A wide range of fluid degradation issues can affect lube oil systems. One growing concern is the presence of sludge and varnish. This condition can occur in even the most well-maintained machines. Surprisingly, it can also arise when oils are not particularly old or contaminated, as well as in thermally robust synthetic lubricants and hydraulic fluids.
Figure 1. Varnish Formation on Inlet Guide
Vane (IGV) Valve from a Gas Turbine
Sludge and Varnish Defined
The products of lubricant degradation are called sludge and varnish. These products start in the dissolved form and accumulate until the lubricant reaches its capacity, referred to as the saturating point, forcing any excess to convert into insoluble degradation products. In certain instances, deposits form on machine surfaces at the exact location where the oil has degraded. In other cases, the oil degrades in one location but, the insoluble degradation products are carried elsewhere by the moving fluid forming deposits on surfaces.
Figure 2. Varnish Formation on Plain Bearing and
Shaft (Courtesy Cerestar Deutschland)
Over time, some deposits can thermally cure to a tough enamel-like coating. Other types of deposits, generally in cooler zones, remain soft or gummy and may, in some cases, appear clear and grease-like. The following are examples of where sludge and varnish might occur in turbine lube oil and electrohydraulic control systems:
- black crusty deposits on mechanical seals
- gold adherent films on valves
- charcoal-like deposits on babbitt sleeve bearings
- gooey-brown accumulations on oil filters
- black scabby deposits on mechanical seal surfaces and thrust-bearing pads
- carbonaceous residue on mechanical surfaces
The deposits that form on sensitive machine surfaces interfere with the flow of fluid and the machine’s mechanical movements. The deposits can also contribute to wear and corrosion or impair heat transfer by clinging to surfaces. For example, deposits on the spool and bore of a servo control valve can tighten the interference fit.
Other types of sludge and varnish-induced failures include:
- silt lock valve failures
- plugged orifices
- damaged mechanical seals
- plugged discharged ports
- journal-bearing wear (disrupted hydrodynamic film production)
- premature plugging of oil filters
- impaired oil cooler performance
Turbine Systems
In turbine systems, few failure conditions can disrupt operation as quickly and completely as a varnished and seized-up control valve operation. Sludge can gum up flow controls, strainers and critical oil pathways. In recent years, there has been an increasing number of reported cases associated with varnish and sludge formation in turbine-generator applications.
Being proactive about dealing with the problem is important for keeping unexpected downtime to a minimum. We will discuss ways to detect and manage the degradation of oil in this article, but using a system designed to deal with varnish, such as the SVR™ Lubricant Conditioning System can address the problem proactively.
SVR utilizes patented ion-exchange resin technology called ICB™ to remove chemical breakdown products and varnish at a molecular level, maintaining lubricants through full-time, continuous treatment.
Whether you have a treatment solution in place or not, there is a need for incipient advisories that report developing varnish potential. The risks are especially pronounced in high-pressure, servo-controlled hydraulic systems operating in continuous and high-duty service.
Degradation Methods and Analysis
Before discussing the methods for analyzing sludge and varnish in turbine systems, it is helpful to understand the lubricant degradation methods in turbine lube oil and hydraulic systems.
Bulk Oil Oxidation
Oxidation causes degradation of the bulk oil over time. Under mild machine operating conditions and a clean environment, oxidation will occur gradually, generating dissolved degradation products. However, elevated temperatures accelerate the oxidation process — the general rule of thumb is that for every 10°C (18°F) increase in operating temperature, the rate of oxidation doubles (Arrhenius Rate Rule).
Water, metals (such as iron or copper particles) and aeration also act as catalysts to speed up this process. As oxidation by-products accumulate beyond their saturation point, they convert into insoluble degradation products, which are attracted to mechanical surfaces, resulting in sludge and varnish in the system.
Thermal and Compressive Base Oil Degradation
Thermal degradation occurs due to adiabatic compression from entrained bubbles or when oil comes in contact with a hot surface. When the machine surface temperature is greater than 200°C (400°F), depending on oil type, thermal degradation can start.
Such heat can come from gas combustion, steam and highly loaded frictional surfaces. Often the aeration occurs due to tank agitation, plunging oil returns or surface lapping. Suction line leaks, pump seal leaks and venturi zones (vena contracta regions) can also introduce air into circulating fluids.
Regardless of the means of entrainment, the forcing function that leads to sludge and varnish is in place. The failure will now proceed along one of two pathways; both involve adiabatic compression in either the load zone of a lubrication system or the pressured zone of a hydraulic control system.
Adiabatic compression occurs when air bubbles travel from low pressure to high pressure. The air bubble compresses rapidly (implosion), resulting in the entrapment and concentration of heat and an extreme rise in the oil’s temperature. The temperatures reached (typically greater than 1,000°F) are often more than sufficient to thermally degrade the oil.
