This article delves into my diverse career journey — from a refinery worker to an industrial lubrication consultant and now as a technical digital solutions expert in the water industry. I will explore how water, a major contaminant for lubricants, connects these fields and highlight the similarity in asset challenges and maintenance practices in both industries.
I will also share a case study of a 1997 fire incident in a cooling tower, emphasizing the tower's significance, maintenance, and its role in sustainability goals. Cooling towers, functioning on the principle of evaporation, play a vital role in removing process heat, minimizing thermal pollution, and enabling water reuse in industries. Specifically, I highlight the challenges faced by gearboxes in cooling towers due to extreme operating conditions, necessitating meticulous maintenance despite difficulties in accessibility.Cooling Tower Lubrication Reliability
The cooling tower's lubrication system employs either splash or oil mist lubrication methods. Given the challenging accessibility of gearboxes in large-scale cooling towers, the choice of gear oil becomes a critical factor in enduring and performing effectively under demanding conditions.
Typically, the gear oil used for lubrication comprises mineral or synthetic base oil with an ISO VG 150 or ISO 68 rating, depending on the fan's speed and the level of investment by management. Synthetic oils are recommended for applications involving severe duties, extended service intervals, very high operating temperatures, limited equipment accessibility, high expected debris density, and the need to reduce oil disposal.
For the electrical motors within the gearboxes, smaller ones are usually sealed for life, incorporating ZZ bearings. Larger motors above 75 hp are lubricated with ISO 68 mineral oil. However, gear oil encounters various challenges, such as overheating and foaming caused by moisture and particle ingress, frequent top-ups due to excessive oil consumption, and the primary issue of limited accessibility for data collection and sampling. This typically occurs because the driving mechanism is typically located under the fan hood.
A real-life example from northern India illustrates the repercussions: a captive power plant faced an unplanned two-day shutdown due to gearbox failure leading to the stoppage of the fan. This resulted in management incurring approximately $30,000 USD in downtime costs, encompassing expenses for gear replacement, maintenance workers, and the entire system's restart. The issue was traced to broken gear teeth resulting from highly contaminated oil. However, even with the significant downtime costs, it was still deemed less than the production loss during that period.
Here are some basic tips I'd suggest for gearbox maintenance:
- Install an offline filtration unit to avoid particles and moisture ingress.
- Equip the gearbox with a desiccant breather (with the extended rod modification) to increase the breather’s life too.
- High-quality sight glasses for quick inspection
- Install and routinely inspect BS&W (Bottom Sediment and Water) bowls.
- Periodically monitor oil temperature using thermography to identify any hot spots.
- Conduct comprehensive oil analyses on a scheduled basis, ranging from quarterly to semi-annually.
- Consider adopting mist lubrication to coat the internal surfaces and prevent corrosion.
- Ensure Proper alignment with coupling and drivers.
- Install magnetic plugs and inspect periodically for abnormal wear debris.
- Label the gearbox with the appropriate lubricant identification.
- Set and periodically check proper cleanliness and dryness targets.
- Install a minimess valve for fixed and live zone oil sampling points.
- Select and maintain high-quality seals and upgrade them when necessary.
- Ensure the integrity of mounting bolts and platform.
- Maintain outer cleanliness with proper housekeeping.
In addition to the aforementioned general recommendations, it's highly recommended to integrate IIOT (Industrial Internet of Things) devices onto equipment to revolutionize the culture of reliability. This integration facilitates quicker decision-making, enhanced equipment uptime, and drives significant business advancements.
IIOT devices, which are cloud-based technologies installed on critical assets, provide real-time information, continuous monitoring, and analysis of parameters round the clock. Their role is vital in achieving industrial objectives related to asset reliability, sustainability, equipment availability, the prevention of premature failure, and more.
Devices such as online particle counters and moisture sensors contribute by supplying data for immediate interpretation and integrating it into actionable workflows, thereby reducing human error in activities like sorting test reports, sampling, and manipulation. This notably enhances the reliability of oil analysis.
Similarly, ultrasound technology, employed in maintenance and condition monitoring practices, aids in leak detection and the prevention of over-greasing, while also supporting predictions related to bearing life, among other benefits.
Cooling Feed Water Maintenance
Now, considering the feed for the cooling tower, it primarily consists of the circulation cooling water. Industries utilize diverse sources of makeup water, such as municipal or government-provided water, seawater, surface water from rivers or lakes, and desalination water. These sources vary in terms of dissolved solid content, contaminants, cost, and chemical composition, directly impacting the operational and maintenance efficiency of the cooling system.
Throughout the entire operation of the cooling tower, two distinct yet interconnected sub-systems require attention: water circulation and heat efficiency. Both are integral components that demand careful management to ensure optimal performance.

