Filtration has two primary objectives. The first objective is “protective”. This refers to creating a barrier to protect particle-sensitive machine components from the invasion of contaminants capable of causing sudden-death machine failure. Machines that have high mission criticality from the standpoint of safety, lost production and/or repair cost are good candidates for protective filtration. Such filters are located just upstream of sensitive components. Many components don’t require wear in order to fail, but they can experience critical loss of performance due to motion impediment and/or flow blockage caused by the intrusion of particles of a particular size and composition. Servo-controlled electro-hydraulic valves are examples of such components that benefit from protective filtration.
The second objective of oil filtration is to mitigate the slow and progressive wear from abrasion, surface fatigue and other particle-induced wear modes. Here is the goal to extend the life expectancy of the machine through the strategy known as proactive maintenance. Many machines release wear metal little by little over time, like tread wearing from the surface on tires. These machines have only so much wear metal to liberate, after which a repair/rebuild is required. Aggressive proactive maintenance tactics using enhanced filtration and ingression control often can extend machine life by two to tenfold.
Changing Landscape
While there have clearly been technological enhancements in the field of oil filtration, what’s driving change mostly are user- and application-specific demands needed to reliably achieve one or both of the above filtration objectives at the lowest possible cost. This is amplified by an increasingly competitive filter supplier environment. Some examples of user- and application-specific demands that have increased in importance in recent years include the following:
Purposeful Filtration – Just having a filter is no longer good enough. Now the filter or filters have to achieve a well-defined objective of attaining quantifiable cleanliness goals. These target cleanliness levels are typically measured and monitored routinely.
User-Engineered Filtration – OEMs and users often have sharply different objectives when it comes to machine reliability and contamination control. Too often, users are forced to take matters into their own hands by adding a filter where there was none. In other cases, users are changing the location and/or enhancing the performance of the filter. Sadly, in many cases, OEMs are far less sophisticated than end-users when it comes to filter selection and the deployment of contaminant-exclusion methods/products.
New Application Requirements – Changing lubricant formulations are putting new demands on filters. One example is the widespread use of highly pure base oils (API base oil groups II & III), which has contributed to electrostatic-discharge problems with filters, causing localized thermal damage from electrical arcing. New filters are now manufactured to solve these problems. These fluids also have intensified varnish-related problems in fluids and machines. Other filtration systems have been designed to remove soft insolubles from oil and help remove deposits from internal machine surfaces. User demand for portable and off-line filters has brought on a wide range of instrumentation and performance features in these products that were non-existent just a few years ago. The list goes on.
Ancillary Filtration – Contamination control is no longer just about a single machine-mounted filtration device. It also includes filters to remove particles and moisture from incoming air to a machine’s headspace (breathers and instrument air purge systems). Quality filters are now needed on transfer equipment, including storage tank pumps, drum pumps, lube-dispensing rack pumps, etc. Of course, high-flow filters also are found on flushing and oil reclamation equipment.
The Non-Particle Filter – Contaminants include particles and many other foreign suspensions, as well. These include air, water, sludge/varnish, bacteria, soot and acids. Suppliers have devised filters and separators to remove these contaminants. They include dry-air sparging, dialysis dehydrators, vacuum dehydrators, centrifugal separators, charged-particle separators, degassifiers, compressed-cellulose filters, etc.
The Best Filter of All
Undeniably, the best filter of all is the invisible filter. This is the filter that doesn’t have to be purchased, doesn’t have to be installed, doesn’t have to be changed and doesn’t have to be monitored. This is the filter that gets the oil clean simply by a change in human conduct and behavior. It’s the countless little actions by people who work with lubricants and machinery that prevent oil from becoming dirty in the first place. These are the things that humans do to expose oil to contamination (knowingly or unknowingly).
The invisible filter is the conspicuous awareness that cleanliness is virtuous toward achieving machine reliability and that every critical machine has an assigned cleanliness target and is monitored religiously.
Awareness and measurement bring about human behavioral change. Be cleanliness wise and cleanliness conscious.
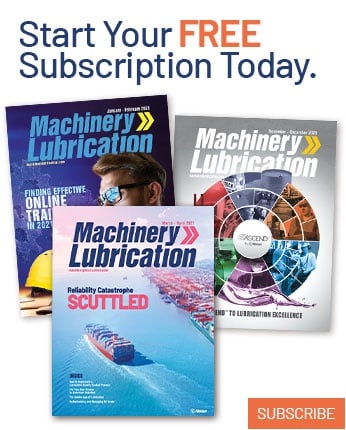