Much has been said and written about biodegradable lubricants for the past several years. Manufacturers and blenders of these products promote biodegradables for use based on the importance of biodegradability and nontoxicity.
But performance issues - like oxidation stability, antiwear protection, hydrolytic stability, viscosity- temperature properties and cost factors - are usually presented only wherever these features provide an advantage to the particular manufacturer. The two primary classes of biodegradable lubricants, vegetable oils and synthetics, have been described and well documented, when compared with traditional mineral oil-base lubricants.
However, little information has been provided by major oil companies or the manufacturers of these biodegradable products with regard to application guidelines or the maintenance of these products once they are in use as machine lubricants.
Industrial users of these products must be prepared to treat biodegradable lubricants somewhat differently than standard mineral-base oils. In order to understand these application and maintenance requirements, it is necessary to review the various types of biodegradable lubricants to point out their advantages and disadvantages.
Vegetable Oils
Vegetable oils include corn, soybean, rapeseed (canola), sunflower, peanut, olive oil and others. In their natural form, these oils consist primarily of triglyceride molecular structures and as such they have performance limitations, most notably, poor thermal, hydrolytic and oxidation stability. For example, most natural vegetable oils cannot withstand reservoir temperatures greater than 80ºC (176ºF).
In addition, water, even in small amounts of a few hundred parts per million, is the natural enemy of vegetable oils and can cause serious foaming and degradation problems. In general, these oils also exhibit low cold-flow abilities. On the other hand, most of these natural oils have good lubricating qualities due to their polar nature.
This provides good metalwetting attraction and also makes them good solvents for helping keep dirt and debris off metal surfaces. Their molecular structure provides for a high natural viscosity and viscosity index. Genetic modifications have also overcome much of the thermal and oxidative stability problems, particularly with soybean and canola oils.
![]() |
Figure 2. Hydraulic oils for use in mobile equipment can be made from a blend of synthetic diester and canola (rapeseed) oil to deliver excellent temperature viscosity properties and good oxidation stability - even in the colder operating conditions found in Northern climates.
|
Synthetic Oils
The primary synthetic biodegradable lubricants available today include:
Polyalphaolefins (PAOs)
These exhibit excellent low-temperature properties, but tend to shrink rubber seal materials.
Diesters
These have good antioxidation characteristics and seal swell properties.
Polyalkylene Glycols (Also Known as Polyglycols or PAGs)
PAGs can be both water soluble (ethyleneoxide) and water insoluble (propylene oxide). Water soluble PAGs are ideally suited for fire-resistant lubricants. One disadvantage of PAGs is their tendency to emulsify water in certain equipment, such as gear boxes, which will cause foaming, sludge and corrosion.
A major disadvantage of both PAOs and PAGs is their poor solubility with regard to additives. Because the additives themselves must also be biodegradable, this limits the additives that can be used to formulate effective biodegradable lubricants from PAOs and PAGs.
Today, some manufacturers are blending diesters with PAOs to form base oils which are biodegradable, have good solubility, resist oxidation and have good temperature viscosity characteristics. Others are blending synthetic diesters with canola oil to provide similar results.
![]() |
Figure 3. In sawmills, the use of biodegradable chain bar, blade and saw-guide lubricants is critical because the oil enters the environment immediately after use. The saw-guide lubricant used here is made from natural canola oil which is more than 99 percent biodegradable in 21 days.
|
Before You Switch . . .
Obviously, biodegradable lubricants are desirable for equipment used in certain resource industries, such as forestry, mining, petroleum exploration and production or wherever the lubricants themselves might come into contact with the environment.
The practical considerations associated with conversion from mineral-base lubricants to biodegradable fluids are often ignored. These biodegradable lubricants may be different in their characteristics, and the conversion necessary for their effective use is not quite as simple as draining the used mineral oil and dumping in the new biodegradable lubricant.
Before converting to a biodegradable lubricant, it is first necessary to consider the lubricating system’s operating and design characteristics, such as the operating temperature, pressures and flow rates, the type of sealing or hose materials used, the potential for contamination, such as water or dust and dirt and whether or not the quality of the existing filtration system is sufficient for the new fluid.
A most important consideration that is also frequently ignored, is whether or not the new biodegradable fluid is compatible with mineral oil. If it is not, serious problems may result if all of the old mineral oil is not thoroughly flushed from the system before the new fluid is installed.
Symptoms of a poor or incomplete conversion to biodegradable fluids include severe foaming, leaking seals, plugged filters, higher-than-normal wear on some components (such as the hydraulic pump), and increased operating temperatures.
What Goes Where
So where are the best places to use each type of biodegradable fluid discussed above? For successful conversions in specific applications, users should consider the following:
-
Vegetable Oils: These products are ideally suited to applications such as sawmill blade or chain drive lubrication where the lubricant is used on a “once through” basis and where low toxicity is required. They are also well-suited for use in low to medium pressure hydraulic systems, or lightly loaded gear drives where the operating temperature does not normally exceed 60ºC (140ºF) and where there is little chance of water ingress or high contamination.
Where the threat of contamination exists, filters must be inspected more frequently, due to the lower filterability of these fluids. Gear boxes and hydraulic systems should be thoroughly flushed to remove debris, sludge and silt prior to the application of vegetable-base lubricants to avoid any unnecessary incompatibility potential. There may also be some negative reaction to sealing materials such as neoprene and nitrile. -
Polyalphaolefins: Biodegradable PAOs are finding increased use as hydraulic and engine oils, particularly in cold-climate applications and where hydraulic pressures are high. These oils are also finding selected use as gear lubricants due to their ability to provide lower operating temperatures and their lower coefficient of friction, both of which help reduce wear.
