The complex nature of machinery in industrial environments requires sophisticated maintenance practices that continuously evolve to meet new application demands. In addition, new marketing strategies now often include service contracts that go beyond traditional warranty considerations. Consequently, the original equipment manufacturers (OEM) are often directly responsible for equipment availability and reliability.
Figure 1. OEM Equipment Design Trends
Frequently, availability and reliability are based on concepts such as the overall equipment effectiveness, lifecycle cost and the total cost of ownership. The key trends in equipment design considerations and their implications for fluid power technology and condition monitoring (CM) programs are shown in Figure 1. These hardware considerations are only a part of the picture. In practice, equipment operation depends on quality and performance of hydraulic and lubricating oils selected for the application.
In parallel with technological progress in hardware components, these fluids are becoming increasingly specialized and tailored to work under specific operating conditions that often include climatic conditions. Consequently, the past few years have seen a shift toward more complex chemistries in both the structure of base stocks as well as the additive package components.
An aspect often overlooked in the discussion of advancements in hardware design and fluid engineering is the increase in cost invariably associated with the introduction and implementation of new technologies. In turn, higher equipment and fluid costs have put additional pressure on the OEMs and operators to improve maintenance practices to increase the longevity of hardware and extend fluid service life to optimize the total cost of ownership.
In response to these conditions, the OEMs and operators have turned toward more sophisticated CM techniques that increasingly rely on the employment of in-line CM sensors. The main advantage of these devices is that they allow for assessment of fluid condition on an ongoing basis and nearly in real time, in contrast to the conventional practices that rely on analysis of oil samples in off-site laboratories.
Online Sensors
Faster access to data derived from online measurements provides for a more efficient response should a remedial action prove necessary. Although the advantages and even the necessity of using online sensors are recognized, several factors need to be considered prior to their installation in industrial applications. This is because typical industrial environments often involve fluids, temperatures, pressures and flows that could be harmful to the delicate electronic sensor components.
In addition, the sensor response signals need to be collected and transmitted with minimal loss or interference from the surrounding equipment. The challenge then lies in constructing sensors rugged enough to withstand the rigors of the application and cost-effective enough to allow for their broad deployment throughout industrial enterprises or vehicle fleets.
Another question to consider is which system parameters and fluid properties should be monitored to provide a reliable assessment of system performance and fluid condition. For example, in order not to lose the historical connection to data collected previously, care must be taken that sensor signals can be related to the existing norms and standards from which the state of the system was gauged in the past.
As a minimum, the sensor data should include information on wear processes, cross-contamination due to improper fluid addition or leakage, water ingress due to condensation and fluid degradation rate due to hydrolysis or oxidation. For example, particle counts, water content, acid number and viscosity provide information on severity of wear processes, contaminant ingression, condensation and leakage (seal failure) and oil degradation due to aging or oxidation.
With these parameters in hand, more informed decisions can be made on fluid replacement or component maintenance intervals.
This article provides suggestions for sensor installation in hydraulic and lubricating systems with the aim of arriving at the optimal CM and predictive maintenance practices in modern industrial environments.
Measuring Particulate Contaminant Levels
Particulate contamination has often been reported to be one of the primary causes of accelerated wear, malfunction and even failure of sensitive system components. Yet, automatic particle counters are not as widely or routinely employed in industrial applications as one might expect.
This is surprising, because the online particle count is one of the simplest and most informative diagnostic techniques for several reasons. First, the installation and operation of these devices is relatively simple, which makes them amenable for a variety of applications.
Second, the changes in particle counts reflect the rate of ingression of these contaminants from external sources or indicate the onset of accelerated wear of system components. In many cases, particle counts can provide an advanced warning about processes such as gear micropitting or accelerated bearing wear which often manifest themselves by well-defined changes in particle size distribution.
Often, changes in particle size distribution precede detection of macro scale changes, such as those that are detected in vibration analysis. Third, the widespread use of standardized reporting methods has greatly facilitated exchange of information and placed the technique on firmer technical ground.
It has become a standard practice to report particulate contaminant levels in terms of the ISO4406 range code that summarizes cumulative particle counts in the >4 µm(c), >6 µm(c) and >14 µm(c) size ranges. Here, (c) denotes the use of a calibration contaminant (ISO Medium Test Dust) traceable to the National Institute of Standards and Technology and defined by the ISO12103-1, A3 international standard.
Similarly, calibration standards, such as the ISO11943 for online measurements, facilitated the use of online particle counters and made their use a well-accepted industrial practice. An illustration of online particle data collected in the course of an excavator work cycle is shown in Figure 2.
Water in Hydraulic and Lubricating Fluids
Water is one of the most pervasive and most damaging chemical contaminants that threaten the operation and performance of hydraulic and lubricating systems. In addition to its impact on fluid physical properties of the fluid, such as viscosity, it interacts chemically with the base fluid or with the additive package components.
Its adverse impact on system components manifests itself through processes such as hydrogen embrittlement and corrosion, while its presence leads to accelerated fluid and additive package degradation through hydrolysis.
