Thinking back to 2020, what lessons would you say you learned from the pandemic? Among all the changes and precautions we had to adopt, one thing many of us remember all too well is having to regularly sanitize our hands and check our hygiene before entering our homes and workplaces. We were forced to pay attention to all those little things in our everyday lives that we might’ve taken for granted in the past.
Likewise, industries such as machine reliability and tribology show us that 70% - 80% of machine failures are attributed to lubrication, which makes up around 1-3% of the total maintenance budget. Lubrication represents a 1:40 investment rate, which means that every $1000 spent on lubrication can yield a savings of $4000, resulting in 3,900% ROI!
The quality of the lubricants our machine consumes significantly impacts its productivity, longevity, and efficiency. How, then, do we properly check the quality of our lubricants?
While lubrication management techniques may differ between industrial facilities, a prevalent issue is the misconception that "new oil equates to clean oil." Upon arrival at a site, oil barrels are typically stored within warehouses or designated sheltered zones on the premises. Fluctuations in daily temperatures cause the barrels to expand and contract, and their exposure to sunlight, elevated temperatures, dust, dirt, moisture, and various weather-related conditions can result in contamination.
This marks the initiation of the lubricant's possible contamination, beginning even before actual operational use. At this stage, you must ask what events occurred before the barrels arrived at your location. Furthermore, what elements contribute to the compromise of oil quality before its receipt? Let's explore.
Stage 1: Production of Lubricants
Lubricants are produced by combining base oil and additives, and in the case of grease, thickeners are also added. These components are carefully mixed in specific ratios to align with the intended use requirements. This blending procedure encompasses various methodologies, which may involve utilizing air for stirring or employing sizable mixing equipment designed for meticulous blending within a controlled atmospheric setting.
Possible Concerns during this stage:
- Sanitation and cleanliness of the blending container
- The quality of the air utilized for agitation, ensuring it is devoid of moisture
- Verification of whether the components involved in the blending process undergo filtration
- The absence of a breather mechanism on the blending container
Stage 2: Intermediate Storage of Lubricants
Since lubricants are produced in substantial quantities, they are initially held in sizable reservoirs before their distribution to the designated location. Fresh intermediate containers are constructed based on volume needs, or previously utilized ones are repurposed.
Possible concerns during this stage:
- Presence of welding or grinding residue within new containers
- Insufficient cleansing of previously used containers
- Improperly installed breathers, leading to the infiltration of particles and moisture into the tanks
- Lack of options for filtration during the transfer of lubricants
Stage 3: Transportation of Lubricants
The delivery of lubricants to your site occurs in bulk quantities or batches. In bulk transportation, oil tankers are cleaned using either steam or diesel fuel. The hoses, pipelines, and interconnecting components employed in this process could introduce cleanliness concerns to the final oil product. Similarly, using drums or totes for batch deliveries also introduces potential chances for contamination.
Possible concerns during this stage:
- Lack of containers dedicated to specific types of oil and the materials used for these containers
- Risks of cross-contamination between different types of oils
- Insufficient handling practices lead to the introduction of contaminants when bungs, pipe connectors, and couplers are left open
- Inadequate flushing of used tanks or drums before subsequent use
Collectively, these factors compromise the necessary oil cleanliness to such an extent that they can adversely affect the system. The acceptable standards for oil cleanliness vary according to the specific applications. For example, servo valves require a higher degree of clean oil than gearboxes. It has been noted that even newly received oil at the site might have ISO codes of 21/19/16 or above NAS 10, indicating compromised cleanliness levels.
How and When to Perform Quality Checks for Lubricant Contamination
Let's now look at how we can implement quality check practices and programs at the onsite reception of lubricants to increase lubricant and system reliability and decrease contamination:
Inspect the lubricant container condition: Before arriving at your location, you can learn a lot about the state from the oil drum/container first by checking if the labels on the barrels are torn, broken or misprinted, or if they are clean enough to indicate their current storage condition. You can also create a checklist to monitor and record the label condition, manufacturing and expiration date to determine shelf life, batch number, supplier quality certificate details, inspection date and time, along with the signature of the quality inspector, reception environmental condition, and so on. The well-documented approach not only aids in lubricant quality control but also in training your teams on the necessity of reliability-centered or proactive maintenance.
Ask for the test certificate: The consumer has the right to ask for the test certificate of the lot along with the lubricants supplied at the site. Test certificates should have detailed information about the quality check before its dispatch, like oil analysis, test results, details of analysis performed, etc. Make sure to have this on hand, at least for the supercritical or critical machines.
Perform basic oil analysis: It is always suggested to randomly check a few samples from each batch to determine the ISO cleanliness level (particle counting), moisture, viscosity, and other basic tests. The plant can set up an onsite lab to perform the test in-house or select a neutral lab to provide the correct analysis detail within the required time. There are many benefits of establishing in-house labs, including rapid sample turnaround time, quality control for purchase and optimization of lubricants, awareness of knowledge of lubrication analysis, report interpretation, test limits, cost, and time savings, to name a few.
Conclusion
This article was originally published in Machinery Lubrication India and has been edited for content.
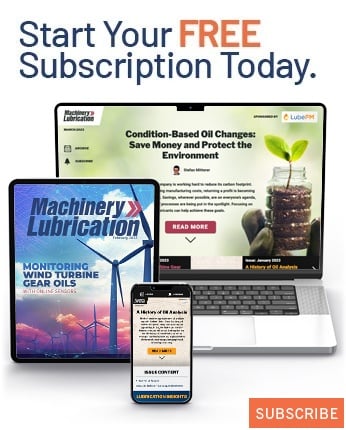