Water Circulation
During the heat-exchanging process, the addition of make-up water to the cooling tower is determined through a simple assessment based on the water mass balance of wastewater and evaporated water. When referring to wastewater, it denotes the losses incurred during the tower's operation, which can be categorized as follows:
Evaporation Loss: This represents the water lost purely due to evaporation. The quantity of evaporation isn't typically a focus for water efficiency improvements.
Drift Loss: This accounts for the volume of water carried away from the tower in the form of mist or small droplets. Drift eliminators or baffles control this loss, typically amounting to around 0.02% of the total volume within the system.
Blowdown Loss: As water evaporates from the system, dissolved solids are left behind, increasing the potential for corrosion or scaling. This concentration is managed by the controlled release of water through blowdown procedures.
Basin Leakages or Overflow: These issues arise due to improper operational practices. It's essential to regularly check system valves to ensure there are no unreported losses and to maintain the basin level using float control equipment.
Heat Efficiency
Heat efficiency can be affected by common challenges faced in the cooling water system, which you can resolve with the following tips:Corrosion - The phenomenon of reversion of metal to the natural oxide state. Cooling water systems provide an ideal environment for the same. |
|
Scaling - The precipitation of insoluble minerals like calcium carbonate or magnesium silicate after the supersaturation point. |
|
Fouling - Deposition of suspended solids during the heat exchange equipment. Foulants can come from external sources such as dust around a cooling tower or internal sources such as products of corrosion or process leaks. |
|
Microbial growth - In this environment, bacteria, algae, and fungi can grow, multiply, and cause deposit problems and human health issues too. |
|
Monitoring and regulating water chemistry within acceptable limits is an essential responsibility. Failure to maintain these parameters can result in decreased system efficiency or production loss. Let's briefly review the key parameters of water chemistry:
pH: This measures the concentration of hydrogen ions on a scale from 0 to 14. An acidic pH (below 7) can cause corrosion, while a basic pH (above 7) can lead to potential scaling.
Alkalinity: This measures the solution's buffering capacity or the base's ability to neutralize acid. It not only aids in regulating the water's pH but also helps control high concentrations of metals.
Conductivity and Hardness: These reflect the presence of calcium and magnesium ions, which lead to scale formation by precipitating mineral particles. The Langelier Saturation Index (LSI) gauges water stability concerning scale formation. A positive LSI suggests a higher likelihood of scale formation, a negative reading indicates a corrosive environment, while an LSI between 0 and 1 is considered neutral.
Oxidizing Biocide Concentration: This assists in inhibiting the growth of microorganisms in the water system using oxidants like chlorine, bromine, or chlorine dioxide. Oxidation-reduction potential measures the oxidizing or reducing strength.
Turbidity: This refers to water cleanliness. Higher turbidity signifies dirtier water, usually caused by erosion, suspended particles, or wastewater. Turbidity in make-up water can be managed through appropriate treatment methods.
To enhance the quality of make-up water, a water treatment skid should be installed in the cooling tower. This skid should include components for:
- Clarification
- Filtration/Ultrafiltration
- Ion Exchange/Softening
- Chemical Feed
Additionally, regular water analysis focusing on the mentioned parameters is crucial for effective water treatment.
Automated Monitoring
The incorporation of automated monitoring distinguishes a standard skid from an IIOT-designed skid. The advanced skid is equipped with probes that measure all water chemistry parameters. When any deviation is detected, it promptly generates notifications, delivering them to users within minutes. With real-time data readily available, swift action can be taken to interpret deviation reports and expedite troubleshooting, thereby enhancing equipment efficiency.
Conclusion
Bringing together both lubrication and cooling feed water aspects in enhancing asset performance through IIOT applications, condition-based maintenance (CBM) integrated with IIOT offers real-time data and alerts for prompt action, mitigating secondary losses and yielding tangible benefits when approached seriously. The absence of live data, resulting from the traditional analog methods, leads to fragmented and irrelevant values, ultimately impacting reliability and effectiveness.
Maintaining the quality of supporting and operational media within designated parameters is crucial. Failure to do so can cause auxiliary equipment to draw excess power, thereby compromising sustainability goals. Each drop of water, every joule of energy, and reductions in carbon footprint are interconnected with asset performance and can be attained through robust management practices.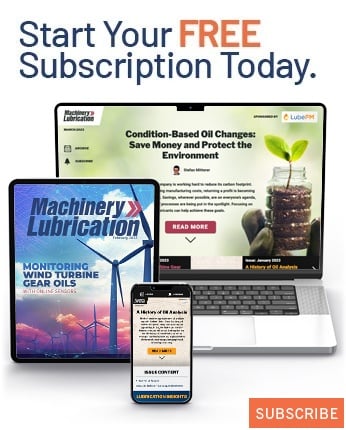