Introduction: 5 Things to Know About the Backbone of Machine Performance
1. The Importance of Tools in Machine Maintenance
- Hand Tools: Wrenches, pliers, and hammers remain staples in every maintenance toolkit, valued for their versatility and ease of use.
- Diagnostic Tools: Vibration analyzers, thermal cameras, and ultrasonic sensors help technicians detect wear and misalignment before they escalate into significant issues.
- Torque Tools: Proper torque is crucial for reliability, especially in bolted joints where improper tightening can lead to failure. Advanced torque tools ensure correct specifications are met.
2. Hardware that Boosts Machine Durability
- Bolts and Fasteners: Often overlooked, fasteners must withstand stress and vibrations. Opting for corrosion-resistant materials can extend the life of your machines.
- Seals and Gaskets: These components prevent fluid leaks and are essential in machinery lubrication. Different materials (rubber, silicone, or metal) can drastically affect longevity and performance under varying temperatures and pressures.
- Bearings: High-performance bearings reduce friction and wear, prolonging machine life. Lubrication plays a significant role here, and integrating systems that ensure constant lubrication will improve operational reliability.
3. The Role of Lubrication Tools
- Grease Guns: Manual and pneumatic grease guns are indispensable for delivering precise amounts of grease to bearings and other moving parts.
- Automatic Lubrication Systems: These systems ensure that machines are lubricated without human intervention, improving consistency and reducing maintenance intervals.
- Oil Analysis Kits: By regularly analyzing oil samples, technicians can spot contamination and degradation early, preventing more extensive machine failures.
4. Emerging Trends in Tools & Hardware for Reliability
- IoT and Smart Tools: The Internet of Things (IoT) has introduced smart tools that offer real-time data collection and monitoring. For example, smart torque wrenches can log applied torque, reducing errors and improving safety records.
- 3D Printing: This technology is beginning to impact the hardware space by enabling on-demand manufacturing of replacement parts and reducing downtime due to supply chain delays.
- Condition Monitoring Systems: Real-time condition monitoring tools integrated with machine hardware allow for predictive maintenance, drastically reducing unexpected breakdowns.
5. The Impact of Proper Tool & Hardware Management on Downtime
- Preventive Maintenance: Regular checks on hardware such as bearings, fasteners, and seals ensure that wear and tear are caught early, minimizing downtime.
- Tool Calibration: Regular calibration is necessary for precision tools like torque wrenches and diagnostic instruments to ensure they provide accurate readings and performance.
Conclusion: Optimizing Tools & Hardware for Maximum Reliability
Supplier Spotlight
Pulsarlube USA 1480 Howard St., Elk Grove Village, IL 60007 847-593-5300 | Pulsarlube.com
Pulsarlube provides the most innovative and reliable Automatic single-point lubricator on the market. Backed by years of research and development, Pulsarlube offers a wide range of superior products to meet the needs of our customers. Pulsarlube provides high-quality products and services worldwide through its well-established distribution network.
Esco Products 2501 Central Pkwy, Suite A-5, Houston, TX 77092 800-966-5514 | EscoPro.com
Esco provides solutions for maintenance and lubrication problems in any industry that uses reciprocating and rotating equipment with oil reservoirs. In addition to our revolutionary Visual Oil Inspection product line of sight glasses, Esco is one of Dow & Dupont’s largest distributors of Dowsil sealants and Molykote high-performance lubricants. As a DesCase partner, we offer their full line of breathers and fluid handling equipment. Contact us today to learn more!
Royal Purple One Royal Purple Lane, Porter, TX 77365 281-354-8600 | RoyalPurple.com/industrial/
Formulated for demanding industrial operation needs, Royal Purple® high-performance synthetic lubricants improve reliability, extend drain intervals, reduce lubricant consumption, lower operating temperatures, decrease downtime, and reduce maintenance and energy costs- transforming your Total Cost of Ownership into an investment in excellence.
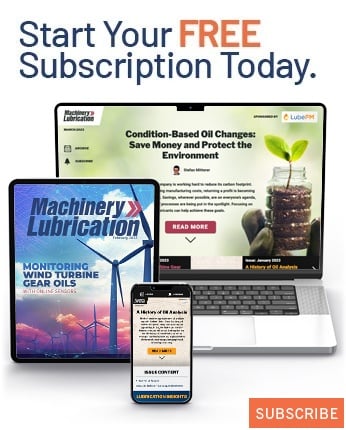