Free and emulsified water can cause contamination in critical fluids, resulting in additive depletion, oxidization, bacterial growth, component wear and corrosion. Before signs of water contamination occur (cloudy appearance of the oil), it is also possible for bearings to lose up to 75 percent of their potential service life. Water causes damage even in its dissolved state, attacking the base stock, additive package and machine. Additionally, water carries organisms that can potentially disable critical hydraulic systems.
Industry's standard method of reporting water content is either as a percentage of the volume or in parts per million. Although the methods are useful, this is not where the testing should end. As a result, Kittiwake developed the ANALEXrs moisture sensor to detect the moisture content of water in oil up to the oil's saturation point. This is the amount of water the oil will dissolve before becoming saturated, or once it can no longer absorb water. The sensor expresses this moisture content as percent relative humidity, where 100 percent is the saturation point.
Above this saturation point, any additional water will sit in the oil as water droplets, or it will form an emulsion. This free water can be detrimental to systems, for instance:
-
Free water can react with the oil's additive package, rendering the oil unsuitable for the application.
-
Emulsion can reduce the film thickness in bearings and other moving parts, which accelerates wear.
-
Free water can settle in machine sumps, pistons and filter housings, resulting in corrosion.
The Sensor
As maintenance costs increase and production capacity and equipment efficiency are maximized, remote online sensor technologies are being recognized as the new cost-effective form of analysis. The ANALEXrs range of online sensors are designed to provide plant engineers and maintenance managers with real time, continuously monitored testing and analysis data for critical plants and equipment. The ANALEXrs moisture sensor, which forms part of this range of online sensors, goes beyond the normal water screening tests to indicate the actual dryness of the oil. Providing percent relative humidity (RH) and temperature values, monitoring can now occur in real time. Personnel can ensure oil is always below the saturation point before free and emulsified water forms. The sensor monitors one of the root causes of the machine and lubricant failure, water.
With self-diagnosing, digital and analog outputs, the new sensor can be integrated into existing condition monitoring and operating control systems, and can be mounted within any lubrication system and machine type.
The ANALEXrs moisture sensor measures the oil's percent relative humidity (RH), resulting from the dissolved water within the lubricant, using a combination of proven thin film capacitance sensors combined with smart algorithms to provide a temperature and percent RH value. Using internal processing power, the self-diagnostic sensor does not require handheld units to analyze or display results, which can be reported using standard displays or PCs. Whether verifying the health of a machine or an alert of changing moisture ingression rates, the moisture sensor provides instant information, which compliments existing laboratory programs.
The moisture sensor head allows only water molecules to penetrate its special polymer coating. The sensor monitors the dielectric property of the polymer layer, which has been affected by the water absorbed into the polymer. This water content is reported as a percentage, indicating the humidity of the oil. Once all oil molecules contain dissolved water molecules, the oil can no longer dissolve water. Therefore any additional water will remain as free water. Applications
Moisture sensors do not need to be in the oil itself, and can be used in the headspace of a piece of machinery, such as a gearbox. High moisture levels that move through a failed breather to the airspace above the oil will dissolve into the oil. This is a good place to monitor moisture, before it enters the oil. Installing a moisture sensor in the headspace above each seal means as soon as the humidity reaches a threshold, commonly at 60 percent, an alarm is raised. This method of condition monitoring illustrates how alarms can trigger investigations, thereby avoiding critical failures and unplanned downtime.
It is suitable for use with diesel engines, gas turbines, gearboxes, compressors, generators and other lubricant-filled equipment. These sensors help to increase productivity, reduce costs and improve profitability.
ANALEXrs equipment can be fitted on any machine with a circulating lubricating system, and where atmospheric, process or coolant issues are a concern. Industries that benefit from the ANALEXrs equipment include:
-
power generation (steam, nuclear and wind turbine)
-
steel
-
pulp and paper
-
petrochemical
-
transportation
-
military
-
marine
Moisture sensors from Kittiwake form part of a range of new online sensors for condition monitoring and maintenance experts. The ANALEXrs range of online sensors include total ferrous wear debris (PPM), particle content (ferrous and nonferrous) and oil condition (oil quality units).
About KittiwakeKittiwake was developed in 1991 with the goal of providing rugged, portable tools for fuel and lubricant analysis in the marine industry. The Kittiwake test kits have since been utilized in marine, offshore and industrial applications. The company's recent growth strategy involved developing a range of industrial water testing kits and equipment to complement the measuring and monitoring approach of fuels and lubricants. In 2003, Kittiwake purchased Analex to enhance its oil analysis product range.
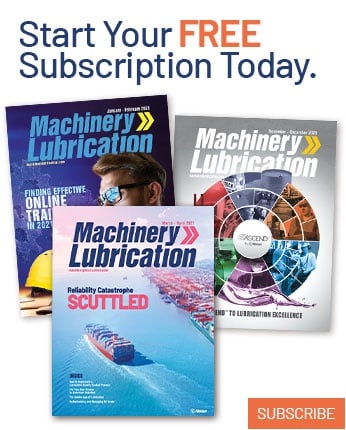