The problem of leaking connectors has been around for as long as hydraulics themselves. It is beyond annoying. It wastes oil. It poses a safety hazard. It can compromise machine reliability. And, rectification consumes the finite resources of the maintenance department. It’s a big problem.
According to hydraulic hose manufacturer Gates, it is estimated that 370 million liters of oil leak from hydraulic equipment every year. That is a staggering statistic – even more so when you consider that as little as one liter of oil can pollute up to one million liters of water.
Sealing technologies have advanced considerably over the past 30 years, but so too have hydraulic system operating pressures and response times. In other words, seal technology has improved, but the stresses they must endure also have increased. As a result, the battle has not been won.
But far from waving the white flag, there is much that can be done to ensure the best possible chance of victory in the war against leaking connections.
Engineer Them Out
If a hydraulic system doesn’t have connectors, they can’t leak. Sure, a system must have some connectors, but their number can be significantly reduced through the intelligent use of manifolds, cartridge valves and stack valves, known collectively as integrated hydraulic circuits, or IHCs (figures 1 and 2).
While the application of this technology normally falls within the realm of the machine designer, if your plant has older machines with line-mounted valves and lots of (leaking) connections, then replacing these line-mounted valves with one or more IHCs will simplify the plumbing and greatly reduce the number of potential leakage points.
Figure 1. Manifold Assembly
Use Reliable Connectors
Tapered-thread connectors such as NPT and BSPT are the least reliable type of connector for high-pressure hydraulic systems because the thread itself provides a leak path. The threads are deformed when tightened and, as a result, any subsequent loosening or tightening of the connection increases the potential for leaks.
Connectors which incorporate an elastomeric seal such as UN-O-ring, BSPP, ORFS and SAE four-bolt flange offer far superior seal reliability.
So for leak-free reliability, replace pipe-thread connectors with a type that incorporates an elastomeric seal, if possible.
That said, the world’s most commonly used hydraulic connection, the JIC 37-degree flare, relies on a metal-to-metal seal. And it means that a permanent, leak-free joint is not always achieved, particularly in the case of tube-end connections. But leaking flare joints can be eliminated by installing a conical washer between the JIC nose and flare.
One type of flare seal, manufactured by Flaretite, consists of a stainless steel stamping, with concentric ribs that contain pre-applied sealant. When tightened, the ribs crush between the two faces of the joint, eliminating any misalignment and surface imperfections. The combination of the crush on the ribs and the sealant ensures that a leak-free joint is achieved.
Torque Them Correctly
A common cause of leaks from 37-degree flare joints and compression-type tube fittings is incorrect torque. In the case of flare joints, insufficient torque results in inadequate seat contact, while excessive torque can result in damage to the tube and connector through cold working. In the case of compression joints, incorrect torque can result in too much or too little “crush” on the ferrule. For optimum sealing reliability, consult the connector manufacturer’s torque recommendations and then apply them as directed.
Figure 2. Vertical Valve Stack
Keep the Machine Cool
Having outlined the benefits of hydraulic connectors that incoroperating temperatures above 85 degrees Celsius result in an exponential reduction in service life for most seal compounds. And, a single over-temperature event of sufficient magnitude can damage all of the seals in a hydraulic system, resulting in numerous leaks.
Short-Circuit Vibration
Vibration can stress hydraulic plumbing, cause fatigue and affect connector torque. If vibration is apparent, the root cause must be addressed. This may involve the installation of hoses and/or rubber mounting blocks to eliminate vibration “bridges” between the hydraulic power unit, tank and valves. Plus, always ensure that all conductors are adequately supported.
Measure to Manage
Do you know how much hydraulic oil each of your machines consumes each year? The only way you can know this for sure – particularly if you have more than one hydraulic machine under your supervision – is if you measure and record all top-offs.
In my experience, most hydraulic equipment users don’t do this. But when clients have done so at my urging, they are often shocked at how much oil a particular machine actually loses over a year.
Yes, I know that it’s one more thing to do, but it’s almost impossible to control anything that you don’t measure. And as the late management guru Peter Drucker once said, “What gets measured gets managed.”
Build Your Arsenal
Hydraulic connection leaks have long been considered an inherent and undesirable characteristic of hydraulic machines. While it is true that the war is not yet won, hydraulic equipment users need to be aware of all the available weapons with which they have to fight. When you consider the true cost of oil leaks – which includes make-up fluid, cleanup, disposal, possible contaminant ingress and safety issues – surrender is not an option.
Battle on.
Read more about how to stop hydraulic leakage:
The Real Cost of Fluid Power Leaks
Selecting Hydraulic Connectors for Leak-free Hydraulic Plumbing
Hydraulic System Leakage - The Destructive Drip
Hydraulic Plumbing Leaks - Causes and Remedies
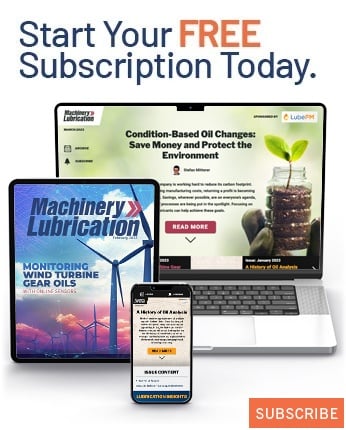