The terms polyalkylene glycol and polyglycol are used interchangeably. These fluids can be manufactured to be either water soluble or water insoluble (oil soluble). The most common are the water-soluble fluids, and thus they can have some very different properties.

Polyglycols are moderately polar, which gives them moderate film strength properties. They have a very high viscosity index (180 to 280) and good low and high temperature abilities.
They burn off cleanly, leaving no residue, and have been used as a carrier oil for solid lubricants for high-temperature chain lubrication. Some versions are food grade and biodegradable. They are used as compressor oils in rotary screw and reciprocating units, worm gear oils, fire-resistant lubricants, metal-working fluids and as brake fluids.
Water-soluble polyglycols are not compatible with mineral oils and therefore must be handled and disposed of separately. They should not be mixed with mineral oils. The result is a gelatinous, gooey mess. Although they are excellent lubricants, they can pose a logistic problem in plants. They can also have some negative effects on paints and seals, and are very expensive.
Water-insoluble (oil-soluble) polyglycols are likely to become more common and are used as heat transfer fluids, high-temperature bearing oils and in screw-type refrigeration compressors.
For centuries, lubricants have been utilized as a way to reduce friction and wear on moving parts. In 2005, 40 million tons of lubricants were produced.
While natural mineral oil-based fluids represent the majority of the market demand, many technological advances in equipment and machinery would not be possible without the benefits offered by improvements in synthetic lubricants, which currently make up only two percent of the market.
While polyalphaolefins (PAOs) fill some of these needs, a growing number of applications are demanding higher performance requirements, or require unique specifications that are not met by traditional lubricants.
One of the most versatile types of synthetics is polyalkylene glycol (PAG) lubricants. PAGs are generally known as compressor lubricants, and their use in industry has increased since the 1980s. Increasing performance standards in the automotive and industrial markets peg these sectors as areas that show promise for growth.
This article offers an overview of the main synthetic base stock chemistries and an in-depth analysis of the benefits and uses of PAGs.
Synthetic Lubricant Base Stocks
There are six major base stock types used in the development of synthetic lubricants, with each offering its own set of unique properties and applications.
Silicones are valued for their low volatility, inertness to most chemical contaminants and thermal stability in severe applications, as well as their performance in low-temperature environments.
These qualities make them an excellent candidate for use as heat transfer fluids, specialty grease applications and DOT Type 5 automotive brake fluids. However, there are two limitations of silicones that must be considered for lubricating applications.
First, they cannot be used in the cylinder lubrication of internal combustion engines because the combustion by-product is silicon dioxide.
Second, extreme pressure performance is limited, and common extreme pressure additives are incompatible with them. In their proper applications, the fluid life and hydrolytic stability of silicones is unsurpassed.
Diesters, or dibasic acid esters, were developed during World War II and are the reaction product of long-chain alcohols and carboxylic acids. Historically, they have been effective as reciprocating compressor lubricants due to their low coking tendency at temperatures of 400°F or higher. They also provide excellent solvency and detergency. The aggressiveness of diesters toward elastomers, seals and hoses has limited the usefulness of these fluids. Newer fluids, such as polyol esters, meet the needs of many applications formerly filled by diesters.
Polyol esters, or Neopentyl poly esters, have largely replaced diesters in high-temperature applications where oxidative stability is critical. Common applications include their use as lubricants in aircraft engines, high-temperature gas turbines, hydraulic fluids, and as heat exchange fluids. They can also be used as a co-blended basestock with PAOs to enhance additive solubility and reduce the tendency of PAOs to shrink and harden elastomers.
PAOs are hydrocarbon polymers manufactured by the catalytic oligomerization of linear alpha olefins like alpha-decene. They are considered high-performance lubricants and provide a high viscosity index and hydrolytic stability. PAOs are the most commonly used, and are generally less expensive than other synthetic lubricants. They have been used in passenger car motor oils, as well as numerous industrial lubricant applications.
Phosphate Esters are valued in applications where safety and fire resistance are critical considerations, which include fire-resistant hydraulic fluids and aircraft fluids. High flash points and fire points enhance their resistance to ignition, and their low heat of combustion makes them excellent self-extinguishing fluids. However, they do have several weaknesses including poor hydrolytic stability, which can lead to the formation of aggressive acidic by-products. Care must be taken when used because they can also react and degrade a variety of commonly used sealants and paints.
PAG oils offer quality lubricity, high natural viscosity index and good temperature stability. PAG base fluids are available in both water soluble and insoluble forms, and in a wide range of viscosity grades. They offer low volatility in high-temperature applications and can be used in high- and low-temperature environments. They are commonly used as quenchants, metalworking fluids, food-grade lubricants and as lubricants in hydraulic and compressor equipment. However, the water soluble PAG oils are incompatible with petroleum oil, and care must be taken in transitioning equipment from hydrocarbon oils to PAG oils.
The Development of Polyalkylene Glycol
PAG oils were one of the first synthetic lubricants to be developed and commercialized. They were created under mandate from the U.S. Navy in response to hydraulic fluid fires on ships resulting from ordnance strikes during World War II. In 1942, and for the next 30 years, the Navy began to exclusively use PAG-based water glycol hydraulic fluids that were fire-resistant and could operate over a wide temperature range. Later, PAG oils began to see extensive use as textile lubricants and as quenchants in metal heat treating.