Water remains one of the most cumbersome contaminants to handle, owing to the difficulties associated with quantifying its content by the sensors currently available for continuous, online service in industrial applications.
Part of the difficulty of detecting water in hydraulic and lubricating fluids is that, depending on the nature of the base stock and the additive package components, water might exist in several different states, each of which requires a different detection technique.
At low concentrations, water remains completely dissolved in the host fluid and forms a homogeneous solution. The oil is transparent to the naked eye and the presence of water can be detected only with the aid of suitable analytical techniques.
At higher concentrations, water might exist in the form of droplets dispersed throughout the host fluid and form an emulsion. The fluid appears cloudy or opaque although separation in the bulk phase does not take place. At still higher concentrations, the dispersed droplets coalesce, complete phase separation occurs and water is said to exist in a free state.
Depending on the differences in fluid densities, the water phase might settle to the bottom of the tank or migrate to the top, as with phosphate esters. The difficulty in accounting for all the water present in the fluid lies in the fact that not all instruments or techniques are capable of interacting and therefore accounting for the presence of water in all these three states (dissolved, emulsified and free). Nevertheless, significant progress in this area has been made, particularly in recent years.
Figure 5. Proposed Remote Monitoring and Data Acquisition System
Utilizing Online Water Sensors
The majority of online sensors employed today for continuous monitoring of water content in hydraulic and lubricating systems rely on measurement of capacitance. The capacitor sensors employed in these applications are inexpensive and robust and, therefore, suitable for operation in a variety of fluid types.
Because similar sensors were previously employed for determination of humidity in air, their transplantation to other fluids was relatively simple. These sensors employ a capacitor with a polymer dielectric, sandwiched between metal electrodes and encapsulated by a ceramic substrate for additional durability.
The relative humidity reading is obtained when the water in the surrounding medium reaches equilibrium with water that has migrated into the polymer dielectric which increases the sensor capacitance. The temperature compensation of capacitance readings is accomplished by incorporating a resistance temperature detector (RTD) temperature sensor next to the humidity sensor in the probe body.
A typical water sensor for industrial applications is shown in Figure 3.
Differential Pressure Transducers
The differential pressure (DP) transducers provide valuable information about events that can signal impending or catastrophic component failures or upsets in fluid condition. For example, in stable systems, the rise of the DP across the filter element exhibits a well-defined and nearly exponential progression in time which repeats itself with each new filter element installed, provided the system remains stable.
However, should significant changes in contaminant level or nature take place, the DP curve can prove to be a highly valuable source of information from which the origin of these events can be determined. For example, an earlier onset or a steeper rise of the exponential curve usually indicates a significant increase in contaminant levels.
On the other hand, a change in the shape of the curve (from exponential to linear) may indicate a different loading mechanism (usually caking) associated with a change in contaminant nature or appearance of a new contaminant. An example of a typical DP transducer is shown in Figure 4.
Data Acquisition Controllers
Signal acquisition and data processing represent equally interesting and challenging aspects of CM programs because they facilitate the interpretation of the information provided by the sensors. Frequently, superimposing the data from several sensors reveals trends that might have been missed if the sensor data was interpreted individually.
In addition, combined data presents a comprehensive picture of system performance, component operation and fluid condition which puts the decision-making process on much firmer technical ground. A proposed remote monitoring and data acquisition system is shown in Figure 5.
Summary
Condition-based maintenance programs have become a recognized and established practice in modern industrial world. Their value in improving system performance, extending component and fluid service life and achieving optimized total cost of ownership has been demonstrated and acknowledged by numerous studies and verified by field experience.
With advancements in electronics and software, the range of applications for online sensors continues to increase while their costs continue to decrease. The information on sensor applications and CM practices discussed in this article should be helpful to personnel involved in predictive maintenance programs at all industrial facilities of various branches.
It may also serve as a guideline as to which sensor components might be useful when instituting new programs or augmenting existing ones. Continued innovation in these fields will raise the level of sophistication in these important endeavors and continue to contribute to further reduction in operating and maintenance costs.
About the Author
Dr. John K. Duchowski is the director of technology development for HYDAC Technology in Germany.
About the Company
HYDAC Technology Corporation
2260 City Line Road
Bethlehem, PA 18052-6117
877-GO-HYDAC
www.hydacusa.com
Editor's Note
This article is the first in a series on sensor-based CM techniques. Look for articles focusing on particle counters, water sensors, differential pressure transducers and data acquisition systems in upcoming issues of ML.
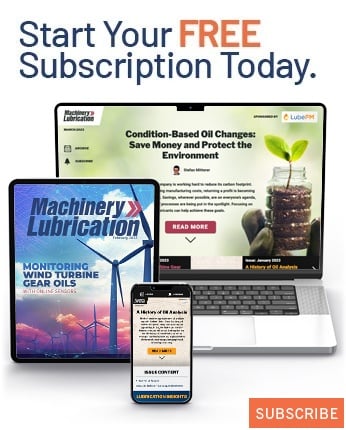