Red. It’s the first thing that you notice. A reddish-brown, clay-toned hue colors the landscape at Alcoa’s alumina refinery complex in Point Comfort, Texas.
The surreal tinting comes courtesy of bauxite, the raw material from which alumina is extracted and refined. Dug out of the freighter ships docked in the adjacent harbor, the material is conveyed through the plant grounds along transport belts and deposited in hill-sized piles until it is ready to be dispatched to process areas.
“Bauxite leaves its mark on our work environment,” remarks Derrick “Gillie” Hall, the engineering, maintenance and powerhouse manager at this site, which is located 125 miles southwest of Houston on the Gulf Coast. “It’s just the nature of the business.”
Senior staff reliability engineer Brenda Graham takes it a step further.
“We are processing dirt,” she says, emphasizing that final word. “We take bauxite, which is from the ground, and crush it up. The final product, alumina, is a very fine powder. It’s hard and abrasive. So maintaining assets, just from a longevity standpoint, is difficult and challenging.”
Crushed bauxite. Alumina powder. Humidity. Add to that caustic steam from chemical processes, accessory process precipitant and residual salts from the Gulf of Mexico.
“Alumina plants, by the nature of the business, given all of the conditions of the process, are very hard on equipment,” says plant manager Allen Ness.
You would think that achieving reliability and lubrication excellence in an environment such as this would be about as likely as safely putting a man on Mars.
Well, as referenced earlier, welcome to life on the red planet.
“People in this business that do maintenance well are the ones that are successful in producing alumina,” says Ness. “If you don’t get maintenance right, it will come down around you and you can’t keep up.”
You will continue in a reactive mode.
This Alcoa facility has worked hard to shift from reactive to proactive. Over the past five years, it has pursued lubrication excellence as part of an overall predictive maintenance strategy. In-depth projects related to lubricant storage and dispensing, oil sampling and analysis, and training and certification have helped position it as a leader among the corporation’s nine global alumina refineries.
Grounded
Prior to 2005, when members of the maintenance organization saw red, it wasn’t just the bauxite; it also was the emergency lights flashing in their heads. Vibration analysis and infrared thermography – tools beneficial to predict and prevent failures – were available and utilized for years. However, the inherent industry challenges matched with a traditional maintenance strategy and old-school lubrication practices created a firefighting habit that was tough to break.
“This plant has really come a long way in my seven years here as far as reliability is concerned, particularly with predictive maintenance,” says Hall. “I can go back to the days when we struggled to even do vibration work because we couldn’t collect the data. We didn’t have the discipline to keep up with data collection and analysis. We would pull the guys off of routes to go fight fires. That was the focus, not on PdM. I am happy to say that we have come extremely far.”
The cleanliness, organization and impressive nature of the lubrication storage building at the Alcoa site in Point Comfort have caused at least one visitor to refer to it as “The Lube Temple”.
From a lubrication perspective, the team has evolved from the days when:
- Oil was primarily stored and dispensed outside, where it was exposed to the elements.
- Undetected varnish and sludge in bearing lubricants had a tendency to cause failures in critical equipment such as turbine generators.
- Lubrication training wasn’t formal, and practices (good and bad) were collected and dispersed through tribal knowledge.
- Lubrication wasn’t seen as an important or respectable position.
- Point Comfort needed to fully commit personnel resources to its predictive maintenance efforts; and,
- Lubrication excellence needed to be a cornerstone of PdM and Rx.
For that last point, Hall says that maintenance workers who focused on lubrication were given the somewhat-denigratory moniker of “oiler” or “greaser”. Not surprisingly, this wasn’t a highly sought-after position within the organization.
You will find a dedicated pump and dispensing system for each lubricant in the storage building.
“When a lube guy retired, it was, ‘Who wants to do lubrication?’ Nobody would raise a hand,” says PdM technician Fred Balboa, a 33-year veteran at the plant. “The lowest guy on the totem pole was given a bucket and told to go after it. We did that for years.”
We Have Liftoff
Groundbreaking change began to occur after site maintenance leaders explored work taking place on foreign soil.
In April 2005, Chris Tindell led a group of five reliability and engineering leaders who attended Noria Corporation’s Reliable Plant conference in San Antonio.
“Listening to the technical papers and the case studies (from companies such as DuPont, Eastman Chemical, Rio Tinto and Clopay), it was really a culture shock. We started to see what was truly possible,” says Tindell, a reliability technician. “We came back and said, we really need to do some of these things.”
And in the spring of 2006, Hall took benchmarking tours of Cargill plants.
“‘Gillie’ is very passionate about reliability, predictive maintenance, proactive maintenance issues,” says Graham. “I think that Cargill trip stoked his fire. Seeing Cargill’s reliability culture got him going.”
