When it comes to the efficient and effective application of grease, a single point lubricator (SPL) can prove to be an extremely beneficial tool in our arsenal. Single point lubricators help engineers regularly and automatically deliver a small amount of grease or lubricating oil to a specific area, which:
-
Extend the life of bearings
-
Prevent extended downtime due to lubrication-related failures
-
Eliminate the human-error element

Because of their importance, it’s critical that we understand when it’s appropriate to apply this technology to capitalize on the available benefits for our teams and facilities. But oftentimes this is easier said than done.
SPLs are not a one-size-fits-all type of technology; there are many different types and variations available on the market that can meet a variety of greasing needs, and not all of them function the same.
So, before we start selecting SPLs at random and begin plugging them into all our bearings, there are several questions we should ask ourselves first to determine if a specific single point lubricator is justifiable for your specific application, or if you should stick with manual greasing practices.
Does the Bearing Require Frequent Lubrication?
Yes – Consider a single point lubricator.
No – Consider manual greasing.
Is the Bearing Difficult to Access?
Yes – Consider a single point lubricator.
No – Consider manual greasing.
Is the Bearing Critical to Equipment Operation?
Yes – Consider a single point lubricator.
No – Consider manual greasing.
Is the Environment Harsh or Dirty?
Yes – Consider a single point lubricator.
No – Consider manual greasing.
Does the Application Require Precise and Consistent Amounts of Lubrication?
Yes – Consider a single point lubricator.
No – Consider manual greasing.
By answering these simple questions, you can begin to determine if a single point lubricator is the best decision for your greasing needs.
When reviewing your answers, if your responses were all “no,” you most likely have no need for an SPL, but if you answered “yes” to at least one of the questions, you may in fact have a case for deploying a single point lubricator.
After you understand whether or not an SPL may be an appropriate solution for your facility, you will need to identify what kind you need.
To determine this, there are several factors that will need to be evaluated.
Will This Application Have High or Low Temperature Conditions?
- If so, you need to consider whether the SPL can withstand extreme temperatures.
-
Positive displacement pump SPLs handle these conditions better than those driven by a chemical reaction.
Are There Routine Inspections That Must Be Done Frequently?
-
Although the lubricating task may be more convenient with an SPL, it may be more beneficial to perform the greasing manually in order to encourage team members to physically visit a location and perform an inspection.
Is the Equipment Located in a Corrosive or Harsh Chemical Environment?
-
Some manufacturing chemicals have the potential to eat through single point lubricators, so you need to ensure that you aren’t setting yourself and your equipment up for failure.
Is There Adequate Space to Place the SPL?
-
Space is not always a limiting factor, but it is something that should be considered. While the possibility exists to install a remote SPL in a tight area, we still need to look at how far we will be pushing the grease and if the chosen SPL can adequately perform the task.
Are There Multiple Maintenance Points Close by That Are All Taking the Same Lubricant and Will All Use SPLs?
- When we run into a case similar to this, we need to ask ourselves if installing a centralized greasing system would make more sense. Though these systems may have a higher cost initially, the lifecycle cost would be much lower over time for this specific application.
While it’s easy to understand the appeal of defaulting to a single point lubricator when there are multiple tasks that are all a priority to complete, these units are meant to be a tool, not a crutch. We need to use informed forethought when it comes to making a decision on whether or not to utilize SPLs for our equipment – look at your reliability goals and ask yourself if they are truly helping you reach these goals. If the answer is no, don’t do it.
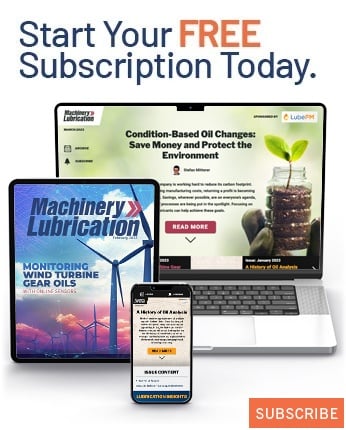