The year was 1984, Ronald Reagan was the President, the average price of a gallon of gas was $1.13 and “Wake Me Up Before You Go-Go” was at the top of the music charts. This catchy song from the group WHAM! was wildly successful and launched George Michael's career to new heights. Who would have thought that a song from what many consider the worst decade of music could hold a message about lubrication, or more specifically about how lubricants degrade?
Amongst the most common degradation pathways of lubricants is the oxidation of the base oil. This process involves the intake of oxidation and the production of highly reactive molecules that not only damage the surrounding base oil but can also impact the equipment health in a variety of manners. Long has oxidation been the bane of extended oil life, and many industries closely monitor it. However, the approach to proactively managing oxidation has a lot to do with what we allow in contact with the fluid in the first place. This is where WHAM comes into the story.
The leading catalysts for oxidation can be remembered using this simple mnemonic device:
W – Water
H – Heat
A – Air
M – Metals
These four agents working together greatly increase the oxidation rate and shorten the lubricant's usable life. Our job is to control each of these and reduce their interactions with the lubricant as much as possible. Some are more easily controlled than others though.
While most lubricants will oxidize eventually, we do have help in delaying the process or at least managing the results of oxidation to a point. The vast majority of lubricants will be formulated with antioxidant additives that function in multiple ways to minimize the impact of oxidation. These additives deplete as they work to slow or delay oxidation. Some of these additives can neutralize or decompose some of the highly reactive free radicals and hydroperoxides associated with oxidation.
Monitoring these additives has become an important aspect of lubricant analysis, especially for equipment utilizing large volumes of lubricants, such as turbines and other machinery with circulating oil systems. The lyrics in the song “Wake Me Up Before You Go-Go” definitely apply to the monitoring aspect of these additives.
In many cases, we want to carefully consider the additive levels to help determine our next course of action. As they deplete to an unsafe level, we may focus on our next full oil change or perhaps even a partial change, known as a bleed-and-feed, to buy us time until a scheduled outage occurs, at which point a more thorough change could occur.
Oxidation causes a dual course of devastation. On one hand, oxidizing promotes the formation of acids, which, if left unchecked, can lead to corrosion. This is especially true in equipment with softer metallurgy, where the acid can pit surfaces, leading to significant damage. The other aspect of oxidation is the production of larger molecules that eventually increase viscosity and, ultimately, the sludge, tars, and varnish that appear inside the equipment.
Varnish has become especially problematic in the industry as it creates surface deposits that reduce dynamic tolerances, reduce heat transfer ability, and produce sticky surfaces that can trap abrasive particles, leading to increased wear. Regardless of the path of destruction, neither is beneficial, and we can delay them from becoming problematic with diligence. To do this, we need to focus on WHAM!
Water
Water can impact the lubricant in many ways but increases the oxidation rate. Water promotes the formation of acids and free radicals, which oxidizes the oil quicker. It also leads to the formation of emulsions, which increases the fluid's surface area, creating more interactions with oxygen.
Keeping water out of the lubricant requires multiple efforts. Most oils are hygroscopic, meaning that they absorb moisture from the air, so any air in contact with oil needs to be as dry as possible. Dry air purge systems or desiccant breathers can be used to do this.
Sanitation activities such as washdowns can be a source of water ingression, and care should be taken to seal equipment against ingression by properly outfitting the machine with seals, sight glasses, quick connects, breathers, or any other accessories that reduce the need to open the equipment during maintenance.
Water can be removed from the oil, and depending on the quantity and the state of coexistence, this can be straightforward. Free water, water that has separated completely from the oil, can simply be drained out and removed. If the water is emulsified, utilizing water-removing filter elements can be a simple approach. Dissolved water is the hardest to remove and likely requires vacuum dehydration or similar, more aggressive removal strategies.
Heat
Heat is the catalyst that increases the rate of oxidation and other chemical degradation processes within the oil. Often cited is the Arrhenius rate rule, which says that chemical reactions double every 10°C increase in temperature. This applied to oxidation means the rate of oxidation doubles with the same step in temperature, so the oil life is effectively cut in half. We want lubricants to operate as cool as possible.
