Oxidation is the most predominant reaction of a lubricant in service. It is responsible for numerous lubricant problems - including viscosity increase, varnish, sludge and sediment formation, additive depletion, base oil breakdown, filter plugging, loss in foam control, acid number (AN) increase, rust formation and corrosion. Therefore, understanding and controlling oxidation is a priority of the lubricant chemist.
Many new oil formulation tests (such as ASTM D4310 - the sludge and oxidation test, turbine oxidation stability test (TOST) D943 and D4485 - the engine oil performance categories) and used oil analysis tests (such as fourier transform infrared (FTIR) oxidation ASTM D2412, linear sweep voltammetry (LSV) RULER™ - ASTM 6971, QSAsm and acid number D664) are used to study this lubricant's nemesis.
Common Oxidation Indicators
Every lubricant is designed with an oxidation controlling method. The formulation of each lubricant, therefore, contains antioxidants. These antioxidants are designed to be sacrificial, meaning they react or oxidize before the remainder of the lubricant (the base oil) to provide protection.
This protection is the only mechanism saving the lubricant from premature failure. To develop a lubricant, the chemist should know what types and how much of these antioxidants to incorporate into the formulation. Anyone monitoring the used fluid's life expedience should also track these additives.
This article discusses oxidation with respect to the tools used for monitoring this problem.
Table 1. Oxidation Test Conditions
The Steps of Oxidation
The oxidation of a hydrocarbon fluid involves three basic steps: initiation, propagation and termination.
With these steps in mind, oxidation can be managed through the control of one or more of its steps or phases. This is achieved by limiting the source of oxygen (the initiation), shortening the number of reaction cycles (the propagation) or adding alternate stopping methods (increasing termination). To some extent, all of these methods are employed in the lubricant formulation. The initiation starts the process, and preventing oxygen is the first line of defense.
Understanding what is causing the propagation steps can also enable the decrease of oxidation. The termination step stops the cycle. Antioxidants are used to break into this propagation and form radicals that are stable, thus halting the cycle. One of the most effective testing methods for understanding the health of the fluid is to be aware of the health of these antioxidants.
Figure 1. Oxidation Analyses from Sequence Testing
Temperature
Heat is often employed to accelerate the oxidation process because temperature has two effects on any reaction. The first effect involves activation energy. If the system does not contain enough energy to push the reaction over the threshold, nothing will happen. The second effect is related to the speed of the reaction. A reaction (oxidation) will approximately double in rate for every 10°C (18°F) increase in temperature. Which means that the oil life will be reduced by one-half for every 10°C (18°F) increase in temperature.
Tests are often developed to study the fluid's oxidation that has resulted with an increase in temperature or an addition of a catalyst. For convenience, these modifications of "real life" are used to conduct a test in a shorter time frame.
The application of these methods is often useful; however, the resulting data should always be carefully studied because it may not agree with the fluid's behavior in real-life applications. Additional reaction pathways can become the major pathway and mislead the researcher.
Analysis
Although most lubricants are formulated with antioxidants to control oxidation, the inevitable breakdown cannot be prevented. For this reason, many tests have been developed to evaluate the oxidation state of the lubricant. Some of these tests study the potential lifetime of the lubricant while others look at the results of oxidation.
Oxidation Reserve
When an oil formulation is designed, a series of tests is required for this formulation to meet. Regardless of the formulation's ultimate application, the test series always includes several oxidation tests. The oxidation test requirement (time, temperature, catalyst, atmosphere and interpretation methods) is designed around the lubricant's application.
In most cases, the remaining oxidation reserve is measured by testing the lubricant's behavior under an oxidation experiment. For example, rotary pressure vessel oxidation test - RPVOT (D2272), universal oxidation test (D6514), turbine oil stability test - TOST (D943), universal oxidation test (D5846) and pressure differential scanning calorimetry - PDSC (D6186) are used to study the oxidation potential of a turbine oil.
The tests differ in the reaction temperature or concentration of oxygen. A lubricant is often measured by several of these tests to assess the temperature effects of the lubricant.1 Because a lubricant is operating in multiple temperature zones, testing at different temperatures provides a better assessment of the lubricant's overall quality.
Figure 2. FTIR Spectra of an Engine Sequence Test
Test Methods
Except for the PDSC and RPVOT, the resulting oxidized lubricant from the above test is also evaluated by another oxidation consumption or property test method. The oxidized lubricants are analyzed by tests including base number, AN, FTIR oxidation or viscosity change. This evaluation further indicates the lubricant's oxidation state.
In the automotive sector, crankcase lubricants are subjected to engine tests (D4485) designed to cause severe oxidation, forcing the lubricant to easily oxidize in a short time. The resultant used oil is measured for BN, AN, FTIR-oxidation and viscosity to determine speed and amount of oxidation. These engine tests are analogous to the actual use that the lubricant could be subjected to in the field, but at a shorted interval.
Figure 1 shows an example from one of these test studies. The effects of the acids reacting to lower the base reserve, BN, are clear, while the oxidation cannot immediately be observed in the FTIR or viscosity regions.
Oxidation Profile
These results are common when trending the lubricant's oxidation profile. As oxidation occurs to the lubricant, it depletes the antioxidants and produces carboxylic acids. The base reserve will neutralize these oxidation-produced acids to carboxylate salts; thus, resulting in a depletion of the base reserve. As previously discussed, many of the esterification and condensation reactions that produce viscosity increases are acid catalyzed.
The base reserve will help prevent this chain growth and viscosity problem. Therefore, in addition to the corrosion problems of the acid components, it is important to prevent BN from getting too low or AN too high. The oxidation reaction produces esters and carboxylate salts (from the base reserve neutralization); however, carboxylate salts are not being measured by the oxidation analyses2 even though it is an oxidation product.