The Point Comfort site began implementing Reliability Excellence (Rx), an improvement game plan created in 2003 by Life Cycle Engineering and the Ron Moore Group, and being utilized by Cargill and several Alcoa facilities.
There’s a place for everything and everything is in its place, including filter carts.
Audits, done internally and in conjunction with Life Cycle Engineering and Noria, created the baseline from which program growth would be measured. Through such audits, it was determined that:
- Point Comfort needed to fully commit personnel resources to its predictive maintenance efforts; and,
- Lubrication excellence needed to be a cornerstone of PdM and Rx.
For the first point, the site earmarked a crew of PdM specialists and classified them as a subset of the overall maintenance workforce. No longer would PdM be just a portion of their job, which in the past allowed them to be diverted toward any number of tasks.
Engineering, maintenance and powerhouse manager Derrick Hall goes over reports with senior staff reliability engineer Brenda Graham.
“Before, we were lucky if we were able to run routes once a month, sometimes every six months,” says vibration technician/millwright Eliseo Guevara. “Predictive maintenance is our focus now 100 percent of the time. That makes a difference. It makes you feel like the company is more committed to this.”
Adds Graham: “Any time there is a ‘fire’, they are going to grab whoever they can, but we want to make sure that we have people focused on their task.”
Today, 10 PdM technicians are devoted to lubrication, three each are devoted to vibration analysis and to motor current analysis, and two each are devoted to infrared thermography and to ultrasonic thickness testing.
“One advantage of this is just the attention to detail,” says electrical engineer Ike Anyikam. “When you have this type of focus for people, not much gets past them.”
Such focus was particularly important for lubrication. The audit process showed that only 60 percent of plant equipment was using the correct lubricant. Plenty of honest mistakes were being made.
Oil samples await testing on a cart outside of the oil analysis office. The office is located inside the lubrication storage building.
“We opened up a reservoir and there was this shiny, yellow sheen to the top of the oil,” says Tindell. “The auditor said, ‘Hey, is there an extreme-pressure additive in here? You have a brass worm gear in here.’ Sure enough, the EP was actually attacking the worm gear. We thought, ‘It’s a gearbox. Let’s put an EP in here.’ But, it’s not always the right call.”
Correct, effective lubrication was central in Hall’s overarching maintenance vision of “we do the things that matter the most.” It became clear to all: Lubrication matters.
“I am very passionate about lubrication. I have said in many forums that lubrication is the foundation of any maintenance program,” he says. “If you don’t get that right, then forget about doing vibration, forget about doing motor condition monitoring, forget about doing infrared, forget about doing all of those nice and fancy things. You have to get lubrication right. That’s how the wheels turn. If you stop lubricating something, it will just grind to a halt. This subject is in my heart and soul.”
Predictive maintenance technician Fred Balboa examines some debris with a microscope in the oil analysis office.
Spacious Station
The heart and soul of the Point Comfort site’s lubrication effort is its lube storage, dispensing and analysis building. This 2,400-square-foot (40 feet by 60 feet), cinder-block structure was designed in 2007, developed throughout 2008 and debuted in January 2009. Its ultra-clean, highly organized state accentuates fluid conditioning, climate protection and contamination control. It has led some to remark that it’s part NASA, part Taj Mahal.
“One of our visitors dubbed it ‘The Lube Temple’,” says Balboa, who oversees this building and its processes.
It makes quite an impression.
“We had plant managers from other Alcoa sites in Point Comfort for a week,” says Graham. “We told them we were going to see our lubrication area. It was toward the end of the last day they were here. It was just another stop. They were tired and talking about where they were going to eat that night. They came in here and their jaws dropped. They didn’t think a lube room could look like this.”
It’s so clean inside this building because it’s not that way outside of it.
Oil barrels are no longer stored outside in satellite locations around the complex nor are they placed in an antiquated storage shed.
“In the old building, there was dirt everywhere,” says Graham. “The oil wasn’t necessarily first-in, first-out. You grabbed the first thing you found. Somebody from stores would come in and pick it up. It wasn’t anyone associated with lubrication. When we removed some of this stuff, some drums were a few years old.”
Today, oil barrels are received in the new lube building’s specially protected dock. For each barrel, Balboa samples and personally analyzes the oil to ensure it is of the right quality and specification. The fluid is then transferred to a spare barrel and a filter cart is attached for 16 hours. The oil is resampled afterward to vouch that it meets the required specifications and ISO cleanliness code. Subsequently, the oil goes into a first-in, first-out inventory of barrels or is transferred to a storage and dispensing tote.
Each of the 12 totes in the room’s tower system has a dedicated pump and hose system to deter cross-contamination.
“The oil is all filtered and ready to go,” says Tindell. “Oil only leaves this area in a sealed and reusable (S&R) container or in a barrel. We want barrels coming out with filter carts. The carts are color-coordinated to match the viscosities and additive packages. If a barrel went out for a new gearbox, it goes out with a filter cart. We filter it into the gearbox or we send out an empty barrel with a filter cart, remove the oil from the gearbox and filter it back in while we are doing work. That is our standard.”
