The objective of a root cause analysis (RCA) is to identify what happened, why it happened, and what can be done to prevent it from happening again. It involves examining the problem and considering evidence from several diverse perspectives.
Fluid degradation can be responsible for many kinds of equipment failures. A lubricant in service is subjected to a wide range of conditions which can degrade its base oil and additive system. Such factors include heat, entrained air, incompatible gases, moisture, internal or external contamination, process constituents, radiation and inadvertent mixing of a different fluid.
(Courtesy of Thomassen Turbines)
Degradation Mechanisms
Following is an overview of some common fluid degradation mechanisms. The relationship between oil analysis and degradation mechanisms is examined in Figure 2.
Oxidation
Oxidation is the reaction of materials with oxygen. It can be responsible for viscosity increase, varnish formation, sludge and sediment formation, additive depletion, base oil breakdown, filter plugging, loss in foam properties, acid number increase, rust and corrosion. Controlling oxidation is a significant challenge in trying to extend the lubricant's life.
Thermal Breakdown
In a mechanical working environment, the temperature of the lubricant is a primary concern. In addition to separating the moving parts of the machinery, the lubricant must also dissipate heat. This means the lubricant will sometimes be heated above its recommended stable temperature.
Overheating can cause the light ends of the lubricant to vaporize or the lubricant itself to decompose. This can cause certain additives to be removed from the system without performing their job, or the viscosity of the lubricant may increase.
At temperatures greatly exceeding the thermal stability point of the lubricant, larger molecules will break apart into smaller molecules. This thermal cracking, often referred to as thermal breakdown, can initiate side reactions, induce polymerization, produce gaseous by-products, destroy additives and generate insoluble by-products. In some cases, thermal degradation will cause a decrease in viscosity.
Microdieseling
Also known as pressure-induced thermal degradation, is a process in which an air bubble transitions from a low-pressure to a high-pressure zone, resulting in adiabatic compression. This may produce localized temperatures in excess of 1,000°C, resulting in the formation of carbonaceous by-products and accelerated oil degradation.
Additive Depletion
Most additive systems are designed to be sacrificial. Monitoring additive levels is important not only to assess the health of the lubricant, but it also may provide clues related to specific degradation mechanisms. Monitoring additive depletion can be complex depending upon the chemistry of the additive component.
Electrostatic Spark Discharge
When clean, dry oil rapidly flows through tight clearances, internal (molecular level) friction within the oil can generate static electricity and may accumulate to the point where it produces a sudden discharge or spark. These sparks are estimated to be between 10,000°C and 20,000°C and typically occur in mechanical filters.
Contamination
Foreign substances can greatly influence the type and rate of lubricant degradation. Metals such as copper and iron are catalysts to the degradation process. Water and air can provide a large source of oxygen to react with the oil. Therefore, a contaminant-free lubricant is ideal and monitoring a fluid's contamination levels provides significant insight to the machine's health.
Figure 2. Analytical Tools Assess Lubricant Degradation
Rethinking Lubricant Root Cause Analysis
The Italian economist Vilfredo Pareto created a mathematical formula describing the unequal distribution of wealth, observing that 20 percent of the population own 80 percent of the wealth. This theory is known as Pareto's Principle and has been applied to countless situations since.
Pareto's Principle can also be applied to equipment reliability in that 20 percent of equipment failures account for 80 percent of the loss. Therefore, having the knowledge and tools to correct the critical 20 percent represents a large opportunity for organizations to improve reliability.
Root cause analysis (RCA) is a term used regularly in lubrication circles. However in the authors' experience, it is an instrument rarely utilized correctly. RCA should be performed on chronic, recurring problems or failures that become more serious over time.
Most lubrication-related RCA is based on a routine analysis of the oil and the technician's assumptions, which wastes an organization's valuable resources. The failure to correctly identify a root cause is usually not because of a lack of knowledge within the individual or team tasked with the RCA.
In fact, the expertise of the team is precisely the problem in many cases, because the investigation may be lead toward their own predetermined conclusions. When selecting a person or team to conduct a RCA, remember that they must possess characteristics such as expertise in multiple disciplines, training and experience in RCA, and persistence.
The most important task in conducting a successful RCA is to logically interpret collected data and investigate without making assumptions. False assumptions and predetermined conclusions are the primary reason RCAs end without soundly documented conclusions or with incorrect findings.
