Constant progress is part of life. We may rail against it at times, but we can’t stop it. And, it manifests itself in many different ways.
In engineering, we’ve grown accustomed to machines and their component parts becoming stronger, lighter, cheaper, smaller, more powerful and more efficient.
Nowhere is this more evident than in the field of information technology. In fact, according to Moore’s Law – named after Gordon Moore, co-founder of Intel Corporation – the power of computer chips doubles every 18 months. At the same time, the cost of this extra computing power to the consumer decreases exponentially.
But as the cost of computing power to the consumer falls, the cost for manufacturers to fulfill Moore’s Law heads in the opposite direction. R&D, manufacturing and testing costs have steadily increased with each new generation of chips.
This has led to the definition of Moore’s Second Law, which states that the capital cost of semiconductor fabrication increases exponentially over time. This means progress comes at a cost – somewhere along the supply chain, at least.
The rapid and constant development we’ve seen in the IT sector is hard to match. But like most other areas of mechanical engineering, the hydraulics industry hasn’t been resting on its laurels, either.
Component operating pressures have increased steadily over the past 30 years, and this trend is forecast to continue. Seal and hose design has improved accordingly, as has oil additive and filtration technology. Advances in materials and manufacturing techniques mean that more efficient hydraulic components with higher power densities are available at lower cost.
In short, much progress has been made, most of it good for hydraulic equipment owners. But, it has come at a cost. Higher operating pressures and closer tolerances make the hydraulic machine more susceptible to wear and damage resulting from oil contamination and inadequate lubrication. This means proactive maintenance is essential for optimum reliability and performance of today’s hydraulic equipment.
But just as Moore’s Law is expected to hold true for another generation, so will the pursuit of performance gains by hydraulic equipment manufacturers. The question is: Which way from here?
To answer this question, it seems to me that some hydraulic equipment manufacturers are headed in the wrong direction. They are “dancing with the devil”, so to speak. Hopefully, my use of this metaphor will make sense once I explain.
A colleague who works for a major hydraulic component manufacturer recently told me his company’s original equipment manufacturer (OEM) customers are demanding components that can handle hydraulic system operating temperatures in excess of 110 degrees Celsius. This number is not for margin of safety; it’s for continuous operation.
But heat is the biggest enemy of a hydraulic system. It’s bigger than particle and water contamination these days due to the widespread understanding and adoption of modern filtration technologies.
And so, in my view, a hydraulic system running at 110°C is a hydraulic system from hell – figuratively speaking, of course. And so, to intentionally design such a system is like dancing with the devil. Let’s consider some of the reasons why.
Oil Life
According to Arrhenius’ Law, for every 10°C increase in temperature, the rate of reaction doubles. The chemical reactions we’re concerned with – in so far as hydraulic oil life is concerned – are oxidation (due to the presence of air) and hydrolysis (due to the presence of water). So the hotter the oil, the faster the rate of these reactions – and exponentially so.
By way of illustration, if you pour some cooking oil into a glass, it’ll take days, even weeks, before it darkens in color – a sign of oxidation. But pour the same amount of cooking oil into a frying pan – which gives the oil a large contact area with air – and then heat the heck out of it, and the oil will go black in a very short space of time.
When asked about the issue of oil life, my colleague from the hydraulic component manufacturer admitted that when lab-testing hydraulic components at temperatures of 110°C and above for extended periods, the oil had “turned black as ink and smelt unmentionable.”
Oil Viscosity
As I explained in my last column, the operating viscosity of hydraulic oil is crucial for both adequate lubrication and efficient power transmission.
The higher the maximum expected operating temperature, the wider the temperature operating window becomes. And the wider the temperature operating window, the more difficult it is to maintain oil viscosity within both allowable and optimum limits.
For example, consider a system with a cold-start temperature of 5°C and a maximum operating temperature of 110°C. To maintain viscosity between 800 centistokes at cold start and 25 centistokes at maximum operating temperature, it would require an ISO VG150 oil with a viscosity index of 2291. Just in case these numbers don’t mean much to you, this is not the type of hydraulic oil you can just call in and pick up from your local oil supplier.
Seal and Hose Life
Like everything else, the elastomers used to make hydraulic seals and hoses are improving all of the time. But oil temperatures above 82°C accelerate the degradation of most of these polymers. In fact, according to one seal manufacturer, operating temperatures 10°C above recommended limits can reduce seal life by 80 percent or more.
The constant cycle of heating and cooling – a process known as aging – is more severe when temperature extremes are greater. Aging causes these polymers to lose their elastic properties. This results in leaking seals and hoses.
False Progress
Increasing the temperature at which a hydraulic system is expected to operate does nothing to enhance machine performance. It only compounds a host of reliability issues which cannot be solved with current technologies. So, it’s not progress; it’s regress. This false progress will certainly come at a cost – to the hydraulic equipment owners who operate them.
References
1. According to ISO Viscosity Grade calculator available at: http://www.mehf.com/2.A.4.b.4.htm
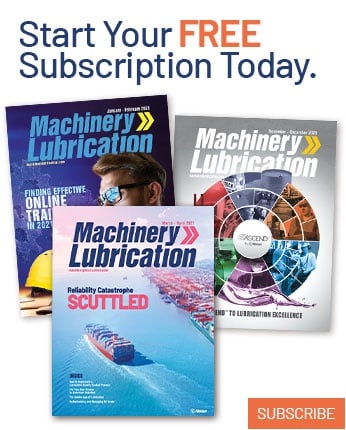