Synthetic gear oils are used whenever mineral gear oils have reached their performance limit and can no longer meet the application requirements. For example:
- at very low or high temperatures
- extremely high loads
- extraordinary ambient conditions
- if they fail to meet special requirements such as flammability
Even though additives can improve many properties of mineral oils, it is not possible to exert an unlimited influence on all their properties. This applies especially to physical properties like the following:
- thermal resistance
- low temperature properties (fluidity, pour point)
- flash point
- evaporation losses
Possible Advantages
Synthetic oils provide a number of advantages. However, they do not necessarily out-perform mineral oils in all respects and may even result in some drawbacks despite their advantages. The advantages of synthetic lubricating oils (depending on the base oil) include:
- improved thermal and oxidation resistance
- improved viscosity-temperature behavior, high viscosity index (in most cases)
- improved low temperature properties
- lower evaporation losses
- reduced flammability (in some cases)
- improved lubricity (in some cases)
- lower tendency to form residues
- improved resistance to ambient media
Possible Disadvantages
Possible disadvantages include:
- higher price
- reactions in the presence of water (hydrolysis, corrosion)
- material compatibility problems (paints, elastomers, certain metals)
- limited miscibility with mineral oils
Application-related advantages often prevail, increasing the use of synthetic lubricants as gear lubricants, especially under critical operating conditions. The most common synthetic types used include synthetic hydrocarbon oils (SHC), polyglycols (PAG) and ester oils (E).
Lubricating Oils Based On Synthetic Hydrocarbon Oils
Synthetic hydrocarbons are similar to mineral hydrocarbons in their chemical structure. They have nearly identical properties relating to their compatibility with sealing materials, disposal, reprocessing and miscibility with mineral oils. The main advantage is their excellent low temperature behavior. It is possible to manufacture food-grade lubricants for the food processing and pharmaceutical industries with SHC base oils using special additives.
Lubricating Oils Based On Polyglycols
These lubricants ensure especially low friction coefficients, which makes them suitable for gears with a high sliding percentage (worm and hypoid gears). With the appropriate additives, they provide excellent antiwear protection in steel/bronze worm gears, and have a good extreme pressure performance.
In gear systems, higher polarity polyglycols allow greater interaction on the metal gear surface. This gives polyglycols mild extreme pressure performance even without additives.
Polyglycol oils may have a negative impact on sealing materials and may dissolve some paints. At operating temperatures above 212°F (100°C), only seals made of fluorinated rubber or PTFE are resistant. Before using PAG oils in production applications, it is advisable to test compatibility with paints, seals and sight glass materials.
Miscibility with mineral oils is limited; mixtures should therefore be avoided. Polyglycols are neutral toward ferrous metals and almost all nonferrous metals. If the application has a loaded contact with one component consisting of aluminum or aluminum alloys (rolling bearing cages containing aluminum), there may be increased wear under dynamic load (sliding movement and high load).
In such cases, compatibility tests should be conducted. If a worm gear is made of an aluminum bronze alloy, polyglycols should not be used because the reaction in the load zone could result in increased wear.
Lubricating Oils Based On Ester Oils
Ester oils are the result of a reaction of acids and alcohols with water splitting off. There are many types of esters, all of them having an impact on the chemical and physical properties of lubricants. In the past, these lubricating oils were mainly used in aviation technology for the lubrication of aircraft engines and gas turbines as well as gear systems in pumps, starters, etc.
Ester oils have a high thermal resistance and excellent low temperature behavior. In industrial applications, rapidly biodegradable ester oils will gain importance because it seems possible to achieve the same efficiency as with polyglycol oils by selecting an appropriate ester base oil.