RCA must start with an understanding of the problem and its potential causes. A list should be generated identifying every possible cause. Care should be taken to not assign blame at this point in the investigation. For each potential root cause, experiments and tests should be constructed to test theory validity.
Keep in mind that data proving any theory false (the devil's advocate approach), is as important as the normal approach - because this can also be used to support the correct root cause and destroy incorrect assumptions.
Utilizing Oil Analysis in Fluid Degradation RCA
The following discussion lists some of the tools available, specifically for identifying fluid degradation issues.
Primary Tests for Fluid Degradation
Membrane Patch Colorimetry (MPC) or Quantitative Spectrophotometric Analysis (QSASM)
This is a laboratory method of extracting the insoluble contaminants from a used oil sample, followed by spectral analysis of the separated material. With QSASM, a direct correlation is made from the color and intensity of the insolubles to oil degradation.
The test is designed to identify soft contaminants (those directly associated with oil degradation), and is not strongly influenced by larger hard contaminants unrelated to oil degradation. This test is considered to be highly sensitive and reliable for detecting subtle changes in insoluble levels. The MPC test method is currently in draft format as a new ASTM standard. The QSASM test is a commercial version of the method performed by Analysts, Inc.
Fourier Transform Infrared Analysis (FTIR): ASTM E2412
Infrared spectroscopy is a method used to measure the chemistry of organic molecular components. FTIR can be applied to monitor additive depletion, organic degradation by-products and the presence of various contaminants. It is a good primary test for measuring chemistry changes of the fluid basestock, in addition to identifying the degradation mechanism that may be responsible for the fluid degradation.
Ultracentrifuge (UC), Sedimentation Rating
This is a method to isolate all insolubles in a sample. It is accomplished by spinning the sample at 20,000 RPM in a centrifuge for 30 minutes. The insolubles are separated from the fluid centrifugally, allowing a visual sediment rating scale to be used. The minimum value of one represents low levels of insolubles.
The maximum value of eight represents a critical level. Limitations of the test include the inability to differentiate between oil degradation by-products and other insoluble contaminants (dirt). Unfortunately, the centrifugation process may also remove additives (VI improvers, dispersants and sulfonates) and may be laborious to run.
Secondary Tests for Fluid Degradation
Viscosity: ASTM D445
Viscosity can be defined as the resistance of a fluid or semisolid to flow and is considered the most important property of a lubricant. It can also be affected by various forms of fluid degradation. Maintaining the proper viscosity is crucial to retaining oil film thickness. However, once a meaningful change in viscosity has occurred due to degradation, several other performance factors (an increase in insolubles, acidity, etc.) may have already been impacted, making it an excellent secondary test for fluid degradation.
Linear Sweep Voltammetry (LSV): ASTM D6971
This test is designed to detect the oxidative health of a lubricant by measuring the primary antioxidants in the fluid. It is performed using an instrument called the RULER and is an essential condition monitoring tool for lubricant health. The level of remaining additive, and thus remaining useful life of the lubricant, is determined by comparison to original levels. The results of LSV can be correlated to fluid degradation, provided a significant amount of data is available from that particular fluid type.
Rotating Pressure Vessel Oxidation Test (RPVOT): ASTM D2272
An important property of lubricating oil is its oxidation stability or resistance. The RPVOT test (previously RBOT) is a controlled, accelerated oxidation test of a lubricant used to measure the performance of remaining antioxidant additives. Results are then evaluated and compared to new oil levels.
This method has limited value as a primary RCA test because fluid degradation may take place on isolated segments of the lubricant, causing insolubles to be created without meaningful drops in RPVOT values. It is not uncommon for sludge and varnish problems to occur in oils even with high RPVOT values. In fact, several lubricants with high RPVOT values have additive chemistries that are more prone to produce deposits such as phenyl-alpha-naphthylamine (PANA).
Acid Number: ASTM D974, D644
This tool measures the acidic constituents present in the lubricant. Most rust inhibitors used in oils are acidic and contribute to the acid number of the new oil. Increases from the new oil level are monitored, which typically reflect the presence of acidic oxidation products.
Increases in acid number could also be attributed to contaminants, mixtures of products and/or chemical transformations. Although this is a valuable tool, it views the chemistry that forms after a problem is already present, and is inherently insensitive to weak, organic acids which are produced during lubricant degradation.