These products are generally compatible with mineral oils and as a result, there is no requirement for extensive flushing prior to conversion unless required by the manufacturer. PAOs have a negative effect on certain sealing materials causing shrinkage, so initial leakage may be a problem. -
Diesters: These biodegradable fluids are excellent lubricants for compressors and turbines. Diester fluids may have a negative effect on certain varnish or paint surfaces, due to their exceptional solvency and detergency, so it would be wise to remove the paint from any internal contact surfaces such as the reservoir, prior to conversion.
In addition, these fluids can negatively affect sealing materials, and fluorocarbon seals should be considered for these applications.
- Polyglycols: PAGs can be either polyethylene or polypropylene oxide-based, with water solubility differing according to type. Polyethylene-based PAGs are highly water soluble, are poorly miscible with mineral oils and are very polar. As a result, thorough flushing of the system should be carried out prior to the conversion from mineral oil-based products. Their water solubility helps to provide biodegradability, but also provides a disadvantage in lubricant applications, because free water contamination tends to occur quickly.
Click Here To See Table 1 -
Suggested Condition Limits for Biodegradable Fluids
Additionally, the high specific gravity of these fluids tends to elevate solid particle contaminant retention (that is particles are less prone to settle). To offset this threat, the filtration systems should be modified or upgraded to ensure that bearing surfaces are not exposed to high contaminant levels. Three-micron filters installed in a side-stream are beneficial in controlling contamination in hydraulic applications.
Operating temperatures must be controlled in order to avoid excessive and unnecessary evaporation of these water miscible fluids. The recommended operating temperature should be kept within a range of about 50ºC to 60ºC (122ºF to 140ºF).
Another consideration when using biodegradable water-based and water soluble fluids in a hydraulic application is cavitation damage to pressure relief valves which may be required to remain in the discharge or open position for long periods. Vapor phase cavitation can cause erosion of the valve seat due to high vapor pressure, which can lead to premature relief valve failure. Proper valve selection prior to conversion should be considered.
![]() |
Figure 4. Power generation is closely linked to river systems. The potential for adverse environmental effects from mineral oil leaks or spills is a serious concern. Operational tests confirm that diester biodegradable oil is equal or superior to mineral base oil in its service capability in turbine applications. The research also confirmed that vegetable oil (canola) is not appropriate where lead babbitt sleeve bearings are used in turbine equipment. The canola oil showed an increase in acidity due to its poor hydrolytic stability which resulted in increased corrosive wear of the lead babbitt material.
|
Keeping it Going
It has been said that the lubricant contained within a piece of machinery is also a component of that machine. It therefore must be maintained and monitored for its condition just like the machine itself. Unfortunately, the lubricant’s condition is frequently ignored until a problem arises and only then does anyone seem concerned about the maintenance of the lubricant.
One cause for this situation is the tendency by many in industry to arbitrarily extend oil drains without giving any thought to the consequences. In most cases, biodegradable lubricants, such as synthetic PAOs or vegetable oils, can cost three, four or five times the price of mineral oil. The users frequently attempt to recoup their initial investment by ignoring common sense and extending oil drains without a regularly scheduled, carefully selected oil analysis program.
Generally speaking, biodegradable oils should be maintained and monitored during use just like mineral-base oils. They must be kept cool, clean and dry (water-free) and their condition should be monitored on a regularly scheduled basis using readily available oil analysis techniques.
Specifically, biodegradable lubricants must be monitored for viscosity (at both 40ºC and 100ºC); free water content (using an accurate technique such as the Karl Fischer test); acid number (which can provide an accurate indication of any increase in oxidation) and solid particle contamination (using particle-count testing techniques).
Any result which indicates that a problem is developing must be investigated and the condition corrected, if satisfactory service life from biodegradable lubricants is to be achieved.
Coefficient of Friction
A lubricant’s coefficient of friction (COF) represents the lubricant’s ability to minimize the amount of frictional resistance between moving components. The COF is a measure in pounds of force necessary to move an object with fixed dimensions (surface area and weight) over a test surface, and is provided in foot pounds of force.
This two-disk test result was reported by Rolf Luther in Lubricants and Lubrication. The figure (right) demonstrates the load bearing comparison between a mineral oil and a polyol ester (trimethylolpropane ester or TMP-Ester).
This test condition indicates that this POE has a friction coefficient of approximately half of the equivalent viscosity mineral oil. There are differences between mineral oils and PAOs and other synthetics as well.
References
- Klamann, D. Lubricants and Related Products. Germany: Verlag Chemie. p. 107-113, 121, 325-326.
- Leugner, L. The Practical Handbook of Machinery Lubrication, 2nd Edition. Canada: Maintenance Technology International, Inc. p. 75-76, 144, 149.
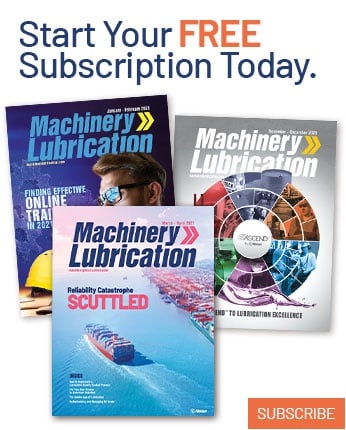