In industrial maintenance, machinery lubrication has always been critical to ensuring the smooth operation and longevity of equipment. Traditionally, lubrication has relied on manual methods and routine schedules, often resulting in inefficiencies and unplanned downtimes. However, with the advent of digital transformation, the landscape of machinery lubrication is undergoing a significant revolution. This transformation is enhancing the efficiency of lubrication processes and redefining the maintenance strategies in industries worldwide.
The Traditional Approach to Machinery Lubrication
Historically, machinery lubrication involved manual application based on predetermined schedules. Technicians would apply lubricants at regular intervals, irrespective of the machinery's actual condition. While this method was straightforward, it was also fraught with challenges. Over-lubrication or under-lubrication were common issues, leading to equipment wear, unplanned downtimes, and increased maintenance costs. Additionally, manual lubrication was labor-intensive and prone to human error.
Enter the Digital Age: IoT and Smart Sensors
The digital transformation in machinery lubrication is primarily driven by the Internet of Things (IoT) and smart sensor technology. These advancements enable real-time monitoring and precise control over lubrication processes.
- Real-Time Monitoring: IoT-enabled sensors are now embedded in machinery to continuously monitor various parameters such as temperature, vibration, and lubrication levels. This real-time data provides valuable insights into the machinery's condition and lubrication needs. For instance, if a machine part starts to overheat or vibrate abnormally, the sensors can detect these changes immediately and trigger alerts for corrective actions.
- Predictive Maintenance: One of the most significant benefits of digital transformation in lubrication is the shift from reactive to predictive maintenance. With data analytics and machine learning algorithms, predicting when a machine will require lubrication is possible. This predictive approach ensures that lubrication is applied precisely when needed, reducing the risk of over-lubrication and preventing equipment failures.
- Automated Lubrication Systems: Automated lubrication systems, integrated with IoT and smart sensors, can dispense the right amount of lubricant at the right time. These systems eliminate the guesswork and manual intervention, ensuring optimal lubrication. Automated systems can also adjust the lubrication based on real-time operating conditions, further enhancing the efficiency and effectiveness of the process.
The Role of Data Analytics
Data analytics plays a crucial role in the digital transformation of machinery lubrication. The vast amount of data IoT sensors collect is analyzed to identify patterns and trends. This analysis helps understand the lubrication needs of different machinery under various operating conditions. Advanced analytics can also provide actionable insights to optimize lubrication schedules and improve overall equipment performance.
- Condition-Based Lubrication: Data-driven insights enable condition-based lubrication, where lubrication is applied based on the actual condition of the machinery rather than fixed schedules. This approach ensures that lubrication is neither too frequent nor too sparse, maintaining the optimal performance of the equipment.
- Enhanced Decision-Making: With comprehensive data analytics, maintenance teams can make informed decisions about lubrication strategies. They can identify potential issues before they escalate, plan maintenance activities more effectively, and allocate resources efficiently. This proactive approach reduces downtime, extends the lifespan of machinery, and lowers maintenance costs.
Benefits of Digital Transformation in Lubrication
The digital transformation in machinery lubrication offers numerous benefits to industries:
- Increased Equipment Lifespan: Digital technologies help reduce wear and tear by ensuring optimal lubrication, thereby extending the lifespan of machinery.
- Reduced Downtime: Predictive maintenance and real-time monitoring minimize unplanned downtimes, enhancing the productivity and efficiency of industrial operations.
- Cost Savings: Automation and data-driven insights reduce the need for manual intervention and prevent costly equipment failures, leading to significant maintenance cost savings.
- Environmental Benefits: Optimal lubrication reduces the wastage of lubricants and minimizes the environmental impact of industrial operations.
The Future of Machinery Lubrication
The digital transformation of machinery lubrication is still in its early stages, but its potential is vast. As technology continues to evolve, we can expect even more sophisticated solutions that further enhance the efficiency and effectiveness of lubrication processes. Integrating artificial intelligence, machine learning, and advanced analytics will drive continuous improvements in predictive maintenance and automated lubrication systems.
In conclusion, the digital transformation in machinery lubrication revolutionizes how industries approach maintenance. By leveraging IoT, smart sensors, and data analytics, companies can ensure optimal lubrication, reduce downtime, and achieve significant cost savings. This transformation not only enhances machinery's performance and longevity but also contributes to more sustainable and efficient industrial operations.
Supplier Spotlight
Pulsarlube USA 1480 Howard St., Elk Grove Village, IL 60007 847-593-5300 | Pulsarlube.com
Pulsarlube provides the most innovative and reliable Automatic single-point lubricator on the market. Backed by years of research and development, Pulsarlube offers a wide range of superior products to meet the needs of our customers. Pulsarlube provides high-quality products and services worldwide through its well-established distribution network.
Royal Purple One Royal Purple Lane, Porter, TX 77365 281-354-8600 | RoyalPurple.com/industrial/
Formulated for demanding industrial operation needs, Royal Purple® high-performance synthetic lubricants improve reliability, extend drain intervals, reduce lubricant consumption, lower operating temperatures, decrease downtime, and reduce maintenance and energy costs- transforming your Total Cost of Ownership into an investment in excellence.
LubePM 1328 E. 43rd Court, Tulsa, OK 74105 800-597-5460 | LubePM.com
As a Lubrication Management System (LMS) engineered by lubrication professionals, LubePM helps an organization create accountability to ensure that every lubrication point is carefully maintained, inspected and measured. Ready to take your facility’s Lubrication Management System to the next level with LubePM? We’re ready to help. Simply request more information or schedule a demo.
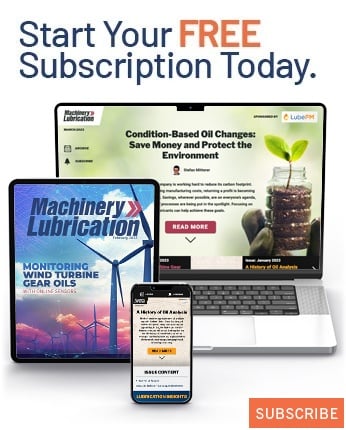