Other Useful Analytical Tools in RCA
Pentane/Toluene Insolubles: ASTM D-893
This test is used to determine the level and composition of insoluble contaminants in a lubricant. The level of contamination is derived from measuring material that can be mechanically separated from the fluid by a centrifuge. The composition and origin of the material are obtained by identifying the contaminant's solubility in pentane and toluene.
Two procedures are referenced in the ASTM standard; one with coagulant added to the base solvent, and one without. The first portion of the procedure requires a representative lubricant sample be mixed with pentane and centrifuged at a defined RPM for a specified time period.
The amount of material deposited in the tip of the tube represents oil-insoluble, resinous matter that may originate from fluid and/or additive degradation (soft contaminants). This material is measured and identified as the pentane insolubles. In the second portion of the method, following the determination of pentane insolubles, the remaining deposit is mixed with a toluene-based solution, recentrifuged and the fluid is decanted.
The remaining deposit is composed of material associated with external sources of contamination, wear debris or densely carbonized matter generated from high-temperature thermal events (hard contaminants). Variations of this test method include membrane filtration with toluene rinse.
Delta MPC or QSASM
Numerous chemical and physical mechanisms may cause an oil to degrade and produce insolubles once it is isolated from the circulating system. This condition is called autodegradation. One cause of autodegradation is when the lubricant contains a depleted antioxidant additive system and a large number of free radicals.
Free radicals are a reactive chemical species generated from lubricant degradation. Antioxidants halt free radical propagation (chain-reactions) which if not prevented, will result in the formation of insoluble by-products, the precursor to varnish. Autodegradation can cause the creation of insoluble contaminants in low or no-flow sections in a lubricating circuit, leading to varnish. Often, lines leading to inactive valves are susceptible to autodegradation and subsequently, when the valves are used, they stick.
Electrostatic spark discharge and microdieseling are two degradation mechanisms known to cause autodegradation due to their ability to create a large number of free radicals in an isolated area. The autodegradation cycle typically reaches an end point approximately 72 hours after the sample is pulled from the reservoir.
Autodegradation can be detected by comparing an on-site MPC or QSASM test to the results of a laboratory test conducted at least 72 hours later. The test is called Delta MPC or QSASM because the changes in the value of the test are observed over time. A significant change in results indicates the occurrence of autodegradation.
High-pressure Differential Scanning Calorimetry (HPDSC): ASTM D6186.
This is a tool that is used to measure the oxidation induction time of lubricating oils under oxygen at 500 psig and elevated temperatures (130°C and 210°C). Many researchers believe this tool relates to RPVOT or RULER in its ability to test for the oxidation life expectancy of the lubricant.
Because the sample size is small, bulk solution effects are minimized and it is possible to observe good interchange of the sample with its atmospheric oxygen. This allows good repeatability of the test procedure with a reasonable reaction time.
Gas Chromatography (GC/MS)
This is a separation technique that is applied to the light ends of a lubricant. It can be used to separate portions of the lubricant's base stock, as well as many of the smaller additives. Using this technique, the refinery controls the production process of the actual basestock.
When linked to a mass spectrometer detector, the GC/MS can also identify the components being separated. The mass spectrometer detector can increase the detectability of the compounds being separated. When using the GC/MS, the concentrations of additives, such as antioxidants, can be measured to as low as 10 ppm.
Thermogravimetric Analysis TGA: D6370, D5967
TGA is a tool that measures the weight loss of a sample as it is heated in a controlled environment. The tool allows the different components present to be studied by observing their vaporization temperature or decomposition points. The amounts of organics (oil, polymer), carbon black and ash in the sample can be identified.
Flash Point: ASTM D92
This is a method that measures the minimum temperature at which an oil vapor will support combustion for at least five seconds. Various forms of thermal degradation will produce lightends that have the ability to lower the lubricant's flash point. Flash point is a common test used to determine the presence of fuel dilution in a used lubricant.
Dissolved Gas Analysis (DGA): ASTM D3612
DGA is an analytical test that measures the dissolved gases in oils through gas chromography. Certain degradation mechanisms cause a lubricant's hydrocarbon molecule to crack, producing light end gases that are entrained in the oil. The type and distribution of these gases can indicate which degradation mechanism is responsible.
