Central Azucarera de La Carlota Inc. (CACI) is a 93-year-old sugar cane processing company based in Negros Occidental in the Philippines. Recently, the company has been under pressure to improve efficiency due to the impending removal of protective import tariffs, rendering its products non-competitive against cheaper imports.
CACI identified the recurring problem of water seeping into the turbine oil as a major cost that could be reduced. During operations, its previous best solution was to replace the oil over and over again. As a result, CACI quickly became one of the largest consumers of oil in the country.
Water and Oil Don't Mix
In any amount, water in oil is never favorable. In turbine oil, it destroys bearings and ultimately stalls or trips the system and can cause a plantwide shutdown.
In this case, the presence of water was visually detected due to the oil's milky appearance. The turbine did not have any water-removal mechanism. CACI has a centrifuge, but it is not calibrated properly and, based on oil color alone, does not perform as expected.
The company decided to install an offline filtration system that can remove particles, water and varnish at the same time. It also started using oil analysis differently. Instead of just checking if the oil is still suitable for further use, it checks machine condition and contamination closely. In effect, the processor has shifted from interval-based to condition-based maintenance.
Initially, CACI considered reviving its centrifuge; however, its remote location and the skill required to set the centrifuge up properly proved to be unjustifiable. It also considered extending drain intervals using synthetic oil, but that was quickly discouraged due to cost.
Tackling the Turbines
Turbines are one of the largest consumers of the maintenance budget due to their considerable oil consumption. They also are critical to operations since they power machines. As a consultant to this project, the Center for Reliability Excellence (CRE) chose to tackle the reliability of turbines first because the savings generated would be significant and because turbines had the lowest reliability rating among equipment.
Initially, there was budget constraint. It is the first time that the Negros Occidental plant is addressing contamination, and it didn't recognize the impact of contamination in machine reliability. Also, plant personnel would turn off the filtration unit, reasoning that the oil was not milky in color. That greatly compromised the contamination control measures. The intent was there, but understanding was insufficient. Further training was scheduled. All total, it took two crop years before CACI decided to buy in.
With the initial hurdle of lack of awareness crossed, CRE opted to provide CACI with an "oil recycling" program. This was easier to justify as CACI management would see immediate cash savings from reduced oil purchases, which was a sensitive issue given the upward spiral of prices at that time. CRE documented the oil parameters and educated CACI on how to read them. After trending oil analysis data, the plant appreciated the impact of filtration in terms of oil life.
The crucial point came when CACI had to suspend the recycling of the oil due to unavailability of the filtration unit; the oil turned milky in a matter of days. The plant realized it could not run the turbine without the filtration unit and thus decided to acquire a dedicated unit for the application.
Technical seminars from Noria and some filtration vendors raised the awareness on how clean oil increases machine reliability and how to achieve and measure clean oil. The seminars and vendor support helped CRE install the right filter at the right locations and carry out proper oil sampling.
Impressive Results
CACI used to replace more than 2,200 liters of oil every six months. Today, the oil remains in good health, fit for at least another crop year. The cane processor also managed to extend the mean time between failure of its Babbitt bearings from replacing three each year to replacing none following the intervention. That equates to higher productivity. The company is saving close to 21 man-days that previously were spent each crop year repairing and replacing damaged components.
Also, the company used to encounter periodic short tripping incidents due to low oil pressure, attributed to the presence of water corrupting oil pump clearances and oil film strength. These incidents led to a production downtime worth more than 500 tons of lost cane production. With the filtration unit, it hasn't experienced such an incident throughout the crop year.
Being able to keep the oil clean and dry helped shift the company from reacting when water is present to a proactive water-elimination program.
CRE measured the frequency of lubricant top-up and recorded any lubrication-related stoppages. It also monitored the replacement of parts during the same period. Through regular oil analysis, it monitored the machine condition, oil condition and contamination. CRE came up with the following data: From the offline filtration, CACI was able to save $7,000 in lubricant consumption, $10,000 in bearing replacements and $11,000 in downtime costs.
On top of the offline filter and its related costs, the real costs to implement the change involved the time it took for management buy-in/awareness and commitment of the parties involved.
About the Author
Juan Bautista L. Lee II is a preventive maintenance consultant for the Center for Reliability Excellence, a Noria franchise partner located in the Philippines. He is certified as a Machine Lubrication Technician Level I and a Machine Lubricant Analyst Level I through the International Council for Machinery Lubrication and as a Certified Maintenance & Reliability Professional through the Society of Maintenance & Reliability Professionals. To contact Juan, e-mail juanblee2@yahoo.ca.
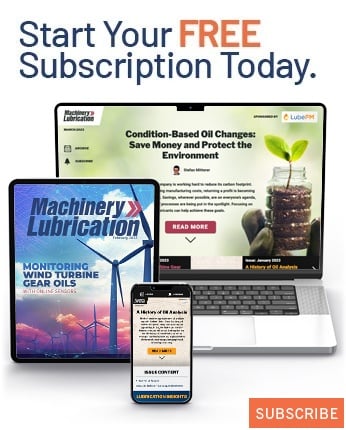