The Kern River Cogeneration Company Omar Generation Facility has been supplying steam for enhanced oil recovery in the Texaco Oil Field north of Bakersfield, California for the last 15 years. Summertime temperatures in this part of the state frequently exceed 100°F (38°C).
The Kern River facility operates four General Electric Frame 7 gas turbines. Three of these turbines have been upgraded from GE frame 7E to DLN 7EA machines, which traditionally run hotter, exacerbating the heat load on the 32-weight turbine oil used for both bearing lubrication and hydraulic control in these turbines. The operating conditions in this part of California continually push the extreme limitations for the mineral-based turbine oil used at Kern River.
The Effects of Scheduled Maintenance
Traditionally, a unit is shutdown nearly every weekend at Kern River for an off-line compressor wash and maintenance. At every shutdown, hydraulic servo valve failures occurred, extending outage times by several hours. This situation was deemed unacceptable by management because the facility is expected to work at 100 percent capacity.
Contamination and oil degradation were the root causes of the servo valve failures, prompting the company to carefully monitor lube condition using oil analysis. Once monitoring began, the oil analysis data revealed that the useful life of the turbine oil had been exceeded, as suspected.
In each case, oil analysis revealed Rotation Pressure Vessel Oxidation Test (RPVOT) values dropped more than half of the new oil, along with elevated AN levels, indicating a significant degree of oil oxidation. In addition, particulate levels were as high as 21/19/16, with signs of varnishing signs in each gas turbine sump.
Careful examination of the failed valves revealed no problems other than being stuck, mostly likely from particle and varnish build-up in critical cylinder-to-bore clearances, caused by excessive oil oxidation. These findings prompted a request to perform a complete oil change, flush and clean on each unit.
The cost of unplanned downtime in California during peak season was more than enough for management to justify the project expenses to make the necessary changes and improvements. Kern River’s maintenance team was given the go ahead.
At this facility, the lubrication program is delegated as a collateral assignment to a facilities operator, Ken Huckeba. He utilized vendors, lubrication engineers and lubrication specialists to formulate a plan of attack. The entire project took less than six months to complete because the plant needed to be fully operational before peak operating season resumed in the summer.
A Cleaner Clean
Properly changing the oil in a gas turbine is often a larger task than it appears to be. There are several factors to consider when planning this type of procedure. For instance, a gas turbine with many hours of service tends to be quite contaminated. Thorough cleaning is a top priority to remove all traces of debris and oil degradation by-products. The first step was to remove the old oil and empty, squeegee and clean all sumps, auxiliary sumps and return lines with lint-free rags.
The clean, empty sump allows for the repair of all instrumentation, coolers and valves that are usually submerged in oil. A splash plate was bolted to the piping under the torque converter dump valve to keep the fluid from stirring particulates off the bottom of the sump when the unit is crank started.
This tip is GE Frame 7-specific, and only time will tell if this works or not; however, during the cleaning process, the sump floor was quite dirty with the exception of the area directly below this dump valve, indicating that a significant degree of agitation had occurred in this area during normal operation.
The coolers were pulled and chemically and mechanically cleaned inside and out. This made a tremendous difference on the coolers’ ability to properly transfer heat load from the oil to the coolant because it takes only a very thin varnish coating to degrade cooler performance by reducing thermal conductivity.
Prior to the oil change, these units were found to have seriously elevated oil system temperatures due to fouled coolers. Varnish typically builds-up on the coolers first, even in a moderately clean system, due to thermal cycling. This is because varnish condenses on the cool surface of the heat exchanger. After the coolers were cleaned, system temperatures dropped on average 15 to 30 degrees.
During the cleaning process, this varnish was extremely hard to remove; in fact, no amount of mechanical pressure washing could remove it. To overcome this problem, cooler pressure test fittings and cleaning stands were custom-made, allowing the coolers to be washed in a caustic bath.
This required careful planning due to environmental considerations and chemical storage requirements. Steam from an operating unit was used in the caustic bath. It took quite a few treatments before the cleaning solutions finally got underneath the varnish and began lifting it off. In addition, all interior tubes were hydroblasted to remove deposits.
