Making a lubricant is a bit like baking a cake. Unlike other forms of cooking, in baking, measuring ingredients with "a sprinkle of this and a pinch of that" doesn't cut it - they need to be precisely measured and combined. Mixing lubricants is similar to taking two cake recipes and attempting to combine them; sometimes it works, other times it flops. This is where the analogy ends, because a wrong lubricant mixture can result in a lot more trouble than a flopped cake.
In my experience working in different plants, I'm amazed at how endemic lubricant mixing can be. In a study conducted by BHP Billiton, it was found that 23 percent of gearbox failures were attributed to "wrong lubricants and lack of oil."
While I am not aware of the percentage of wrong lubricants as opposed to low oil levels, there is no doubt that using the wrong lubricant, including mixtures of lubricants, is a major cause of machine and lubricant failure.
In most cases, lubricant mixing occurs due to a lack of knowledge about the possible negative consequences, as well as just a lack of attention to detail.
Figure 1. BHP Billiton Reasons for Gearbox Failure
The Problems Caused by Mixing Lubricants
Mixing lubricants can cause issues for the lubricant itself and the machine. These issues include:
-
Incompatibilities between the base stocks, commonly encountered when switching between minerals and some synthetics.
-
Seal expansion or shrinkage issues, usually as a result of base oil changes, leading to possible leakage and seal failure.
-
Incompatibilities between additive packages. Problems here can include additive precipitation, loss of antiwear performance, loss of demulsification properties, reduction of oxidation stability, and the loss of storage stability when mixing lubricants in storage tanks.
-
With greases, incompatibilities between different types of thickeners. Grease thickeners are notoriously incompatible, and the wrong mixture or grease can result in consistency changes and excessive oil bleed. And just because a grease thickener is described as polyurea, for instance, does not mean it is compatible with other polyureas.
The Causes of Lubricant Mixing
Why is so much lubricant mixing taking place? Some of the more common reasons include:
-
Not specifying electric motor greases when purchasing or rebuilding. Motor manufacturers and rebuilders use their own in-house grease. Unless they are otherwise instructed, this will end up in the bearings of the motors. Therefore, one must specify on the purchase order the grease type to be used in the bearings.
-
Poor inventory control. If a situation arises where a large volume of oil is suddenly needed and there is not enough product available to cover the demand, then the alternative is mixing lubricants or shutting down the machines. To avoid this situation, make sure enough product is in stock to cover most scenarios, and ensure the distributor maintains enough stock at its warehouse and can quickly provide product if necessary.
-
Lack of lubricant identification.
-
Lack of knowledge concerning the dangers of lubricant mixing. This is a more prevalent problem in plants practicing the TPM model, and where people with little or no knowledge of lubrication are being asked to perform duties they are not trained or qualified to do.
-
Changing from one lubricant to another.
Issues to Consider when Faced with Mixing Lubricants
Situations arise when mixing lubricants is unavoidable, which typically occurs when changing from one supplier to another; when needing to change, for operational reasons, from one lubricant to another; or when an inadvertent lubrication mix has already taken place. Faced with one of these situations, the following must be considered:
-
Compatibilities of the base oil
-
Compatibility of the additive packages
-
In the case of greases, compatibility of the thickeners
A good place to start when considering a mixture of lubricants is with one or both of the lubricant OEMs. Their engineering departments should have access to compatibility studies, both between their own products and competitor's products, and may be able to provide a solution. Always use this as the first resource.
If the lubricant OEMs are not able to provide the answers, it is up to the user to conduct the testing. It is important to use the proper test method to gain the most accurate results, because most commonly performed oil analysis tests typically do not provide the user with relative information.
Strategies for testing mixed lubricants include:
-
In the case of oils, make mixtures by ratio of 90/10, 50/50 and 10/90. Test for filterability, sediment, color/clarity, RPVOT and storage stability.
-
In the case of greases, make mixtures by ratio of 75/25 and 25/75, and test for consistency, dropping point and shear stability.
-
In all cases, after a lubricant mix, planned or inadvertent, has occurred, make sure to continuously test the mixture until the consequences of mixing have been determined.
Avoiding Lubricant Mixing
In my experience, the biggest single cause of lubricant mixing is probably the lack of lubricant identification on both the lube-handling side (tanks, drums, containers) and on the machine side. The answer is simple and cheap to implement - institute a color-coding and tagging system. Once this is in place, the only chance of unplanned lubricant mixing comes from improper handling.
Again, it is easy to implement a comprehensive policy to manage transfer and storage practices. As far as lubricant storage issues are concerned, ensure that transfer equipment (pumps, containers, hoses, filter carts) are dedicated to lubricant types as much as possible, and when cross-use of equipment is unavoidable, proper flushing procedures are followed. Once good lubricant storage and handling practices are in place, virtually the only instances of mixing will come from planned lubricant changes, and with the benefit of foresight, these can be easily and safely planned.
Reference
Noria Corporation. Machinery Lubrication training course.
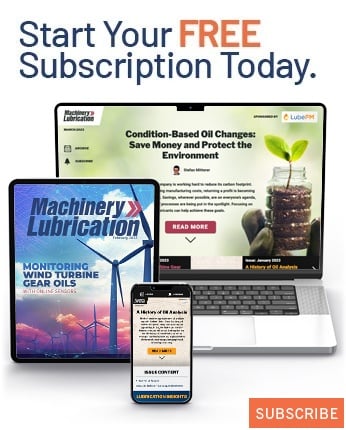