Maintaining properly lubricated machinery is an important part of any lubrication program. Without administering lubricant at correct intervals with the proper amount, a machine can experience costly failures. Centralized lubrication systems are a common tool used in industry to distribute a precise amount of lubricant to specific locations at specific times through the use of programmable timers, lubricant pumps and lubricant injectors. This buyers guide presents basic information for these centralized lubrication systems, as well as their availability through various vendors in the market today.
Background
Centralized lubrication systems were introduced in the mid-1930s. Since then, much research has concentrated on resolving the flow issues of viscous lubricants, such as grease, to deliver the fluid properly to its designated points. Advancements in technology have created today's centralized lubrication systems with precise delivery methods for a wide range of industrial applications. Centralized lubrication systems are sometimes referred to as automatic lubrication systems because they are completely or mostly computerized in the process of lubricant dispensing.1 These systems eliminate the risk of human error and increase precision when an application requires the lubrication of many components on numerous machines.
Centralized lubrication can deliver either grease or oil to a lubrication point. The basic operation of a centralized system includes the following: The system controller and injectors are preset to deliver a specific amount of lubricant at a specific interval. To deliver the lubricant, the lubricant pump is activated by the controller, via an air solenoid. This builds pressure in the lines, causing the grease to flow out of the injectors. A pressure switch is incorporated in the system to deactivate the pump once the lubricant injection is complete. In the last step of this process, the system directs any lubricant remaining in the lines back into the reservoir by venting.1
Technological advancements have created many products for controlling and monitoring centralized lubrication systems that further increase the precision and reliability of these systems. Lubricant injectors, system plumbing and lubricant reservoirs are commonly monitored by alarms. An alert signal is sent when an undesirable flow pattern exists or when the lubricant reservoir is low. Incorporating such alarms into a system is useful in preventive maintenance. Furthermore, to prolong maintenance intervals, high-capacity lubricant reservoirs can be incorporated into the systems and typically hold double the volume of the common system reservoir.
Centralized Lubrication Systems and Options
A centralized system can be categorized into the following:
-
positive displacement
-
flow proportioning
From the types of systems mentioned, the most distinctive difference is how the lubricant is injected during a lubrication cycle.
The positive displacement type uses metering pistons, and the flow proportioning uses restrictive orifices.
Figure 1 shows the basic layout of a single-line parallel system, which is an example of positive displacement, and Figure 2 shows injectors currently offered by Lincoln Industrial and Dropsa. The Lincoln SL-33 injector is an example of a single-line system, and the Dropsa divider valve delivers grease by progressive metering.
Many of the manufacturers of centralized systems have created their own complete systems to help you select a system that works best for you. For example, Lincoln Industrial provides the Centro-Matic single-line parallel system, Quicklub single-line progressive system, and Modular Lube single-line progressive system. Manufacturers of centralized systems can also customize to any specific needs.
The primary purpose for the addition of alarms on the system is to prompt the operator for immediate action in the event that a system failure occurs. Some common centralized system failures include3:
-
line failures - plugged, collapsed or broken
-
empty lubricant reservoir
-
dirty lubricant
-
pump or injector failure
Centralized lubricant systems can be monitored electrically, with pressure and level switches, or visually. Lubriquip provides a variety of monitoring and controlling devices for centralized lubrication. For example, Lubriquip's Lube Line, one of many products on the market, will alert the user of any undesirable grease flow patterns.
Figure 2. Lincoln Single-line Grease Injector SL-33
Selection
Centralized systems can be designed to fit almost any application with the lubricant pump and injectors selected based on lubricant weight and the distance it must travel to lube points. The weight of the lubricant and the supply-line distance affect the selection of pump and injectors because of the time required for the injectors to vent after an injection.
Most centralized systems allow for visual inspections to confirm operational status. Because of the complexity of these systems, other components that can aid in the overall system diagnostics of a centralized lubrication system should be considered. These include enhanced controlling and additional monitoring devices. The necessity of these accessories should be determined based on a compromise between reliability and the available budget for initial system costs. The potential for human error exists and oversight can occur during regular maintenance. Monitoring devices help to decrease this risk.
Components can be selected when designing a system that requires fewer monitoring devices than others. For example, monitoring progressive metering valves requires the alarm to focus on only one metering piston to determine the functioning of all the others. This is because of the positive hydraulic actuation.2
Conclusion
The primary purpose of a centralized system is to eliminate the tedious task of manually lubricating components on multiple machines. By accomplishing this, centralized lubrication systems offer two main benefits: increased machine reliability and single-person control from a centralized location. Many different systems available on the market can accomplish this task; however, care and thorough understanding of your system and applications are necessary in choosing the correct product for use.
Contact Information
Please see table for list of manufacturers, their contact information, and the products they offer.
References
1. Paul Conley and Raj Shah. "Ventmeter Aids Selection of Grease for Centralized Lubrication Systems." Machinery Lubrication magazine, January 2004.
2. D. Czichowski and G. Mehr. "Securing Green Wind Energy Production Through Centralized Lubrication." Evolution - the Business and Technology magazine from SKF.
3. Keith Stanbury. "Preventive Maintenance of Centralized Lubrication Systems - Key to Its Reliability." Machinery Lubrication magazine, January 2002.
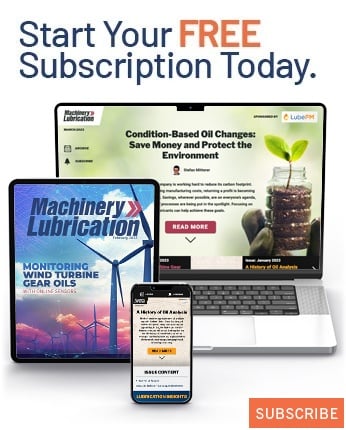