity - This involves a sight glass inspection aided by a strong light. Usually a comparator image is used.
Foam Presence and Stability - This can be determined by some sight glasses or headspace inspections, or both.
Entrained Air Presence and Stability - Also generally assessed by sight glasses and headspace inspections.
Free Water - Inspect water traps or BS&W bowls for a free water phase.
Emulsified Water - Inspect sight glasses for turbidity.
Oil Sediment and Floc - Inspect sight glasses and BS&W bowls for stratified solids and soft insolubles.
Gauge and Sensor Inspections - These inspections utilize various digital and analog gauges, including temperature, pressure and flow. Some machines have sensors that report oil properties, such as particle count, wear particle density, water contamination and viscosity.
Heat Gun Inspection - This provides a quick, quantitative assessment of the oil temperature on critical machine surfaces.
Magnetic Plug Inspections - Some sight glasses have integrated magnetic plugs for quick and effective observation.
Headspace Inspection - Hinged hatch access aided by a strong light can enable observation of bathtub rings, varnish and foam.
Corrosion Gauge Inspection - Similar to magnetic plugs, these gauges can be quickly inspected to reveal corrosive conditions associated with corrosion agents, impaired rust inhibitors, etc.
Leakage Inspection - Failed seals and radial shaft movement can cause leakage, but this can also be due to a sudden drop in oil viscosity, change in oil chemistry or ingression of certain liquid contaminants.
Exception Inspections
Exception inspections are conducted either because of a reportable or questionable routine oil inspection or as the result of an abnormal operating condition. Most exception inspections require the extraction of an oil sample and a simple test that can be performed at the machine or on a benchtop. The following are examples of visual exception inspections related to lubricating oil:
Blotter Spot Test - This simple test can be extremely helpful for detecting a range of contaminants and abnormal oil conditions.
Blender Test - This test can be performed with a blender or graduated cylinder. It is useful for revealing certain contaminants, degraded oil chemistry, impaired air-handling ability and other abnormal conditions.
Inverted Test Tube - This is an old method that uses the rate of rising air bubbles to roughly estimate oil viscosity. Graduated cylinders or sample bottles can be utilized as well.
Oil Drop on the Surface of Water - Certain additives and chemical contaminants influence the interfacial tension of lubricants. Placing a couple drops of oil on the surface of water can quickly exhibit this. Compare the results to that of new oil.
Cold Oil Turbidity - Oil with trace amounts of water can be assessed by placing a sample of the oil in a refrigerator for an hour. Dissolved water will saturate in oil at cold temperatures and become visibly noticeable by a cloudy appearance.
Hot Oil Clarity - The presence of soft oil insolubles (oxides, organic materials, dead additives, insoluble additives, varnish potential, etc.) and some emulsified water will often quickly dissolve in the oil when heated. This is visibly noticed by the oil becoming markedly clearer (less turbid).
Crackle Test - This well-known test for water contamination can be performed with a hot plate or soldering iron.
Bottle and Magnet Test - The presence of ferromagnetic wear debris particles can be separated and concentrated for quick inspection by placing a strong rare-earth magnet against the outside surface of an oil sample bottle and then agitating. For high-viscosity oils, dilute the oil first with kerosene or another solvent to lower the viscosity.
Laser Pointer Test - Shining, reflective particles can be easily observed in many oils by passing a laser through the oil. The particles will scatter the light. It sometimes is best to allow the particles to settle to the bottom of the bottle first and then pass the laser light up from below.
For more information on these test methods, refer to the Daily One-Minute Lubrication Inspections and Field Tests booklet in the Noria bookstore at store.noria.com.
70% | of lubrication professionals perform daily visual inspections of the oil at their plant, based on a recent survey at MachineryLubrication.com |
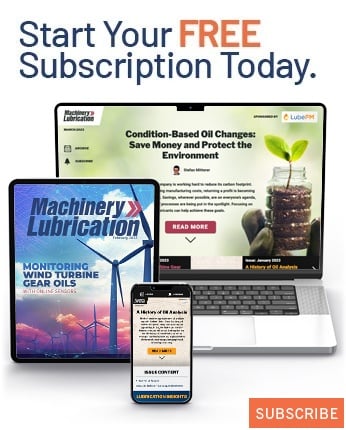