PAG oils are classified by their weight percent composition of oxypropylene versus oxyethylene units in the polymer chain. PAG oil with 100 weight percent oxypropylene groups are water insoluble; whereas those with 50 to 75 weight percent oxyethylene are water soluble at ambient temperatures.
Although PAG oils have long been used as industrial lubricants, recent work has led to the development of PAG lubricants for use in equipment in the food processing industry. These products are known as food-grade approved lubricants.
In these applications, they offer excellent lubricity, increased oxidative stability, a high viscosity index (180 to 280) and low pour points. They are one of the few synthetic substances identified in the FDA’s food additive regulation for food-grade lubricant base stocks, 21 CFR § 178.3570, for use in industrial machinery when incidental food contact with a lubricant may occur.
PAG Oil Applications and Benefits
Because of the properties that make up PAG lubricants, they are uniquely suited for a number of industrial and manufacturing applications. Their water solubility allows for easy clean-up of equipment. PAG lubricants offer high viscosity indexes, and are shear stable.
PAG oils are also valued for their low volatility in high-temperature applications, and for resistance to formation of residue and deposits. Their biodegradability makes them ideal for environmentally sensitive applications.
PAG oils are best known as compressor lubricants. PAGs are also the lubricant of choice in high-pressure natural gas and ethylene compression, where the viscosity stability of hydrocarbon-based lubricants is adversely affected due to solubility of the gas in the fluid.
In refrigeration compression, PAG and polyol ester-type lubricants are used almost exclusively with the current generation of environmentally friendly HFC refrigerants such as R-134a and R-152a.
The two largest U.S. air compressor OEMs have used PAG lubricants as the standard factory fill in rotary screw air compressors for almost 20 years. More recently, a third compressor OEM has begun to offer PAG oil as an optional fluid.
From the laboratory perspective, the condition of PAG fluids is relatively easy to monitor. In most applications, as the end of the useful life approaches, the only significant change is the increase in acid number (AN) from fluid oxidation.
Depending on the additive package, fresh PAG oils will typically have an AN of 0.1 to 0.5 mg KOH/g. An increase of 1.0 from the new fluid specification is a good condemning limit.
Viscosity remains fairly stable, even during the latter stages of fluid life. Water limits may be set higher for PAG oils than hydrocarbon fluids because they are more water tolerant than other fluid types. Even a “water insoluble” PAG oil will tolerate as much as 0.7 percent water contamination before allowing free water to exist in the fluid.
PAG oils are also useful in industrial equipment operating year-round without seasonal changes. Their superior heat transfer characteristics and thermal and oxidation stability make them ideal for use as heat transfer fluids in large, open vented systems and for process fluids in the production of plastics, elastomers, threads or fabricated parts where compatibility of the fluid with the processed part is important.
Textile fiber production is another industry that benefits from the use of PAG oils. These lubricants do not stain or discolor fibers, and are easily removed during the scouring process. PAG oils are also the lubricant of choice for many high-speed, high-temperature fiber processes where shear stability is a requirement. In addition, they are often used as lubricants in textile manufacturing equipment as extreme-pressure gear lubricants.
A renewed emphasis on energy conservation has increased interest in energy-efficient gear lubricants. For example, the extreme demands of gear lubrication in wind turbines are being met by PAG oils.
The low velocities and high surface loadings on the gears in these units have resulted in micropitting problems with conventional hydrocarbon oils that have been overcome with PAG-based fluids. In other gearbox applications, especially worm gears, the naturally low coefficient of friction found in PAG fluids results in energy savings, lower temperatures and lower wear rates.
Versatility Meets Performance
For more than 60 years, synthetic lubricants have provided a viable alternative to traditional hydrocarbon lubricants. Each type serves unique roles, with PAG oils performing in both high- and low-temperature environments, in areas of extreme pressure and where water solubility is desired.
Polyalkylene glycol can be designed to form a wide variety of polymers. The design of the polymer can be tailored to the lubricant application to provide, for example, the desired viscosity, pour point, solubility and other attributes.
This versatility and the applications in which they are used shows that PAG oils account for about 24 percent of the entire synthetic lubricant market. Low pour points, a wide range of viscosities, resistance to varnish formation, increased solvency and a wide range of solubility all add to PAG lubricants’ reputation as a high-performance synthetic lubricant on the market.
With continuing emphasis on environmentally acceptable lubricants in industry, these qualities will continue to push PAG oils to the forefront of the synthetic market.
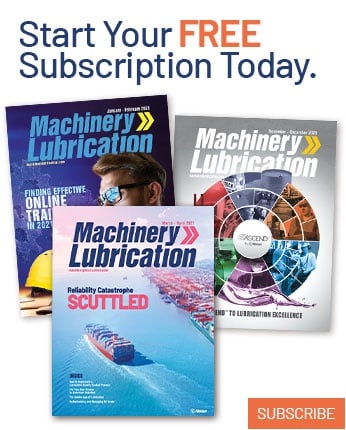