S&R containers (also color-coded) are equipped with quick-connects that plug directly into the equipment for clean transferral of fluid. In between topoffs, they are stored in a cabinet (along with grease guns, grease tubes and cleaning supplies) located inside a building close to the point of use.
“With these practices, the oil is never exposed to the atmosphere,” says Balboa.
Inside the lube room, cleanliness practices are not confined to Balboa. Anyone entering the area must don booties over his or her work shoes to avoid tracking in dirt. And, if you check out a filter cart, you better return it in showroom condition.
“Sometimes a lube tech will try to sneak it back in without cleaning it,” says Balboa. “The next time, I’ll watch him and make sure it’s returned the right way. It has to be wiped down ... wheels and all.”
Returned S&R containers go through a special washing machine that removes dirt on the exterior and residual carbons on the interior.
Members of the lubrication team at the Alcoa alumina refinery in Point Comfort include (from left to right): Joseph Justis, George Orzabel, Chris Tindell, Pat Garrett, Charlie Holtz, Fred Balboa, Kenneth Elee, Justin Burke and Brian Baros.
Taking Samples
As touched on in the previous section, the other main deliverable of the lubrication area is oil analysis. Lube technicians regularly draw oil samples from pumps, gearboxes and other key pieces of equipment. Identification data is written in marker on the cap of each sterile glass sample bottle. Filled bottles are delivered to a cart outside the lube room’s smallish analysis office, where Balboa and Graham perform a battery of tests. Samples requiring specialized attention are shipped to an outside lab. Balboa forwards the lab results to maintenance leaders and the techs.
Analysis helps to identify trends (increased levels of dirt, metals, water, etc.) and anomalies before they can generate mechanical stress, degradation and failure.
“When we see a bit of metal, we think, ‘What could be happening here?’” says Graham. “We are spending some focus time troubleshooting those pieces of equipment because they are so critical and expensive. Oil analysis puts us ahead of the game.”
The maintenance group also stays ahead by sampling and analyzing oil during the commissioning of equipment.
“We are getting in the practice of taking baseline samples,” says Tindell. “We went to commission a boiler feed pump, pulled an oil sample before starting it up and picked up ferrous metal. This is a brand-new, multi-stage, $100,000 pump. We found iron and copper. We sent that off to our external lab, and it confirmed our findings. We opened the pump up and found that the slinger ring had fallen out of its groove during transit. It was cocked and rubbing on the internal housing. We wouldn’t have found that if we hadn’t taken the sample.”
From Red to Well-Read
Lubrication, like pumps, may not appear to be complex, but there are a lot of moving parts under the surface.
“You would think that it is so simple – we used to – but there is so much involved,” says Hall. “A little thing like lubrication could make the difference between torturing your equipment or not.”
While not rocket science, lubrication and oil analysis are highly involved, technical and dynamic subjects. Success comes not with a “low man on the totem pole” approach, but instead when folks with “the right stuff” are given the right opportunities. That’s why maintenance leadership at Alcoa’s Point Comfort facility is a firm believer in training and professional certification.
“Knowledge is king. Knowledge is power,” says Hall. “As a manager, I believe in training ... a lot. I don’t believe in asking someone to do something that they are not fully trained to do.”
The site takes full advantage of free educational sessions from its oil supplier, free Webinars from a host of industry resources, and hundreds of thousands of dollars’ worth of technical training and classes through its involvement with a local industrial consortium.
“The consortium gets money from the State of Texas; it’s like $2.9 million,” says Tindell. “We can get special classes together, and then the industry and its partners determine who wants to send how many people to each one. Some of the Noria lubrication classes that we are bringing on site are part of this. We don’t even have to drive anywhere. The state paid for it. You just have to fill out the paperwork and involve the training department to help organize all of that. It has been fantastic.”
Plant workers come away with skills and much more.
“I was at an infrared thermography class last week,” says Anyikam. “After receiving this training, I have a new sense of pride and understanding and knowledge of this equipment. When you have ownership and pride in what you are doing, it’s not just coming to work and getting a paycheck. It goes deeper than that.”
Maybe that’s why Pat Garrett, a lube tech in the calcination department, proudly states, “I told the company to sign me up for everything.”
Mastery of subject matter can lead to certification. Most everyone involved with vibration analysis and infrared thermography on the predictive maintenance team holds a professional designation. Through August, five employees (Graham, Tindell, Carmel Camacho, Hector Venecia and Wayne Pilliner) held at least one certification through the International Council for Machinery Lubrication (for program details, visit www.lubecouncil.org).