Gases that are useful to examine when applying this test to fluid degradation include hydrocarbons (methane, ethane, ethylene and acetylene), carbon oxides (carbon monoxide and carbon dioxide) and hydrogen. Researchers have attempted to identify the specific gases produced once the hydrocarbon molecule is cracked (temperatures in excess of 300°C). Acetylene, for example, is created at temperatures greater than 1,000°C.
Color: ASTM D1500
When fluid rapidly changes colors, this may indicate accelerated oil degradation, a mixture of oils in service or contamination with another product. Color is an important characteristic to monitor over time. Oil darkening is often caused by chromophores created in the degradation process.
In addition, certain additives produce distinct color bodies after depletion. It is important to note that some fluids may have not undergone a color change and could still be degraded to dangerous levels, and vice versa.
Scanning Electron Microscope/Energy Dispersive X-Ray Spectrometer (SEM/EDS)
SEM/EDS uses a high-energy electron beam reflects off the surface of an object providing detailed three-dimension visual observations, while also identifying the object's elemental composition. This is a powerful tool in examining deposit formation, metallurgical analysis and failure analysis.
Nuclear Magnetic Resonance Spectroscopy (NMR)
NMR is a tool similar to FTIR in that it allows the molecular properties of the lubricant to be studied. By applying a magnetic field to the molecule, certain atoms yield a nuclear spectrum that is affected by its chemical environment. For oil analysis, the most commonly used atoms that can record NMR spectra are hydrogen (¹H), carbon-13 (¹³C) and phosphorus (³¹P).
NMR is closely related to MRI (magnetic resonance imaging), which is used to capture images of soft tissue damage in human medicine. This tool allows research of detailed structural information concerning the sample's chemistry.
Gel Permeation Chromatography (GPC)
GPC is a technique that physically separates the sample by the molecular size of its components. It is valuable for the study and separation of high molecular weight materials from the base oil, additives and formulated lubricants. These materials include many of the oxidation condensation products.
Spectrochemical Analysis: ASTM D6595, D5185
Elemental spectroscopy is an analytical method to measure and monitor specific trace metals for wear and corrosion levels, airborne or internally generated contaminants, and certain additives. Particles detected are typically 8 µm or less and the results are reported in parts per million (ppm) by weight.
Water Content: ASTM D6304, D1744
Water contamination within oil systems adversely affects the lubricant by acting as a catalyst for oxidation and depleting water-sensitive additives (also called additive washout). Water also promotes rusting, corrosion, microdieseling and filter plugging. Results are reported in parts per million (ppm) by weight.
Particle Count: ISO 11171, ISO 11500, NAS 1638
This is a test designed to count the number of particles present greater than a given micron size per unit volume of fluid. The results reflect the insoluble contaminants present within that size range and are applied to assess fluid cleanliness and filtration efficiency. Cleanliness levels are also represented by the ISO 4406 classification system to classify the particles larger than 4 µm, 6 µm and 14 µm per milliliter of fluid.
Root cause analysis is a powerful tool to methodically investigate reliability problems including lubricant degradation. Oil analysis is an excellent tool in the root cause analysis toolbox. Measuring chemical changes in the lubricant, along with the creation of insoluble contaminants is the first step in identifying fluid degradation.
Remember that one of the major pitfalls in lubricant root cause analysis is that assumptions are made by the investigators. As a result, problems are either incorrectly diagnosed or not solved. By approaching lubricant degradation issues with an open mind and by methodically applying oil analysis tools, the root cause of recurring problems can be solved.
Editor's Note
QSASM is a service mark of Analysts, Inc.
This is an abridged version of a technical paper that appeared in the Conference Proceedings from Lubrication Excellence 2006. The full-length article with case studies can be found in the LE2006 Proceedings.
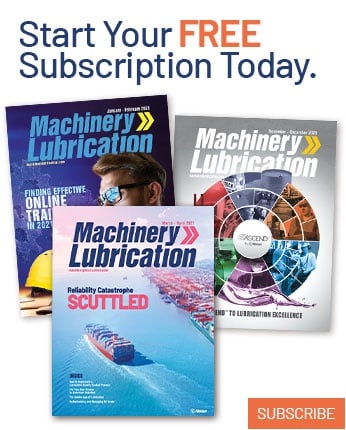