Certain ester oils may exhibit low hydrolytic stability. Hydrolysis is the cleavage of the ester into an alcohol and an acid in the presence of water. Ester lubricants need to be hydrolytically stable because they are often exposed to humidity in use. In practice, hydrolysis may be a less serious problem than commonly reported. The hydrolytic stability of an ester depends on:
- the type of ester used
- the type of additives used
- how the ester was processed
- the application
Application-Related Advantages of Synthetic Lubricating Oils
The following application-related advantages result from the improved properties of synthetic lubricating oils as compared to mineral oils:
- improved efficiency due to reduced tooth-related friction losses
- lower gearing losses due to reduced friction, requiring less energy
- oil change intervals three to five times longer than mineral oils operating at the same temperature
- reduced operating temperatures under full load, increasing component life; cooling systems may not be required
Reduction of Gearing Losses and Efficiency Improvement
Because of their special molecular structure, synthetic lubricating oils based on poly-alphaolefins (a type of SHC) and polyglycols ensure that tooth-related friction is considerably lower than with mineral oils. It may be up to 30 percent lower than if a regular mineral gear oil with EP additives was used. Because the friction coefficient of synthetic oils is lower, tooth-related friction is reduced, thus increasing the gear’s efficiency.
The efficiency of gears with a high sliding percentage, worm and hypoid gears, for instance, may increase up to 15 percent if a synthetic oil is used instead of a mineral oil. Even in the case of spur, helical and bevel gears (which have a naturally high gear efficiency), it is possible to increase gear efficiency of up to one percent by using a synthetic gear oil.
This may not seem like much at first, but it may result in considerable cost savings depending on the nominal output of the gear unit, especially in the case where several gears are deployed.
Table 1. Potential Reduction of Gearing Losses and Improvement of
Efficiency if Using a Synthetic Gear Oil Instead of a Mineral Oil. |
||
Type of Gear |
||
Effect |
Worm Gears, Hypoid Gears
|
Spur and Helical Gears, Bevel Gears with Axis Not Offset
|
Reduction of Total Losses | 30% and more | 20% and more |
Improved Efficiency | 15% and more | up to 1% |
Reduction of Operating (Steady-State) Temperature | 68°F (20°C) and more | up to 54°F (12°C) |
Table 1 shows the extent synthetic oils can reduce gear losses, especially in gear systems with a high degree of load-dependent losses.
Advantages of Synthetic Gear Oils Based on Reduced Friction
Increased Gear Efficiency
- Smaller gears with smaller motors can provide the same power output
- Higher power output can be achieved with the same power input
Reduced Oil Temperatures
- Extension of the oxidative life (five times longer than mineral oils in some cases)
- Extended component life (where reduced wear and friction is achieved)
- Cooling systems may no longer be required
Reduced Energy Consumption
- Reduced costs for electric current or fuel consumption resulting from lower total energy losses in the gearbox; 30 percent and more for worm gears
- Costs for electric power have been reported as high as 10 percent
Improved Efficiency and Reduced Wear When Using Synthetic Oils
Tests show synthetic oils make gears more efficient than mineral oils. A polyglycol oil in the study resulted in the highest degree of efficiency: 18 percent more than the high performance mineral gear oil. SHC gear oil also made the test gears eight to nine percent more efficient. Its performance as a food-grade lubricant in accordance with USDA-H1 is also an excellent added advantage. Food-grade lubricants are often thought to be inferior to normal lubricants, an opinion which this study seems to disprove.
Synthetic base oils have excellent wear protection behavior, which is enhanced by appropriate antiwear additives. Wear is particularly low when the PAG gear oil is used.
Extended Oil Change Intervals Using Synthetic Oils
Synthetic oils have better resistance to aging and high temperatures and a longer service life than mineral oils. Depending on the base oil (SHC or PAG), the oil change intervals may be three to five times longer at the same operating temperature.
Approximate oil change intervals of gear oils at an operating temperature of 176°F (80°C) are:
- Mineral oil: 5,000 operating hours
- SHC oil: 15,000 operating hours (extension factor 3)
- PAG oil: 25,000 operating hours (extension factor 5)
Synthetic oils have a lower friction coefficient than mineral oils in a gearbox and a more favorable viscosity-temperature relationship. This generally permits the use of synthetics at lower viscosity grades and also offers the possibility of reduced oil temperature during operation. In such cases, the life extension factors for oil change intervals of synthetic oils are longer than the values stated above, which refer to identical oil temperature.
