GTI Spindle Technology Inc., one of the world's largest and fastest-growing spindle remanufacturers, is advising its customers who utilize high-frequency grinding spindles to consider air/oil lubrication to help eliminate the negative impact on the environment that other types of lubrication systems may cause. GTI has been offering air/oil lubrication systems since 2004 to customers in various industries.
"Although being environmentally conscious in your manufacturing practices is not a new trend, at GTI, its part of our core business practices. As new systems become available that may assist companies in improving their work environment while also minimizing the negative effects on the environment that air/oil mist lubrication can have, then we have the responsibility to offer this type of air/oil injection lubrication systems to our customers," says GTI president Thomas Hoenig.
Air/oil injection provides advantages over air/oil mist lubrication, including:
· More precise metered amount of oil provided to the lubrication points
· Dramatically decreases oil consumption by 2/3
· Eliminates work environment contamination
· Removes occurrence of venturi becoming clogged/varnished
· Ability to provide lubrication to more points using only one system
One key selling point that GTI stresses to its customers, such as NTN Driveshaft in Columbus, Ohio, in considering the adoption of air/oil lubrication for use on their high-frequency grinding spindles can primarily be contributed to its eliminating harmful contaminates in the work environment. Factors such as having no oil fog in the air, no oil residue on machines or floors, and no oil to be inhaled by workers have provided tremendous benefits to the company and its employees. Another significant benefit concerns reductions in spindle failure rates, as NTN realized a reduction in excess of 60 percent.
About GTI
GTI Spindle Technology, with locations in Manchester, N.H.; Bloomington, Ill.; Romulus, Mich.; and Pontiac, Ill., offers a variety of services including failure analysis and corrective action programs, vibration analysis diagnostics and guaranteed cost savings programs. The company inspects, repairs and remanufactures spindles and other precision rotating assemblies including super-precision high-frequency, motorized, belt and gear driven spindles with emphasis on Japanese and European high-speed machining centers.
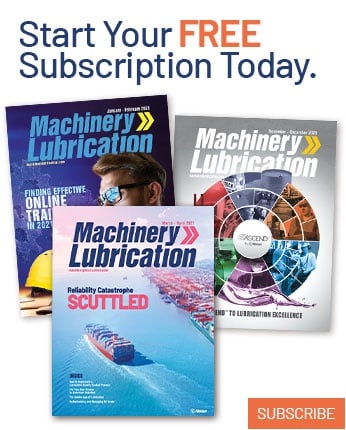