Electrostatic Discharge
Studies have been conducted on the effects of static discharge in hydraulic systems since the 1970s. Static discharge is a form of localized thermal degradation, which has been discussed previously. Recently, attention has been directed to fluid electrification and static discharge as a prominent contributor to sludge and varnish formation in turbine systems.
Electrostatic charge generation occurs in fluid systems as a result of internal molecular friction and electric potential between the fluid and machine surfaces (particularly where no boundary films develop, such as the interstices of an oil filter). Many factors contribute to the magnitude of the static charge within the oil; however, grounding of the machine itself has little impact on mitigating charge propagation.
This is due to the oil being nonconductive, which effectively self-insulates the charged fluid zones from grounded surfaces. Once these charges build up in the working fluid zones, including reservoirs, the subsequent static discharging, similar to lightning strikes through the fluid, may cause localized thermal-oxidative oil degradation.
Figure 3. Acid Number (AN) for Turbine Oil Exposed to Static Charges
after Zero, Six and Nine Months in Storage
According to research conducted by Dr. Sasaki, spark discharges can reach temperatures as high as 20,000°C. Additionally, he has found that although the initial failure is localized, the chemical degradation process is autocatalytic. In one study, a turbine oil sample was exposed to spark discharges. Acid number (AN) was measured on the oil samples just after initial exposure and again after six and nine months of oil storage.
The results of this test are shown in Figure 3. AN was measured immediately after the tests and were the same, regardless of the number of sparks exposed to the turbine oil, suggesting that the bulk oil degradation had not yet started. However, there was a significant change in AN after being stored, indicating that the oil oxidation process had advanced past the induction period, even when stored in the dark at room temperature.
Stages of Failure | Conditions of the Fluid to be Tested | Corresponding Analytical Method |
Stage One (precursor stage) — Root causes that propel the fluid into the next stage |
Measurable oxidation root causes: 1. Particle contamination 2. Wear debris 3. Water contamination 4. Antioxidant additive depletion |
1. Various laboratory particle counting methods (optical, pore blockage and microscopic) 2. Elemental analysis, ferrography, ferrous density analysis 3. Various laboratory methods, including Karl Fischer and FTIR 4. Methods include FTIR, RPVOT, RULER and HPDSC |
Stage Two (transitory stage) — The beginning of base oil degradation and increasing risk of varnishing formation |
The presence of soluble oxidation products to form: 1. Carboxylic acids, formic acids, etc. 2. High-density resins, polymers, etc. 3. Chromophoric compounds (color bodies) |
1. FTIR (1,730 cm-1), AN 2. Coagulated oxide insolubles 3. Spectrophotometry, patch colorimetry |
Stage Three (attack stage) — More advanced oxidation phase where significant risk of varnish, corrosion and impaired lubrication is present |
The presence of both soluble and insoluble oxidation products to form: 1. Metal carboxylate soaps and sludge 2. Suspended oxide insolubles 3. Rising oil viscosity |
1. Analysis of sludge (bottom sediment, organic filter sediment, etc.) by elemental analysis, FTIR (1,730 cm-1), GC/MS 2. Ultracentrifuge, patch test, patch colorimetry 3. Viscometry |
Table 1. Methods for Analyzing
Oxidation-induced Sludge and Varnish |
Analysis Techniques for Monitoring Sludge and Varnish
Analytical techniques for measuring sludge and varnish vary depending on the failure mechanism. These methods fall into three categories, according to the stage of contaminant or degradation product targeted. The first stage is a precursor condition. Specifically, it relates to the contaminants that give lubricants a propensity to form oxides and other oil breakdown products.
Stage two is a transitory stage. Typically, it consists of soluble oxides and other dissolved impurities that might later synthesize to form insolubles. The condition that aids the transition from stage two (oxide soluble) to stage three (oxide insoluble) may be cold oil temperature or simply a supersaturated state (a concentration of oxides in excess of the varnish saturation point).