Figure 2 shows how oxidation is progressing in this complex experiment. The lowest plot (line) in the figure was generated on an oil sample early in the test. Successively higher lines are generated from additional oil samples taken during the test.
In Figure 2, the acids can be observed at 1,715 cm-1, while nitrate oxidation is at 1,631 cm-1 and carboxylate salts at 1,555 cm-1. All the components in the 1,800 to 1,500 cm-1 range are oxidation-related components.
Figure 3. LSV (D6971) of New and Used Turbine Oil
Protection
The majority of analytical tests that measure oxidation protection measure the amount of oxidation that has occurred to the lubricant. The Linear Scanning Voltammetry (LSV) (D6971) and FTIR are two tests capable of measuring the concentration of the antioxidant additive(s) present in the oil to control oxidation.
The LSV is an application of linear sweep voltammetry (LSV), which utilizes a sweep voltage to measure both amine and phenolic antioxidants (Figure 3). When calibrated against the new oil, the remaining antioxidant concentration can be determined to estimate the lubricant's remaining oxidative life.
Similar information can be obtained from FTIR. As shown in Figure 4, the phenolic and amine antioxidants are visible in the FTIR spectrum. Like LSV, the peak area of the FTIR spectrum can be used to quantitate the antioxidant's concentration.
The remaining lifetime of the lubricant obtained from both FTIR and LSV can be expressed only as a percentage of the new oil life. It can be related to the number of hours of oil life remaining only if the historic life of the oil is known in hours and the application's conditions have remained stable. For systems like turbine oils that have controlled operations, there can be established contaminations limits for the percentage useful life.
Figure 4. FTIR Spectrum Showing Antioxidants
Oxidation Progress
A common method for studying oxidation is to trend its progression. Oxidation results can be followed by measuring the increase in the acid number of the fluid (or the loss in base number in engine oils caused by the formation of acids), viscosity (caused by the formation of condensation products), FTIR carbonyl oxidation (the ketones, aldehydes, esters and acids formed form the oxidation reactions) and insoluble products.
Although certain tests like the Pentane/Toluene Insolubles D893 measure both hard and soft insolubles, applying tests like Pentane Insolubles by Membrane Filtration D4055, QSAsm3 or the filter paper Blotter Spot Test can also follow the amount of oxidation products. In the case of oxidation, measuring the formation of condensation products that are insoluble in the fluid is tracking or monitoring the oxidation.
Performing these different methods and following the results can provide an understanding of the root cause and mechanism of oxidation. For example, if oxidation occurs at low temperature, significant FTIR oxidation and a small amount of insoluble products will be apparent.
On the other hand, high temperatures can cause condensation reactions and increase insoluble products. Many thermal-cracking processes (like microdieseling or combustion) will promote oxidation, but will also produce nitrates that can be observed through FTIR nitration as a flag of the process.
Other less widely utilized tests have been used to measure oxidation. The most promising of these methods employs the measurement of the electrical polarity or permittivity of the fluid.5, 6 Both the real and imaginary parts of the impedance measurement contains information about the fluid.
The real parts of the impedance, the conductivity, and the imaginary part, the permittivity or dielectric coefficient, are both affected by the change in polarity of the fluid. Oxidation is a major source of this change in lubricant polarity. Therefore, new sensor technologies are emerging that utilize these resistance-related measurements to assess the oil quality, in many cases as a real- time measurement.
Although oxidation has been studied for more than 140 years, it remains to be fully understood. Fluid chemistry, reaction temperature and reaction conditions are varied in testing experiments in an attempt to predict the in-service behavior of the lubricant.
Tests have been designed to measure oxidation reserve (the amount of protection remaining) and oxidation progress (the amount of oxidation that has occurred). Both testing methods have their advantages, and the effectiveness of these tests depends on the operation of the in-service fluid. The better that a test can measure what is occurring, the more information is available concerning the life of the fluid.
Understanding how the fluid is handling the oxidation problem can enhance the attempt in correcting this root cause of fluid failures. The lubricant chemist should be aware of the measuring tools available and what they may indicate. Therefore, one can address and potentially reduce this source of fluid failure.
References
1. V. Gatto, W. Moehle, T. Cobb and E. Schneller. "Oxidation Fundamentals and Its Application to Turbine Oil Testing." ASTM Symposium on Oxidation and Testing of Turbine Oils. December 5, 2005, Norfolk, Virginia.
2. Annual Book of ASTM Standards. "E2412." American Society for Testing and Materials. West Conshohocken, Penn., 2000.
3. QSAsm is a registered service mark of Analysts Inc. (www.Analystsinc.com).
4. G. Trujillo. "The Blotter Spot Method." Practicing Oil Analysis magazine, July-August, 2003.
5. C. Koehler, D. Wooton, D. Sosnowski and R. Hirthe. "Fluid Condition Monitoring Using Broad Spectrum Impedance Spectroscopy." U.S. Patent Application 20050110503.
6. C. Collister. "Electrical Measurement of Oil Quality." U.S. Patent 6,459,995.
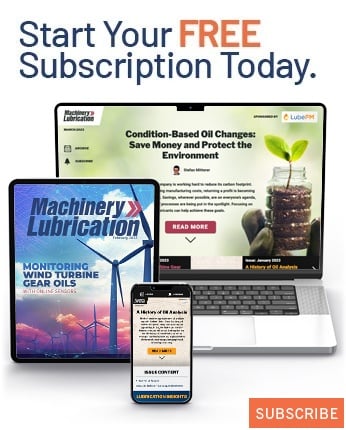