To begin a discussion of preventive maintenance of any machine or component, one should first define preventive maintenance. A suitable definition is this: maintenance that can be performed economically to prevent equipment breakdowns before they occur, shifting the greater portion of maintenance work to a planned basis.
Emphasis is placed upon the word economically, as costs for elaborate and frequent preventive maintenance functions may exceed any savings resulting from the effort. Equipment relubrication is a preventive maintenance function.
In many applications, applying lubricant is most effective when it is dispensed in small quantities at short time intervals. Many operations and types of machinery do not permit this optimum approach to lubrication. Consequently, components are lubricated at intervals dictated by machine operations, available manpower and machine availability. For these reasons, centralized lubrication systems are often installed on existing machinery or on new machinery as it is manufactured.
Purpose of Centralized Lubrication Systems
The basic purpose of a central system is to provide a controlled and reliable means to lubricate multiple bearing surfaces from a central location. There are many types of systems available but all should accomplish the same results: delivery of a controlled amount of lubricant to the bearing’s frictional surfaces. Two broad categories include:
1. Positive displacement systems using metering pistons and
2. Flow proportioning systems using restrictive orifices.
However, all types of systems have three components in common:
1. Pumping station - delivers lubricant to the system at the proper flow and pressure. It may include flow and pressure controls, timers, filters, pressure gauges and over-pressure protection devices.
2. Lubricant distribution systems - deliver lubricant from the pumping station to the metering valves and from metering valves to the lubrication point.
3. Metering valves and fittings - provide controlled deliveries of lubricant to specific lubrication points by either a specifically sized piston discharge or by a specifically sized flow restrictive orifice.
These components are common to all systems whether they are positive displacement, parallel, series, multiline or combination, oil flow proportioning, single-line resistive or aerosol.
Once a proper lubricant is selected for machinery lubrication and the system is properly designed and installed, the natural tendency is to assume that the proper lubricant is applied at the proper time, in the proper place, and in the proper quantity. This is a false assumption; the central lube system must be serviced regularly to operate at peak efficiency.
In the development of a preventive maintenance program relating to any centralized lubrication systems, the major system components must be reviewed.
System Components
1. Energy and pressure generating components
a. Electric pumps
b. Pneumatic pumps
c. Hydraulic pumps
d. Mechanical pumps
e. Manually operated pumps
2. Control components
a. Timers
b. Reversing valves
c. Pressure regulators
d. Signals (lights or warning devices)
3. Distribution network
a. Primary header piping
b. Secondary piping (header to metering device)
c. Final piping (metering device to lube point)
d. Valves, etc.
4. Metering devices
5. Pressure sensing devices
Most centralized lubrication systems are designed with an audible or visual check mechanism incorporated into the system. These devices are also susceptible to failure and must be checked periodically. A low-level warning device on the lubricant reservoir can be beneficial to the system.
The plant personnel responsible for system inspections should be thoroughly trained and familiar with the sequence of operation. Most major system manufacturers and suppliers will train plant personnel on the selected system. The training should include operations, adjustments and maintenance of the system.
The following are the 10 most common ways a centralized lubrication system can fail to deliver the lubricant at the proper time, in the proper place, and in the proper quantity.
1. Plugged or collapsed lines
2. Broken lines
3. Empty lubricant reservoirs
4. Dirty lubricant
5. Pump failure
6. Injector bypass (worn out injectors)
7. Dirty air
8. Low air
9. Power failure
10. Improper adjustments to injectors
At the risk of repetition, be sure to remember the definition of preventive maintenance; that is, what can be done economically to prevent equipment breakdowns before they occur, and to put the greater portion of maintenance work on a planned basis. With this definition in mind, preventive maintenance (PM) should begin with the power source.
Preventive Maintenance
Simple manual operation of the system will determine if the power resource is operating efficiently. In the case of pneumatic or hydraulic operations, a pressure gauge on the power source will confirm operating pressure.
The next phase of the system PM inspection is to check the level of lubricant in the supply reservoir. This check should include a visual examination of the lubricant for contamination in cases where the lubricant is open to the atmosphere during transfer and handling. If the system uses filters, strainers or screens, they should be checked periodically for contamination build-up or blockage, and cleaned.
In the control area of the system, the timer should be checked to assure that the predetermined time settings have not been altered. All electrical controls and terminals should be visually checked for cleanliness and tight connections. Electrical components should be contained inside a panel that can be closed and latched to provide protection from atmospheric condition and to protect plant personnel from system malfunctions. During manual operations of the system, check system pressure and compare to previously determined normal operating pressures.
Checking any lubricating system at the pump/reservoir/control panel location is a necessity, but does not assure that the lubricant is being delivered to the lubrication point. It means only that the heart of the system is in good operating condition.
