The defoamant (also known as antifoam agents and foam inhibi tors) is a common additive in many types of lubricating oils and hydraulic fluids. As the name implies, the purpose of the defoamant is to retard the formation of stable foam on the surface of the oil in the sump, gearbox, or reservoir.
Silicones, or compounds containing silicone, and acrylic copolymers are popularly used in mineral-based lubricant formulations. Lighter grade turbine oils and hydraulic fluids are generally formulated with acrylate anti-foam additives while heavier gear oils, paper machine oils, and crankcase lubricants may use silicone.
When stable foam is allowed to form there is considerable risk that effective lubrication will not be achieved. In many cases foam is merely a cosmetic concern. In other cases it is quite serious and can lead to premature failure of the oil and machine.
Foam is considered a problem and must be treated if any of the following occur:
1. The oil level in the sump or reservoir becomes impossible to control
2. The oil spills onto the floor creating a safety hazard
3. The foam leads to air locks and inability to effectively supply oil to lubricated components
4. The foam inhibits heat transfer and encourages oxidation and thermal failure of the oil
5. The equipment is lubricated with foam instead of oil
There are many possible causes of unacceptable levels of foam. Some relate to the conditions of the oil and others are mechanical in nature (see table). A mechanical problem may be associated with over agitation from high return/drain flows or a low oil level. If foam collapses quickly when a machine is at rest, then a mechanical problem should be suspected.
Troubleshooting Foam Problems
Air Release (IP 3B Test Method) | Foam Stability (ASTM D892 or IP 146) | |
Mechanical Problem (exessive aeration) | Same as new oil | Same as new oil |
Air Detrainment Problem (oil doesn't release bubbles) | Increase from new oil | Same as new oil |
Depleted or Ineffective Defoamant | Increase from new oil | Increase from new oil |
Oil related problems might be due to degraded air release properties (caused sometimes by too much defoamant or silicone leaching into the oil from gasket/seal material) or by ineffective or depleted defoamant. In order for the defoamant to be successful in inhibiting foam formation it must possess each of these properties when suspended in the oil:
1. It must have surface tension lower than that of the fluid
2. It must not be dissolved in the oil
3. It must be dispersed into small droplets within the fluid (best around 10 microns)
Often these three conditions are not met, either initially with the new oil, or later as the oil ages. Although there is a common test used to evaluate an oil’s foaming tendency (ASTM D 892) it is often too time consuming and expensive for routine used oil analysis.
Therefore other methods must be employed to estimate the foaming tendency risk. This can be done by simply assessing the probability of failing to meet the three properties listed above. It is worth noting that in many applications a depleted or ineffective defoamant may not, in itself, lead to foam or air release related problems.
Surface Tension
Newly formulated lubricants will generally have high original surface tension (30-35 dynes/cm). The microscopic globules of defoamant will typically have surface tension in the range of 20-24 dynes/cm. This differential is essential to insuring that a weak spot on foam bubbles form allowing them to break.
As oil ages its surface tension is constantly declining. A variety of things contribute to this including moisture contamination, solid impurities, oxidation, grease/STP contamination, floor soaps and detergent contamination, and other common polar suspensions.
This causes the overall surface tension to fall into the range of the defoamant which reduces or eliminates its effectiveness. While surface tension is not commonly evaluated by oil analysis laboratories the many impurities previously mentioned can be.
Such tests as particle count, total insolubles, ultracentrifuge, patch test, FTIR for oxidation/water, TAN, and color can be used to help reach a conclusion as to whether there has been an appreciable loss of surface tension.
Undissolved Defoamant
Often new oils will have silicone levels in the range of 10-25 ppm coming from the presence of the defoamant. Although the concentration is small, the silicone is supersaturated in the oil in microscopic globules.
If the silicon level drops too low, say below 5 ppm, there is risk of it being in the dissolved state as opposed to the required undissolved (supersaturated) state. One known cause of the depletion of silicone is its removal by filtration.
A study by Chevron has shown that the finer the filter the greater this tendency. And, the defoamant droplets can also coalesce over time resulting to more rapid settling in quiescent fluid zones. The easiest way to monitor the silicone is by common elemental analysis. Compare the silicon level of the new oil to that of the used oil. If it drops below 5 ppm consider foam tendency to be a risk.
Droplet Size
This is difficult to evaluate in used oil. One possible test is to put a sample quantity of the oil into a glass beaker. Then, very slowly pour the oil over the rim of the beaker. If lumpy globules of the silicone appear flowing over the rim (called fish eyes) this is a good indication that the silicone has coalesced or was initially improperly suspended in the oil. This is a common problem when defoamant is retrofitted into a used oil (called sweetening).
Another way to crudely assess foaming tendency of used oil is to place a sample quantity of the oil into a blender. If a stable foam forms after agitation it is safe to conclude a loss of defoamant performance due to either of the reasons above. It is usually a good idea to practice with new oil to provide a comparison.
It is also worth noting that viscosity has an impact on foaming. The highest foaming tendency seems to peak around 280 cSt. Therefore, the influence of temperature may need to be assessed with gear oils having viscosities in this range at operating conditions.
The control and management of air and foam in reservoirs and sumps is essential to proper lubrication. To a large extent, oil analysis can be used to help identify changes in foaming tendency and depletion of critical defoamant additives. Over time, with practice and experience, reliable methods such as those described above should be routinely employed.
References:
Summers-Smith, J.D., “A Tribology Casebook,” Antony Rowe Ltd, Chippenham, Wiltshire, 1997
Awe, R.W., “Silicone Antifoams for Lubricating Oils,” National Fuels and Lubricants Meeting, Tulsa, OK, 1963
Friesen, T.V., “Transmission-Hydraulic Fluid Foaming,” International Off-Highway & Powerplant Congress & Exposition, Milwaukee, WI, 1987
Duncanson, Marianne, Exxon Company USA, “Sources of Air-in-Oil Problems in Circulating Systems,” Exxon Maintenance Conference, 1998
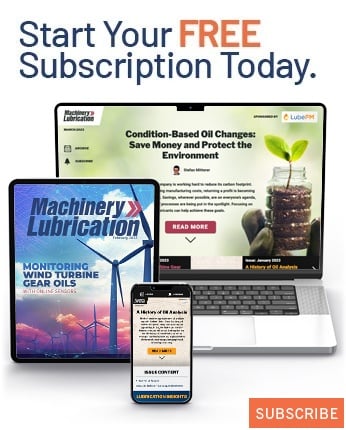