Oil sensors and analyzers are used in automotive and industrial applications to gather or send valuable information. They can range from a simple, float-type oil level indicator to a complex, in-line laser particle counter and everything in between. This article will outline the different types of oil level sensors, demystify how they work and explain the results they return to the user.
Mechanical Sensors
The mechanical sensor is the simplest and most widely used level sensor. The principle behind magnetic, mechanical, cable and other float level sensors involves the opening or closing of a mechanical switch, either through direct contact with the switch or magnetic operation of a reed.
With magnetically actuated float sensors, switching occurs when a permanent magnet sealed inside a float rises or falls to the actuation level. With a mechanically actuated float, switching occurs as a result of the movement of a float against a miniature (micro) switch.
The choice of float material also is influenced by temperature-induced changes in specific gravity and viscosity; such changes directly affect buoyancy.
Don’t use float-style sensors with very high-viscosity (thick) oils, oils that have a tendency to form sludge and varnish, or heavily contaminated oils. Other sensing technologies are better suited for these applications.
A special application of float-type sensors is the determination of interface level in oil-water separation systems. You can use two floats, with each float sized to match the specific gravity of the oil on one hand and the water on the other.
Another special application of a stem-type float switch is the installation of temperature or pressure sensors to create a multi-parameter sensor. Magnetic float switches are popular for simplicity, dependability and low cost.
Pneumatic Sensors
Use pneumatic level sensors where hazardous conditions exist, where there is no electric power or its use is restricted, and in applications involving heavy sludge or slurry. Since the compression of a column of air against a diaphragm is used to actuate a switch, no process liquid contacts the sensor’s moving parts.
These sensors are suitable for use with highly viscous liquids such as grease. This has the additional benefit of being a relatively low-cost technique for point-level monitoring in a lube system.
Ultrasonic Sensors
Use ultrasonic level sensors for non-contact level sensing of highly viscous liquids, as well as bulk solids. The sensors emit high-frequency (20 to 200 kilohertz) acoustic waves that are reflected back to and detected by the emitting transducer.
Turbulence, foam, steam, chemical mists (vapors) and changes in the concentration of the process material also affect the ultrasonic sensor’s response. Turbulence and foam prevent the sound wave from being properly reflected to the sensor.
Steam and chemical mists and vapors distort or absorb the sound wave. Variations in concentration cause changes in the amount of energy in the sound wave that is reflected back to the sensor. Use stilling wells and wave guides to prevent errors caused by these factors.
Proper mounting of the transducer is required to ensure best response to reflected sound. In addition, the tank should be relatively free of obstacles such as weldments, brackets or ladders to minimize false returns and the resulting erroneous response, although most modern systems have sufficiently “intelligent” echo processing to make engineering changes largely unnecessary except where an intrusion blocks the “line of sight” of the transducer to the target.
The requirement for electronic signal processing circuitry can be used to make the ultrasonic sensor an intelligent device. Ultrasonic sensors can be designed to provide point-level control, continuous monitoring or both. Due to the presence of a microprocessor and relatively low power consumption, there also is capability for serial communication to other computing devices, making this a good technique for adjusting calibration and filtering of the sensor signal, remote wireless monitoring or plant network communications.
To summarize, the ultrasonic sensor enjoys wide popularity due to the powerful mix of low price and high functionality.
Conductive Sensors
As most all oils have an insulating property, conductive level sensors aren’t exactly the best choice for an oil level sensor. However, many liquids in industry are conductive, so these sensors are included in this article.
Conductive level sensors are ideal for the point-level detection of a wide range of conductive liquids such as water, and is especially well suited for highly corrosive liquids such as caustic soda, hydrochloric acid, nitric acid, ferric chloride and similar liquids.
For those conductive liquids that are corrosive, the sensor’s electrodes need to be constructed from titanium, Hastelloy B or C, or 316 stainless steel and insulated with spacers, separators or holders of ceramic, polyethylene and Teflon-based materials. Depending on their design, you can use multiple electrodes of differing lengths with one holder.
Since corrosive liquids become more aggressive as temperature and pressure increase, consider these extreme conditions when specifying these sensors.
Conductive level sensors use a low-voltage, current-limited power source applied across separate electrodes. The power supply is matched to the conductivity of the liquid, with higher voltage versions designed to operate in less conductive (higher-resistance) mediums.
The power source frequently incorporates some aspect of control, such as high-low or alternating pump control. A conductive liquid contacting both the longest probe (common) and a shorter probe (return) completes a conductive circuit.
Conductive sensors are extremely safe because they use low voltages and currents. Since the current and voltage used is inherently small, for personal safety reasons, the technique also is capable of being made “intrinsically safe” to meet international standards for hazardous conditions.
Conductive probes have the additional benefit of being solid state devices and are very simple to install and use. In some liquids and applications, maintenance can be an issue. The probe must continue to be conductive. If buildup insulates the probe from the medium, it will stop working properly. A simple inspection of the probe will require an ohmmeter connected across the suspect probe and the ground reference.
Build on Knowledge Base
There are many other techniques and technologies used to monitor sump levels, but the devices covered in this article are going to be the most prevalent in nearly all plants.
I hope this article gives you a better base knowledge of the different types of sensors used. As always, if you would like more information or wish to discuss this subject in greater detail, feel free to contact me.
Sensor Technology Reduces Costs, Downtime
Fluid condition sensors, which can track a variety of fluid condition metrics – including viscosity, conductivity and dielectric constant – provide the continuous monitoring capability required to ensure the uninterrupted operation of equipment. Read an exploratory article on this topic from SenGenuity at www.machinerylubrication.com. Access it by typing “SenGenuity” in the Search box.
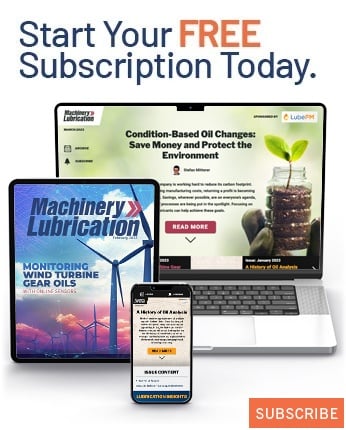