The January-February 2017 issue of Machinery Lubrication detailed how the Seminole Electric Cooperative near Jacksonville, Florida, was able to extend the life of the lubricants used in its electro-hydraulic control (EHC) systems. This follow-up article will explain the unintended consequences of going 30 years without an oil change.
After 30 years, the facility’s phosphate-ester fluid became unmanageable, and a high-velocity chemical flush was completed on the system with a rinse fluid and a new fluid fill. This turned out to be an eye-opening experience, as the fluid became dark soon after the flush.
Some believed this was due to the generation of new debris or problems within the system. Others thought the new oil was cleaning the system. Whatever the reason, the new fluid was quickly getting worse, and when you have 2,500 gallons per unit, it must be treated as an asset rather than a commodity.
New Problems
The problems began shortly after the first chemical flush was completed on the second unit and it was returned to service. The new fluid turned black fast. It was so dark that a flashlight could not be seen through the fluid in a sample bottle. The final filter was changed from a 3-micron element to a 1-micron varnish-removal type element.
The hope was this filter would help clean up the problems occurring after the chemical flush. This proved to be a problem of its own, as the element could not last even one month before the terminal differential pressure was reached. One of the high differential pressure elements was sent for analysis to identify the composition of the debris that was plugging the element. Once this was determined, a plan of action could be developed to correct the issue.
The filter analysis detected five distinct categories of materials. More than 86 percent was derived from the EHC fluid, which was comprised of phosphate esters and their breakdown products (varnish). Another 8.63 percent was reported as metal/metalloid contaminants associated with acid-scavenging media.
An additional 2.11 percent was found to be wear metals or particles consistent with those expected from wear of metallic equipment components, while 1.85 percent was characterized as metal contaminants often associated with foreign lubricant mixing. The final 1.27 percent was classified as halogen contaminants, which can be associated with fluoropolymer breakdown or seawater.
Not all of these materials were thought to be current problems with the new oil after the flush. Of course, even with a high-velocity flush, there will still be some buildup or residual material from a 30-year run that the new fluid will clean and remove.
Of the fluid-derived breakdown products, 58.86 percent was carbon. This most likely was caused by microdieseling, which is a pressure-induced thermal degradation. An air bubble transitions from a low-pressure area to a high-pressure zone and through adiabatic compression is heated to very high temperatures.
Even though not much heat is transferred between the fluid and the bubble, the temperature within the bubble can reach 2,000 degrees F. When this occurs, it forms submicron-sized soot particles, which can cause the oil to darken.
This image shows the changes in oil color when electrostatic filtration was started, stopped and restarted.
System Changes
As with any plant, many things were changed, modified and updated over the years. Unfortunately, the lubrication and design engineers did not communicate. Although certain changes to enhance a system might not affect its operation, they can be very detrimental to the fluid.
Among the concerns with phosphate-ester fluid include a pressure drop within the system, pressure spikes, inadequate residence time in the reservoir for air release, improperly returned fluid to the tank, and the lack of a downcomer or diffuser on the return line. Unfortunately, these problem areas are not easy to locate within a system and usually are difficult to fix.
In this case, the reservoir was well-designed with downcomers, diffusers, baffles and a large enough volume for proper air-release residence time. There were three submerged screw pumps, each with a capacity of 175 gallons per minute (GPM), along with a constant-pressure regulating valve and three relief valves, one per pump. There were no accumulators in the original system, so two pumps were run continuously to meet system spikes and swings.
With 350 GPM from the two pumps, the residence time in the reservoir was just more than seven minutes. The new oil’s air-release time is usually between three to five minutes. After one year, the fluid had an air-release time of 7.4 minutes and was up to 11 minutes before the removal of submicron debris. If there was a spike in the system, the third pump started automatically but did not shut down automatically.
The constant-pressure regulator valve was designed to handle 1,100 GPM. When the valve is not working properly, excess flow and pressure are relieved by the relief valves on each pump. This initially was not much of a problem since the relief valves dumped into a common header that drained into the main return line to the bottom of the tank through a diffuser.
Over time, separate dump lines were placed on the relief valves. One remained in the return header, while the other two were flanged right to the top of the tank. When the constant-pressure regulator valve stuck, there was excessive heat generation at the relief valves and additional aeration from the returning oil to the tank.
Prior to the chemical flush, the constant-pressure regulator valve and three relief valves were sent for rebuild and calibration. They are now calibrated annually as needed. During the flush when the tank was drained, new downcomers with diffusers were added to the two relief valves’ dump lines. Accumulators were also installed approximately one year after the flush, so the plant can now operate on one pump at 175 GPM, thus increasing the residence time for air release in the tank.