Lubrication Selection
One of the key criteria used for selecting the right lube for this application was to ensure that the oil had excellent resistance to oxidation because of the excessive heat loading that this oil would be subjected to over time. Synthetic oils were considered, but were ruled too costly for this application.
While hydrocracked base stock oils were not readily available at the time, Huckeba called for a high quality mineral oil with excellent oxidation resistance. To decide which oil was best for this application, Huckeba obtained oil samples from selected vendors and had the oil’s RPVOT tested to depletion (until the pressure in the RPVOT test vessel dropped by 25 psi).
This sounds redundant, but after speaking with industry experts, it was discovered that some laboratories stop the test early and extrapolate the data instead of carrying out the test all the way to depletion. This showed fascinating results. Some oils with higher new oil RPVOT values were found to undergo a very quick pressure drop in the RPVOT test, indicating incorporation of the oxygen into the oil.
Other oils with much lower quoted RPVOT values were found to have very stable additive packages and maintain a consistently high RPVOT pressure reading with only a slow but constant pressure drop as the oil oxidized through the duration of the test. Huckeba chose the oil that maintained a high pressure through the early stages of the RPVOT test despite having a lower initial RPVOT value based on the stability of the antioxidant additive package.
Huckeba also visited the lube supplier’s blend facility to get a complete understanding of procedures and to address any problems and concerns. One requirement was to make stipulations on the lubricant’s specifications at delivery. Guarantees were agreed upon for items such as initial RPVOT and particle count with penalties for dirty oil and oil that didn’t meet a specified RPVOT value.
This initial RPVOT value is extremely important because it determines the turbine oil’s ability to handle oxidation in the future. Baseline sampling independent of the vendor is also important. Large samples were taken for extensive analysis to firmly establish baselines and were tested by both the oil manufacturer and independently using Kern River’s own program to ensure that all new oil batches met specified limits.
The final step of the oil change procedure was to hire an outside contractor to clean the new oil to super-clean standards a few days after the oil change. This was done to let the new oil pick up any contaminants left in the system prior to cleaning.
This added expense was equal to half the cost of the oil, but was worth it due to the fact that a high proportion of problems, particularly those in servo valve controlled components are caused by particle contamination. After this procedure, the turbine oil reached immaculate standards of fluid cleanliness.
This procedure was performed more than two years ago. Since then, a new grade of polyester filters was installed. The cleanliness levels have leveled out around 18/16/13 and are still lower than required for this company’s goal-based reliability standards for a hydraulic system of this kind.
Side stream filter skids are being manufactured to bring this particulate level down to 14/11 or better and the company is using a portable filtration cart, which uses ion-exchange technology to maintain acid number levels with acceptable limits by removing by-products of oil oxidation.
The goals for the turbine oil change, flush and clean, were met but are ongoing. There has not been a single hydraulic valve failure on any of the four turbines in the past two years and the systems maintain much cooler temperatures.
Although slightly higher than desirable, fluid cleanliness levels are still very low and should improve when the side stream filters are online, while RPVOT and AN levels are constant and close to new oil values. Although a nominally simple procedure of changing the oil was made complicated, Kern River believes it was well worth the effort.
Located in central California, these units were called upon to peak fire during the many Stage 1 alerts the past two summers. Kern River would not have been able to operate as efficiently during those hot summers if the oil had been left unchanged and the coolers and sumps remained unclean, because during the summers months preceding the change, the turbine systems were getting too hot at base load.
The lessons learned from this ongoing process have expanded to include heat recovery steam generator feed-water pumps, units that are also critical for reliable operation, but that surprisingly have no filtration. External filters and coolers are being engineered and will be installed at a later date.
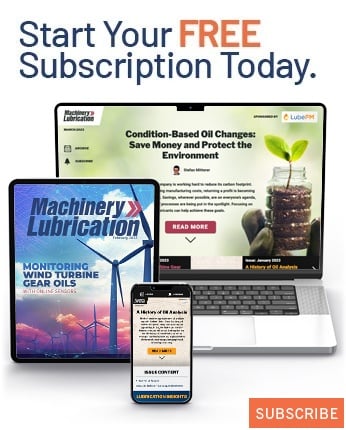