Stages of Failure | Conditions of the Fluid to be Tested | Corresponding Analytical Method |
Stage One (precursor stage) — Root causes that propel the fluid into the next stage |
Measurable root causes: 1. Impaired air-release properties 2. Cross-contamination (mixed lubricants) 3. Contamination with polar impurities (dirt, water, oxides, etc.) |
1. Air release tests (ASTM D3427) 2. FTIR, elemental analysis, etc. 3. Various standard lab tests for such impurities |
Stage Two (transitory stage) — The beginning of base oil degradation and increasing risk of varnishing formation |
The presence of soluble thermal degradation products: 1. Nitric oxides 2. Chromophoric compounds (color bodies) 3. Localized thermal failure conditions |
1. Thick-cell (500 µm) FTIR for nitration (1,639 cm-1) 2. Spectrophotometry, patch colorimetry 3. Pattern testing (combining above tests with RPVOT, AN, viscosity, etc.) to differentiate from bulk oil degradation |
Stage Three (attack stage) — More advanced degradation phase where a significant risk of varnish is present |
The presence of both soluble and insoluble thermal degradation products to form: 1. Suspended high molecular-weight nitric oxides and similar resinous insoluble compounds 2. Sludge and deposits |
1. Ultracentrifuge, patch test colorimetry, coagulated insolubles 2. Analysis of sludge (bottom sediment, organic filter sediment, etc.) by elemental analysis, FTIR, GC/MS |
Table 2. Methods for Analyzing Thermal
Degradation-induced Sludge and Varnish |
Stage three is an attack stage. While conditions in stages one and two may not damage the machine, stage three contaminants are surface-active, potentially causing deposits, corrosion or mechanical wear. Stages one and two are more proactive, meaning that analytical methods detect aberrant conditions before damage or harm to the machine occurs. Stage three is a predictive maintenance stage where an incipient or impending machine failure is already in progress.
Stages of Failure | Conditions of the Fluid to be Tested | Corresponding Analytical Method |
Stage One (precursor stage) — Root causes that propel the fluid into the next stage |
Root causes: 1. Exceedingly dry oil 2. Exceedingly clean oil 3. Unoxidized oil 4. Drop in oil conductivity |
1. Karl Fischer, dew point meters 2. Particle counters (various), total insolubles 3. AN, RPVOT, FTIR (1,730 cm-1) 4. Conductivity meters, dielectric breakdown testers, dielectric constant meters, etc. |
Stage Two (transitory stage) — The beginning of base oil degradation and increasing risk of varnishing formation |
The presence of soluble thermal degradation products: 1. Chromophoric compounds (color bodies) 2. Localized thermal failure conditions |
1. Spectrophotometry, patch colorimetry 2. Pattern testing (combining above tests with RPVOT, AN, viscosity, etc.) to differentiate from bulk oil degradation* |
Stage Three (attack stage) — More advanced degradation phase where a significant risk of varnish is present |
The presence of soluble and insoluble thermal degradation products: 1. Suspended high molecular-weight similar resinous insoluble compounds 2. Sludge and deposits 3. Gas evolution |
1. Coagulated total insolubles 2. Analysis of sludge (bottom sediment, filter sediment, etc.) by elemental analysis, FTIR (1,730 cm-1), GC/MS 3. Flash point, gas chromatography for acetylene and other gases* |
*Note: Analytical methods for clearly isolating oil degradation in conditions to electrification and static discharge have not been fully developed.
The methods listed here are general in nature and may aid in the differentiation. Table 3. Methods for Analyzing Static Discharge-induced Sludge and Varnish |
Oxidation is a well-known oil degradation mechanism and is relatively simple to monitor with traditional oil analysis methods compared to other failure mechanisms. Thermal degradation, although less understood, is also common and can be analyzed with traditional oil analysis. The effects of static discharge are still relatively new to the oil analysis field. It is more difficult to analyze (isolate as the root cause) with traditional oil analysis techniques.
The degradation stages and analytical scheme for oxidation, thermal and compressive base oil degradation and static discharge conditions are presented in Tables 1 through 3.
Numerous analytical tests have been identified in Tables 1 through 3. It is of interest to discuss a couple of these tests and how their results can be used to distinguish the various failure mechanisms.
Membrane Patch Colorimetry (MPC) - Varnish Potential (ASTM D7843-21)
As oxidation occurs, degradation materials are generated and accumulate in the oil. MPC varnish potential testing is an adapted patch test using non-polar solvent and a spectrophotometer to quantify the insoluble color bodies that are captured on the patch. Because the MPC result will be higher the longer the sample sits in the sample container, the ASTM procedure requires a reset period whereby the sample is heated to 140°F (60°C) for 24hrs and aged for 68-74 hours. In this manner, all laboratories can test MPC at the same moment in time. The resulting patch's varnish potential is expressed as ΔE. The recommended in-service guideline is to maintain MPC ΔE <20.
Fourier Transform Infrared Spectroscopy
As oxidation increases, common reaction by-products are carbon-oxygen double bonds, also called the carbonyl group. Carbonyl peaks on FTIR spectra in the 1,740 cm-1 region (Figure 4), easily identifying oxidation. As oxidation increases, the absorbance peaks will increase in this region. Additionally, phenol inhibitors used as antioxidants in the oil show peaks around 3,650. Changes in this peak are also noteworthy.
Figure 4. FTIR Spectrum Showing
Oxidation Peak around 1,740 cm-1 Range
Because thermal degradation can occur without significant amounts of oxygen, different degradation by-products are often observed. Therefore, the 1,740 cm-1 peak is less likely to be significant. Instead, the by-products of thermal base oil degradation show up in the 1,600 to 1,640 cm-1 region — also known as the nitration peak due to the nitrogenous by-products, which is more pronounced using a thick-cell (500 µm path length) spectrometer.
