Elemental analysis is an important part of any used oil analysis program, providing concentrations of different wear metals, contaminants and additives. While most oil analysis users are familiar with trending the concentrations of wear metals such as iron, copper and lead, or monitoring common contaminants such as silicon or sodium, elemental spectroscopy is often overlooked in assessing additive health.
When it comes to elemental analysis, labs have two basic choices, Arc-Spark Emission Spectroscopy or Inductively Coupled Plasma (ICP) Spectroscopy. Both methods provide elemental concentrations (usually in parts per million or ppm); the principle difference between the two methods is the preparation and presentation of the sample to the spectrometer. For monitoring additive concentrations, ICP is usually the preferred method because it has a wider dynamic range than Arc-Spark. This allows additive element concentrations in the 1000 to 5000 ppm range, typically found in crankcase and other highly formulated oils, to be accurately measured. For this reason, most lubricant formulations use ICP for quality control during production and packaging of lubricating oils.
![]() |
![]() |
Elemental
analysis works by first vaporizing an oil sample, and then exciting the
molecules present in the sample with a high energy source so that they
are broken up in their constituent atoms. These excited atoms emit light
at different wavelengths corresponding to the type of atomic elements
present. By measuring the amount of light emitted at each discrete wavelength,
the concentrations of each element can be determined. The difference between
an Arc-Spark instrument and an ICP instrument is the high energy excitation
source used. In an Arc-Spark instrument, the oil is vaporized and excited
using a high voltage discharge between an electrode and a rotating carbon
disc. In an ICP instrument, the oil is injected into a high temperature
argon plasma.
|
One of the problems with using elemental spectroscopy for used oil analysis is the particle size bias of this method. For Arc-Spark instruments, only those particles smaller than six to eight microns in size can be sufficiently vaporized to provide reliable concentration data. For ICP instruments, the situation is even worse with only particles in the three to five microns range and smaller being “seen” by the spectrometer. For additive quality control purposes, this size limitation is usually not an issue. With only a few exceptions, additives must be soluble in a lubricant base stock to be effective, although it must be considered when using elemental spectroscopy to evaluate wear problems and certain contaminants.
The main problem with using elemental spectroscopy to trend additive health is that the test is not actually measuring the concentration of the additive itself, but rather the concentration of the constituent atoms of the additive molecule in question. For example, a certain antiwear (AW) hydraulic fluid may contain the additive zinc dialkyldithiophosphate (ZDDP) which is both an antiwear and antioxidant additive. Taking a clean, new sample of this oil and performing ICP analysis will typically yield zinc and phosphorus concentrations in the 200 to 300 ppm range, indicative of the amount of ZDDP present in the oil. When this oil is put into service, the ZDDP will be slowly depleted reducing the oil’s effectiveness in resisting oxidation and preventing wear from occurring. Although depletion results in the loss of ZDDP molecules through chemical reaction, the amount of zinc and phosphorus present as measured by ICP is usually unchanged since atoms cannot be destroyed by simple tribochemical reactions. The result is an oil, which may have 50 percent or more ZDDP depletion, but still shows normal zinc and phosphorus levels of 200 to 300 ppm.
One way around this problem is to use the Stoke’s procedure to separate healthy additive molecules from those that have been depleted. The method relies on the principle that particles and other insoluble materials suspended in a liquid (such as oil) will naturally separate due to gravitational effects. When additives are depleted, they typically form insoluble chemical byproducts, which are held in suspension in the oil. Because these insoluble byproducts are too small to drop out of suspension under normal circumstances, increase the effective gravity to around 35,000 g’s. Place the oil sample in a centrifuge spinning at 20,000 rpm so those insoluble molecules in the oil separate out, such as additive depletion byproducts as well as wear particles and contaminants, from those that remain in the oil such as healthy additives.
To calculate the remaining useful additive level using this method, a new oil sample is dissolved in a solvent such as kerosene and thoroughly mixed. Concentrations of oil in solvent vary depending on the sensitivity of the instrument and the range of elemental concentrations, but are usually between 20 percent and one tenth of one percent. The sample is then transferred to a 100 ml centrifuge tube and centrifuged for five minutes to separate all insoluble material as well as any trace water from the oil sample. The remaining dry, solid-free solution can then be decanted and run as usual on the ICP instrument. The same procedure is carried out on the used oil sample with the centrifuged solution again decanted and run on the same ICP instrument.
Because any insoluble material, including spent additives, is removed during sample preparation, the centrifuged solution from the used oil sample shows only those elements dissolved in the oil and are thus representative of healthy additive molecules. The remaining useful additive level can then be estimated by ratioing the elemental concentrations from the centrifuged solution of both new and used samples as follows:
Percent Remaining Additive Level = ppm used oil / ppm new oil X 100
Using this simple approach, elemental spectroscopy can be used to monitor additive depletion, providing a valuable tool for estimating the remaining useful level of healthy additives left in a lubricating oil.
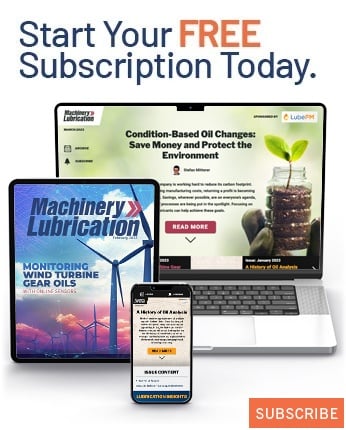