Those numbers, especially for ICML certification, will undoubtedly increase this fall and into 2011. Noria will supply extensive lubrication training to lube techs and maintenance coordinators. Attendees will take ICML’s Machine Lubrication Technician Level I exam at the completion of the course. This is all part of Graham’s goal to eventually get all of the techs certified as a MLT Level I.
“I’m prepping them for that test,” she says. “It’s a difficult course. It’s a difficult exam. I don’t want to scare anybody, but I want them to be prepared. I give them questions whenever I can to educate them in advance. That way, they are aware of the level of expertise that they need to attain.”
Whether the students pass the exam or not, the process is worthwhile.
“You may not pass a certification exam. These tests are tough. But you always learn from it,” says Tindell, who along with Pilliner also is a Certified Maintenance & Reliability Professional through the Society for Maintenance & Reliability Professionals (www.smrp.org). “Ideally, we all would like to pass, but that doesn’t always happen. No matter what class you go to, you still will gain information. You will come away with something that you can apply.”
What’s Your Destination?
Lubrication excellence is possible in even the most unforgiving of environments. Alcoa’s alumina refinery is southern Texas proves that out.
Getting there isn’t exactly easy. (Some will tell you a trip to Mars is a better proposition.) There will be challenges. There will be mountains to climb. Whether they are made of bauxite or not, the prize lies on the other side in better-performing equipment, higher yields, less stress and increased profits.
“Lubrication – it’s a matter of discipline,” says plant manager Ness. “How well you do the fundamentals is how well you perform. We are getting better and better at the fundamentals, and that is important as we go forward.”
Alcoa: Defined and Refined
Company: Alcoa is the world’s leading producer of primary aluminum, fabricated aluminum and alumina. It employs approximately 59,000 people in 31 countries. The company had 2009 sales exceeding $18.7 billion, placing it 127th on the 2010 Fortune 500 list. It also holds a spot on Fortune’s World’s Most Admired Companies list.
Plant: Alcoa Point Comfort Operations, located in Point Comfort, Texas (125 miles southwest of Houston on the Gulf Coast). The site opened in 1948, and today features six production units. It currently runs 24/7/365 with two main shifts – 7 a.m. to 7 p.m. and 7 p.m. to 7 a.m.
Size: Approximately 3,000 acres.
Plant employment: The Point Comfort site employs around 550 workers, including nearly 180 in plant maintenance roles. The maintenance staff includes approximately 100 crafts personnel/millwrights, 50 electrical workers and 30 in supervisory roles. Hourly workers are represented by United Steelworkers union Local 4370.
Products: Since 1959, the site has produced alumina, the compound from which aluminum is made, and ships it to Alcoa’s global network of smelters. The plant has the capacity to produce 6,300 tons of alumina per day.
Lubrication Excellence? It’s All in the Alcoa Family
Alcoa has nine alumina refineries around the world, and all are competing for corporate attention, resources and funding. So when a refinery like Point Comfort, Texas, has something good going, it should probably hold on tight to the template, right? Not so, says plant leaders.
“We share information with all of the Alcoa locations,” says reliability technician Chris Tindell. “Even though we consider ourselves somewhat of a competitor with the other refineries, they are all part of the Alcoa family. We share best practices with the family.”
Even those best practices for lubrication excellence?
Information is supplied through various means, including case studies, conference calls and benchmarking tours.
How This Alcoa Refinery Measures Lubrication Success
How do you measure the success of a program such as lubrication excellence? Alcoa’s alumina refinery in Point Comfort, Texas, does that through three specific financial measures.
Says senior staff reliability engineer Brenda Graham: “One is the cost of bearings, because that is something that lubrication definitely affects. Another is the cost of lubricants; we wanted to get rid of some of the expensive lubricants, plus we aren’t dumping oil like we used to. The other is the cost of rotating equipment.
“I think last year, we saved more than $800,000 overall, and this year, through August, we have saved more than $500,000. We have to justify the program, so, yeah, these savings are important.”
Engineering technician Chris Tindell offers additional perspective.
“Many of our projects have financial targets, and then we measure to those targets,” he says. “There are certain metrics that we put into place once we agree that this is a program that we want to pursue. Then, what are the financial implications?
And, how are we going to measure that? Once we agree on the parameters, we are measured against that. Brenda, being the SPA (single point accountable) for lubrication, is very much aware of that. There are targets that need to be met.”
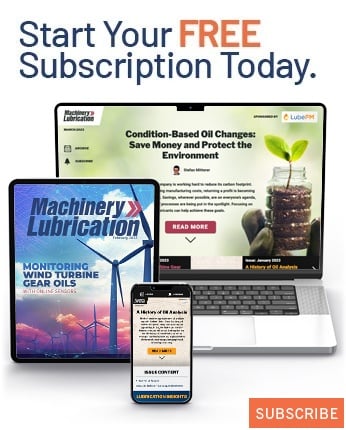