As this issue of ML has been diving into all things tribology, let’s take a minute to focus on some important aspects of the proper storage of lubricants. Lubricants play a crucial role in various industries, from automotive to manufacturing and beyond. They ensure the smooth operation of machinery and equipment, reduce friction, dissipate heat and prevent wear and tear.
However, to maintain their effectiveness and extend their shelf life, it is essential to store lubricants properly. In this article, we will explore the importance of proper lubricant storage and provide guidelines for ensuring longevity and efficiency.
Why Proper Lubricant Storage Matters
Prolonged Shelf Life
Lubricants, whether in the form of oils, greases, or other compounds, have a finite shelf life. Proper storage can help extend this shelf life, saving money and resources. Correctly stored lubricants maintain their original properties, ensuring consistent performance in critical applications.
This consistency is vital for machinery reliability and longevity. Proper storage minimizes the risk of contamination by moisture, dirt, or other contaminants, which can compromise the lubricant's performance and, consequently, the equipment it is meant to protect.
The first thing to focus on is the climate. Lubricants should be stored in a cool, dry place with a controlled temperature. Extreme temperatures can degrade the lubricant's quality. Ideal storage temperatures typically range between 50°F and 80°F (10°C to 27°C).
Lubricants should never be stored in direct sunlight or near heat sources, as this can accelerate oxidation and reduce the effectiveness of your lubricants. Just putting lubricants in a climate-controlled room is not proper storage we want to ensure that lubricant containers, whether drums, pails, or bottles, are tightly sealed. This prevents moisture, dust, and airborne contaminants from infiltrating the lubricant.
Ideally, we want to see some sort of filtration of new oils and then transfer them to a clean tank. If this is not possible, then we should always replace container caps or seals immediately after use to maintain product integrity.
Another thing we want to be aware of when it comes to lubricant storage is that we are not cross-contaminating lubricants — we want to see clearly labeled containers listing not only color but also shape, which provides multiple ways to verify the lubricant that is in the container.
Even small amounts of one lubricant mixing with another can alter their properties. Also, make sure to note the date the lubricant was received. This will help with the “first-in, first-out”, regarding usage.
The Proper Handling of Lubricants
Now let’s dive into the proper handling of lubricants. When handling lubricant containers, make sure to use clean tools and equipment to avoid introducing contaminants. A “top-up” container that can be filled without the removal of the lid is ideal.
As we discussed above, when it comes to usage of your lubricants the “first-in, first-out” rule of thumb prevents your lubricants from reaching the end of their shelf life before you use them. We need to make sure that we have a good way to track the use of our lubricants, whether it be good old-fashioned pen and paper or on a computer-based tracker. Knowing the usage rate of your lubricants prevents you from possibly running out at a crucial time and also keeps you from over ordering.
Upon receiving new lubricants, examine them right away to ensure there was no damage or contaminants that were introduced during transit. A couple of tools to help keep contaminants like water and debris particles include desiccant breathers or filtration carts with quick-connect fittings through which you can add the lubricants without exposing them to any contaminants in the environment.
Lubricants act as silent guardians, ensuring the gears keep turning, the engines keep running, and the processes remain smooth. However, the significance of proper lubricant storage and handling is often underestimated, despite its pivotal role in the efficient and sustainable functioning of these industries.
Ensuring Consistency in Performance
This article has sought to shed light on the importance of this crucial practice and provide a comprehensive set of guidelines to help facilities master the art of lubricant management. Lubricants are not just substances in bottles or drums — they are the lifeblood of mechanical systems. Neglecting their storage can have profound repercussions, including a reduction to the consistency in performance.
A lubricant's role is to deliver consistent and efficient performance. If a lubricant's properties are compromised due to improper storage, machinery reliability is jeopardized. Consistency ensures that operations run smoothly, maintenance costs stay in check, and productivity remains unhindered.
Reduced Contamination
Lubricants are sensitive to contaminants like moisture, dirt, and impurities. The equipment they protect is reliant on their purity. Proper storage is the first line of defense against contamination, safeguarding both the lubricant's effectiveness and the machinery's longevity.
As we've explored through this article, temperature control, protection from heat and light, airtight containers, and avoiding cross-contamination are all vital facets of proper lubricant storage. Equally important are the principles of proper handling and usage tracking, which help organizations avoid waste, manage inventory, and reduce risks of running out or overstocking.
Environmental responsibility should be at the forefront of any organization's approach to lubricant storage. Developing a plan for the responsible disposal and a documented emergency-response strategy is a commitment to both the environment and the safety of employees.
In essence, proper lubricant storage and handling are the cornerstone of effective lubricant management. Neglecting these practices can lead to decreased lubricant effectiveness, equipment breakdowns, and even environmental hazards. By embracing and implementing these guidelines, industries can not only ensure the longevity and efficiency of their lubricants but also contribute to the overall success and sustainability of their operations.
After all, it's the meticulous care of these silent guardians that keeps the wheels of industry turning smoothly.
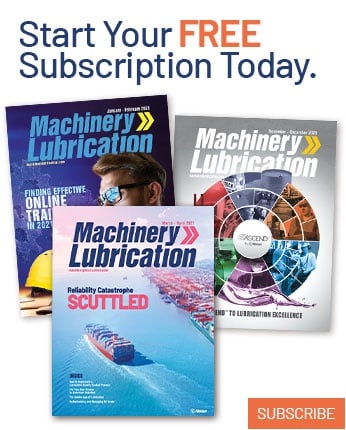