The next step is to check the distribution system. Ruptured, plugged or kinked piping and tubing can make some portions of the system inoperative while other portions are operating efficiently. This condition can lead the control systems and warning devices to indicate satisfactory performance through the system, when in reality, some machinery points are not being lubricated.
The best way to assure that all lube points are being properly serviced is to visually check each header, secondary lube line, and lube line from the metering device to the lube point. This is, in many cases, a time consuming and difficult task, and consequently is not performed. As a result of skipping this step of the PM check, a malfunction in the header and distribution lines is discovered only when the machinery fails.
Finally, the system is not fully operational unless each metering device is individually checked to assure proper operation. Most metering devices have a visual indicator for this purpose. Those devices that do not have a visual indicator can be checked only by loosening the distribution line from the metering device, operating the system and visually checking for operation of the valve. This is a time consuming and often overlooked portion of the PM check, but is also an important aspect.
Establishing Cycles
Even though all of the activities described are important to system reliability, remember that the economy of preventive system maintenance is the key. To maintain low-cost economics, use common sense when devising PM activities. Because we can’t overlook any of the components, cost control is a function of the frequencies established to perform the required inspection.
Preventive maintenance frequencies are variable, and are determined by operating conditions, complexity of the system, the critical nature of the machinery involved and the accessibility of the equipment as related to production requirements.
Basic system operational checks and lubricant supply checks should be made on a daily basis where possible. Maintenance or production personnel should manually activate the system and check the operation of all lights and/or warning devices on the control panel and pumping station. At the same time, lubricant reservoirs should be checked for proper level and lubricant condition. This process is not time consuming; it takes only five to ten minutes to complete. If operations personnel perform the PM inspection, they should submit a written report of any deficiencies to the maintenance department.
Even though PM checks on distribution networks and individual metering devices are more time consuming, they should be done on a weekly basis if possible, or on a monthly basis at an absolute minimum. Primary and secondary piping on many systems can be easily checked by visual observation of metering device indicators. If all of the indicators on each block of metering devices are operational, the primary and secondary piping is operational. All indicator pins should disappear and reappear on the same cycle. If they do not, there is a malfunction in the system that requires attention.
The final distribution network from the metering devices can be checked only by visual observation of each line from the metering device to the point of lubrication.
Constructing the Format
While reviewing the important criteria for preventive maintenance of centralized lubrication systems, a typical PM checklist can be constructed (Figure 1).
Lubrication Systems Preventive MaintenanceDaily Requirements 1. Manually activate systems and observe cycle completion, warning devices and system operating pressures. Should develop ____ psi. 2. Visually check level of lubricant in reservoir and record ____. Note the brand in use. 3. Check condition of lubricant visually. 4. Check settings on time clock. The system should activate every ____ minutes. 5. Check control cabinet for cleanliness and damage. Make sure the doors are closed and latched. 6. Fill the air line lubricator on pneumatic supply line (pneumatic pumps only) using ____ lubricant. Weekly or Monthly Requirements 1. Check and clean filters, strainers or screens as required. 2. Check piping and hoses on primary and secondary distribution system for broken lines, leaks and blockage or kinks. 3. Visually check metering devices for proper operation. 4. Check distribution lines between metering devices and lubrication points for leaks or damage. Quarterly or Annual Requirements 1. Clean interior of electrical panels and controls. 2. Check for loose electrical connections. 3. Check the pressure gauges and calibrate as needed. 4. Check the operation of warning and safety devices. |
Figure 1 - Lubrication Systems Preventive Maintenance Checklist
|
In addition to development and implementation of preventive maintenance procedures for central lube systems, plant personnel should be trained on the basics of the system. The system manufacturer or the lubricant supplier should be able to conduct training sessions on the system. Reliance upon a lube system to handle lubrication makes it one of the most important machines in the manufacturing plant.
The return on investment from a lubricant purchase is realized only when the product is applied properly and at the right frequency, regardless of whether it is a high priced, high-performance type or a low-cost commodity type product. Centralized lubrication systems play an important role in gaining return on investment, but only if they are maintained to function as designed - supplying the correct lubricant in the right amount to the lubrication point at the proper frequency.
The author is president of KE-LUBE, Inc., specializing in design, installation and maintenance of lubricant delivery and fluid condition control systems. This article originally appeared in an ASLE publication (1984) (American Society of Lubrication Engineers).
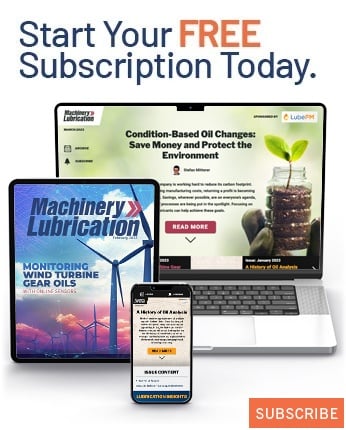