In most cases, heat is difficult to avoid and is present due to the nature of the operation (friction) or because of the environment (ambient heat, close proximity to ovens, etc.). In either case, we try to guard the equipment against excessive heat. This may include shading for equipment exposed to direct sunlight or heat shields for equipment installed close to hot areas of the process.
Controlling heat is largely a task for heat exchangers and housekeeping. You want to ensure the equipment is kept clean to promote the dissipation of heat from the case of the equipment to the environment. Heat exchangers are used when passive cooling isn’t adequate. These devices may utilize fans or cooling fluids to promote faster removal of heat from the systems. For smaller pieces of equipment where these may not be economically feasible, we should ensure we are using the correct viscosity and fluid volume so as not to unnecessarily create more drag and fluid friction that would compound the issue.
Air
Of course, for oxidation to occur, there must be oxygen present. The air that exists within the system is the source of most of this oxygen. Our equipment typically operates at atmospheric pressure, especially splash-lubricated machines and most fluid reservoirs. At these conditions, oil holds air in a dissolved state, up to 10% by volume. As oil experiences turbulence and movement through a system, bubbles can form and start to suspend through the fluid volume. This is entrained air and represents one of the areas of most concern with air contamination.
Suction leaks, turbulent reservoir conditions, and impaired surface tension of the oil are all mechanisms that can lead to entrained air. Once these bubbles are in the system, they hang out in the oil volume and increase the area of the oil in contact with air. This further promotes oxidation and the byproducts mentioned earlier.
To control this, we need to ensure the oil stays healthy, which in turn ensures the oil's air release properties remain intact. We want the air to rapidly separate from the oil. To further aid in this, we want reservoirs to be as calm as possible, so the addition of baffles, diffusers, and other devices to slow down the movement of the oil can make a huge impact on the amount of entrained air that is allowed to move throughout the system.
Metal Catalysts
Like microscopic spark plugs, the metal particles suspended in the oil greatly impact the rate of oxidation. These particles can react with the air in the system, creating more reactive oxygen species that then attack the oil. They can also react with hydroperoxides in the oil, making more reactive molecules that increase the rate of oxidation and acid formation. Also, the metal surfaces provide a site for oxidation reactions to occur, allowing oxidation to occur more rapidly.
Most of our equipment is comprised of metal, so its presence is not uncommon. However, it is the small wear particles that can cause us great concern. These particles are released from the machine surfaces during operation and then allowed to move throughout the system, coming into contact with more of the lubricant. As their concentration grows, the more surface area is present through the system, which increases the rate of oxidation.
To reduce these impacts, we must ensure that our equipment is mechanically sound and operating well. This includes maintenance activities such as alignment, balancing, and solid mounting to ensure that the equipment isn’t unnecessarily producing wear. Correct viscosity and additive packages to minimize wear are crucial from a lubrication aspect. We pair this with proper filtration to remove these fine particles and other wear-producing particles, such as dirt, to minimize the wear-particle population. Keeping the metal particles low helps slow down the oxidative process.
While you may not have the greatest opinion on the band or the song, it doesn’t mean that there aren’t lessons to learn here. Keep in mind that WHAM is largely controllable, and if we focus on it, we can greatly increase the life of our lubricants. Much like the song says, “I’m not planning on going solo.” Get your team involved in these improvements, as everyone involved in the lubrication program has a role to play in keeping these contaminants out of the equipment.
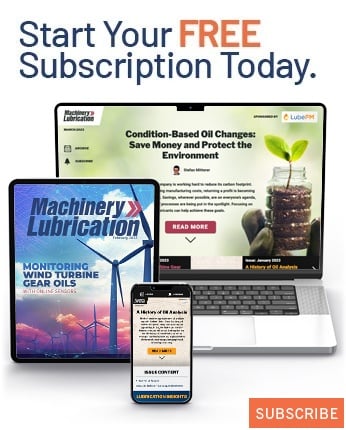