Acid Number (ASTM D974 or D664)
Acid Number (AN), previously referred to as Total Acid Number (TAN), increases over time due to the oxidation process. In large turbine systems, AN change should be very gradual, with increases as low as 0.3 to 0.4 above the new oil baseline often sufficient to condemn an oil.
Rotating Pressure Vessel Oxidation Test (ASTM D2272)
RPVOT measures an oil’s resistance to oxidation. This information indicates the oil’s remaining oxidative useful life (RUL) and is calculated by dividing the in-service sample result, expressed in minutes, by the new oil result. RPVOT values are influenced by the type and quantity of antioxidants present in the oil and the oxidative robustness of the base oil. Cautionary and critical limits for turbine oils are usually at 60 percent and 40 percent RUL, respectively.
Linear Sweep Voltammetry (ASTM D6971)
Measures the aromatic amine and hindered phenol antioxidants in new or in-service type turbine oils. Values are expressed as a percent of new oil baselines. Warning levels are expressed at <50% of the primary antioxidant, which is normally the amine, but in some oil brands it can also be the phenol. The critical value is <25% of the primary antioxidant.
Viscosity (ASTM D445)
During oxidation, cleaved oil molecules recombine to form higher molecular weight species. An increase in absolute viscosity can indicate when oxidation becomes advanced. In some cases, oil can be thermally cracked during degradation, where the oil molecules are severed into smaller molecules. As a result, a decrease in viscosity can be detected.
Flash Point (ASTM D92)
Flash point may be used to identify thermal degradation if oil molecules have been thermally cracked. As the percentage of lower molecular-weight oil fractions increases due to thermal cracking, the flash point will drop accordingly.
Conclusion
A number of degradation methods have been discussed in this article. In order to differentiate between the failure mechanisms and assess varnish potential severity, turbine owners should consider an ensemble of tests to monitor the oxidative or chemical degradation of turbine oils, such as:
- MPC
- FTIR
- ACID Number
- RPVOT
- LSV
- Viscosity
- Flash Point
References:
- Livingstone, G., Clarus Technologies and Thompson, B., Analysts, Inc. “New Varnish Test Improves Predictive Maintenance Program.” Practicing Oil Analysis magazine, July 2005.
- Fitch, J., Noria Corporation. “Demystifying Sludge and Varnish.” Machinery Lubrication magazine, January 2002.
- Fitch, J., Noria Corporation. “Using Oil Analysis to Control Varnish and Sludge.” Practicing Oil Analysis magazine, May 1999.
- Noria Corporation. “The Lowdown on Oil Breakdown.” Practicing Oil Analysis magazine, May 2003.
- ASTM D4378-03. Standard Practice for In-Service Monitoring of Mineral Turbine Oils for Steam and Gas Turbines, Annual Book of ASTM Standards 2005, West Conshohocken, Penn.: American Society for Testing and Materials, 2005.
- Yamamoto and Hirano. “Electrical Behavior of Phosphate Esters.” Wear, volume 50, 1978, p. 349–355.
- “Electrokinetic Wear.” BFPR Journal, Fluid Power Research Center, Stillwater, Okla. 1988, vol. 21, p. 137–145.
- Sasaki, A. et al. “Generation of Static Electricity During Oil Filtration.” Lubrication Engineering magazine, September 1999, p. 14-21.
- Duchowski, J. et al. “Overcoming Electrostatic Discharge in Hydraulic and Lubricating Applications By Incorporating A Novel Filter Media.” NCFP I05-19.1, NFPA Technical Paper Series, Presented at International Fluid Power Exposition, March 2005.
- Sasaki, A., et al. “Free Radicals and Oil Auto-Oxidation Due to Spark Discharges of Static Electricity.” Lubrication Engineering, May 1998, p. 24-27.
- White, L. “Snap Crackle Pop,” Hilliard Corporation, Elmira, New York (n.d.).
- Fitch, J. “Hydrocarbon Analysis,” Chapter 24, Fuels and Lubricants Handbook: Technology, Properties, Performance, and Testing, George E. Totten, West Conshohocken, Penn.: ASTM International, 2003.
- “Fourier Transform Infrared Spectroscopy.” Practicing Oil Analysis magazine, March 2002.
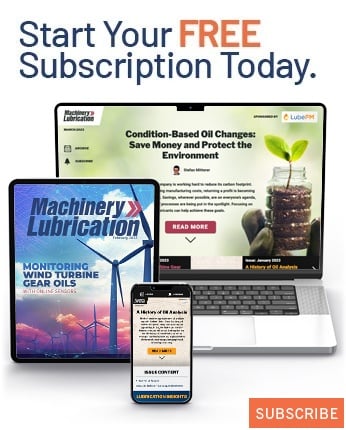