The rest of the system consists of 10 stop valves, 10 control valves, a couple miles of piping, numerous orifices and other fluid-restricting valves. The actuators for the stop and control valves were replaced several years ago. Leak-through had not been checked on the old system.
The new system has been measured at approximately 50 GPM bleed-through. This flow reduction can only help to diminish the heat-induced problems within the system that are detrimental to the fluid.
Darkening Fluid
The corrected items still did not solve the issue of the darkening fluid. While the ISO codes were excellent (15/13/10 to 16/13/11), the fluid continued to get darker. However, the fluid’s color was not the actual problem. The facility needed to know how much submicron debris was in its fluid. Submicron debris has been thought to cause blinding or coating of acid-remediation media, which makes it challenging to control acid generation and maintain the proper acid number.
The prior filter testing had revealed the type of debris, 58.86 percent carbon, which in this case was soot. Two methods can be used to collect submicron debris: membrane patch colorimetry (MPC) and gravimetric analysis. These methods utilize a nitro-cellulose patch, which will have a specific volume of fluid passed through it before being dried and weighed.
The MPC method may have a higher patch weight if the system has excessive varnish, since the solvent used can force semi-soluble contaminants to precipitate and be collected on the patch along with the submicron debris. This method primarily uses a color scale to identify the fluid’s condition and does not include patch weight. When soot is in the system, a black patch is already assumed, so while color is important, the weight of the patch will be the more valuable information. Therefore, be sure your lab can weigh the patches.
Electrostatic filtration was not deemed cost-effective
for the old, degraded fluid.
Electrostatic Filtration
Since changing the final filter from a 3- to 1-micron element was impractical, electrostatic filtration was tried. This type of filtration had previously been used with excellent results but was not deemed cost-effective for the old, degraded fluid.
One thing to consider when using electrostatic filtration is the fluid’s water content, as it does not function properly when the water level is more than 500 parts per million (ppm). With phosphate-ester fluids being hydrophilic, they can solubilize up to 4,000 to 4,500 ppm water at operating temperature, which can create problems.
In this case, the system had dry headspace purge air installed many years ago. This utilizes a device that dries the air to a dew point of minus 40 degrees F. The air is then blown into the headspace of the reservoir and exits through the existing vent.
Phase equilibrium allows the water to be pulled out of the fluid into the dry air and then blown out the vent. This has worked very well. Even in the hot, humid summers of Florida, water levels below 500 ppm have been maintained.
Two types of electrostatic filtration are available for lubricants: balanced charge agglomeration (BCA) and the collector type. BCA initially was tried on the second unit. It consists of a pre-filter and a mixing chamber that charges particles and starts the agglomeration process. Larger agglomerated particles are filtered out in a final or post filter. Although this method reduced the patch weight, no color change was noted in the fluid.
Next, the collector type of electrostatic filtration was employed. With the filtration in service, it took a few months for the oil to begin changing colors and for the patch weight to decrease. A problem then occurred with the filtration unit, which was not fixed for a couple months because of a unit shutdown.
Fortunately, during the same shutdown, accumulators were installed on the second unit. This allowed for one-pump operation. Now, not only was the reservoir residence time increased for air release, but the soot generation was also lessened due to adiabatic compression of bubbles within the pump.
When electrostatic filtration was placed back into service on the second unit, the cleanup time to clear oil was greatly reduced. The air-release time also decreased by two minutes. The hope is this was due to the reduction of generated debris rather than the system being cleaned with new oil.
Controlling System Problems
As with most mechanical things, when something goes wrong, it usually is not just one issue but several compounded problems. The quick fix is often just to change the oil, but this case is a perfect example of the oil not being the issue. Instead, it was the system that was causing the trouble. While many of the easy fixes have been made, only time will tell if they are enough to solve the problems that seem to plague EHC systems.
Electrostatic filtration appears to be the best technology for removing submicron debris from the fluid in this system. Although it is always nice to have fluid you can look through, your primary concern should be to reduce and control the problems within the system that create submicron debris, as this can be very detrimental to properly maintaining your oil.
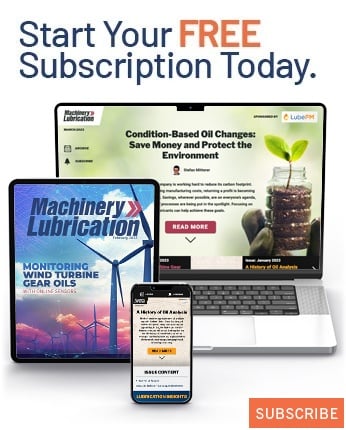