How can the stages of bearing failure in a plain bearing (not ball bearing) be detected on a turbocharger installed on a medium-speed engine burning heavy fuel oil? How can one detect the bearing failure using vibration analysis?
The basic operation of a turbocharger encompasses a turbine and a compressor on a common shaft. The turbine is driven by exhaust gas, which in turn drives the compressor that injects compressed air into the engine. This shaft can rotate up to 170,000 RPM.
The compressed air leaving the turbocharger can reach temperatures up to 200°C. This hot air is cooled by either an intercooler or aftercooler using water or air. This allows more air to be injected into the engine because cool air is more dense than hot air.
The bearings are generally lubricated by the engine oil, which is pumped through the turbocharger journal bearings and acts as both a lubricant and a coolant.
The journal bearings are a free-floating rotational type that floats on a six- to nine-micron film of oil. A free-floating bearing revolves around both bearing and shaft, and bearing and bearing housing. These bearing clearances are tight, and dirty oil can cause serious damage.
Origins of Turbocharger Problems
-
Damaged blade caused by contamination from dirt or other particles entering the turbine or compressor housing.
-
Low power or boost caused by a gas leak or blocked cooler restricting air injection.
-
Whistling caused by an air or gas leak.
-
Sluggish or seized turbocharger resulting from oil breakdown and degradation.
-
Worn or excessive clearance caused by low oil, contaminated oil, and dirt injection.
Other Causes
The best technique for dealing with turbocharger problems is to prevent them from occurring.
-
Use the proper synthetic oil recommended by the manufacturer.
-
Install a quality oil filter and change at recommended intervals.
-
Frequently sample the oil for contamination and additive depletion.
-
Repair any air leaks and sources from contamination injection.
-
Idle the engine for two to three minutes to cool down the turbo bearings before shutting off the engine, and thus the (cooling) oil supply.
Turbochargers have a high infant mortality rate, meaning they often fail early in their functional lives. This is primarily due to dirt and foreign contamination left in the chambers after rebuild or installation. For this reason, cleanliness cannot be over stressed.
Diagnosing Problems
Most diagnostics such as vibration analysis or infrared thermography will detect the problem at a stage only when damage is excessive.
Oil analysis is the best method for determining an impending problem before it reaches catastrophic proportions. Damage can result in a short time, and because of the high temperatures and speeds in these machines, proper maintenance - including clean and proper oil, oil analysis, eliminating air leaks and the shutdown procedure (three minutes cooling off before shutdown) - is critical.
Vibration analysis may be beneficial on a new installation or rebuild to check for balancing problems. It will also pick up a damaged blade and bad bearing, but not until the damage reaches the stage where a rebuild is necessary.
Journal Bearing Failures
There are several causes for journal bearing failures, including:
-
Lubrication contamination
-
Incorrect lubricant (viscosity and/or additives)
-
Environmental conditions (temperature)
-
Speed
-
Load (overloading and/or shock loading)
-
Balance
-
Shaft problems (bent or cracked)
-
Oil whirl
-
Rub
-
Loose foot
-
Misalignment
-
Metallurgical and manufacturing defects
A combination of oil and vibration analysis is the best approach to detect early signs of bearing failure. These two analytical tools can identify worn or damaged components at their earliest stages.
Journal bearings do not fail in the same way as roller bearings. Certain well-defined fundamental frequencies appear at different failure stages in roller bearings that are not as distinctive in journal bearings. Vibration analysis can still be used for diagnosing journal bearing problems; however the signs and symptoms vary and are generally not categorized as stage one, stage two, or stage three failures like roller bearings. In fact, some journal bearings can go from normal to complete failure in a matter of minutes.
Thermal imaging can be a useful tool especially when the bearing is inaccessible. Comparing thermal characteristics of both bearings on a common shaft with a balanced load can be used to identify potential problems. But again, this is a tool that will detect a problem only in the later stages of bearing failure and is not an alternative to oil or vibration analysis. A history of temperature over time is also beneficial for diagnosing machine-related problems with thermography.
Ultrasound can also be useful in areas where accessibility is a problem. The best use of this technology is direct contact with the bearing journal, but it can also detect frequencies and amplitudes from afar.
Related Reading
Eugene Matzan. "Detecting Premature Bearing Failure." Machinery Lubrication magazine, May 2007.
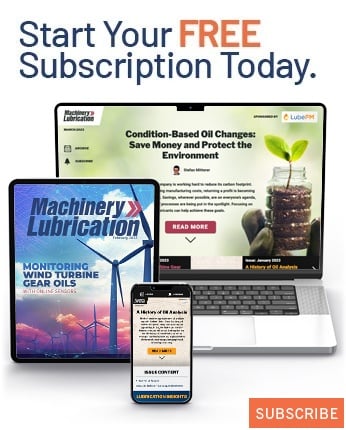