The following comparison of test results illustrates this advantage. Three lubricants were tested in a splash lubricated worm gear test rig.
The test records show the following oil sump temperatures after 300 operating hours:
Mineral oil: 230°F (110°C)
SHC: 194°F (90°C)
PAG: 167°F (75°C)
The life extension factors of synthetic oils as compared to mineral oil are as follows:
Mineral oil = 1
SHC = 9.5 times longer
PAG = 31 times longer
Synthetic Oils Help Save Maintenance and Disposal Costs
As compared to mineral oils, the oil change intervals of synthetic oils may be five times longer under the same thermal conditions. Despite the fact that the purchase price and the costs of disposal of synthetics are higher than that of a mineral oil, the extended oil change intervals can offset these costs when taking into account the gear unit’s extended service life.
A comparison of the costs for mineral and synthetic offers real opportunity to reduce maintenance cost and improve machine reliability. There is also the advantage of reduced environmental impacts with lower lubricant disposal rates.
Selecting the Gear Oil Type
In order to select which type of gear oil to use in a gearbox, you must understand the gearbox’s mode of operation. The application factor (KA) identifies the type and magnitude of load the gears will experience.
Viscosity
Viscosity is the most important physical property of a lubricating oil. Because the viscosity changes with temperature, the rate of change is an important property identified by the Viscosity Index (VI). Most mineral-based gear oils will have a VI of 95. A lower VI indicates that the oil’s viscosity changes to a greater extent with change in temperature.
Conversely, a higher viscosity index indicates a much lower rate of change in viscosity with respect to change in temperatures. The advantage of a high VI is that in lower temperatures, the oil will tend not to increase viscosity as much as a lower VI product. The ability of an oil to maintain a small viscosity differential over the operating range of the gearbox provides a more consistent lubricating film to the gears and more predictable wear performance.
Viscosity Selection
As stated earlier, the correct viscosity is an important parameter in proper selection of a gear oil. The manufacturer of the gearbox or gear system generally offers a viscosity recommendation and these recommendations should be followed in most cases. If the OEM of the gear unit has not provided a recommendation and the viscosity has not been calculated based on lubrication theory, it can be selected in accordance with various worksheets and graphs. The differing viscosity-temperature and viscosity-pressure behavior of synthetics as compared to mineral oils should also be taken into account.
The correct viscosity must be selected independently of any specific gear stage, realizing that a compromise is required for multistage gears. The selection of the correct viscosity is based on the oil’s expected operating temperature, such as sump temperature or the temperature of the injected oil.
This temperature is calculated by determining the gear’s thermal economy, taking into account the frictional losses; or in the case of gears already installed, by measuring the temperature of the sump.
It might be required to select a lower viscosity to ensure lubricant is supplied during a cold start or at lower ambient temperatures. In each individual case, it is necessary to check the viscosity at the existing starting temperature, especially in the case of oil circulation systems.
A typical worksheet method for determining the viscosity required for a spur gear drive and a worm gear drive starts with the calculation of the force-speed factor. Because of different viscosity-temperature (VI) behavior of different oils, different ISO viscosity grades are selected for the same Kluber Viscosity Number.
This article presents only a few of the important factors in gear lubricant selection. Technical and performance specifics about lubricants lead to better, more precise decisions in making lubricant selection.
It is also helpful to use a reputable lubricant supplier who is knowledgeable in selection options that affect energy consumption, machine life, lubricant consumption and waste oil generation. Included in these options should be the consideration of synthetic lubricants.
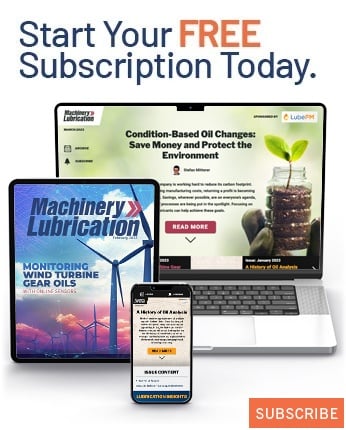