Far too many times, I see plants facing the same challenges over and over. They start at the wrong part of developing a lubrication program. They start by either changing lubricant suppliers, changing greasing intervals and/or changing products, and then hope to see successes and immediate returns on their investments from these emotion-driven changes.
Lubrication excellence is a full-circle game that must be played to its capacity to ensure present and future successes, meaning we must start with determining the right products, address storage and handling flaws, and then work our way to the machines to carry out the actual lubrication task.
Lubrication excellence is not just about lubricating; it is about everything that must go into lubricating properly. This article will discuss some of the main reasons why lubrication programs fail. Namely, it comes down to storage, handling and decontamination.
Figure 1. Properly Designed Lubricant Storage Room
Storage
Lubricant storage is an area where many plants struggle. They fail to see the real value-add in developing a proper lube room to store all new and in-use lubricants as well as all lubrication-related tools such as filter carts and grease guns. Proper storage techniques always must start with designing a proper storage facility (Figure 1). Among other things, this facility should include: proper air handling to regulate temperature and moisture, adequate fire-proof cabinets for accessory storage, work space for filling top-up containers or grease guns, designated filter cart storage areas for each oil type, new and in-use storage space for all lubricants, and a small desk and filing cabinet to track lubricant usages and inventories.
Once your lube room is fully designed and built, and all lubricant-related items are in place and prepared for use, the next major hurdle is to develop a labeling system to employ plant-wide. The labeling system should be developed based on the lubricants that are present in the lube room – no more and no less. This will help keep the labeling system accurate and manageable when the time comes to implement these labels on all top-up containers, grease guns and machines. These labels should be easily identifiable and readable using codes, colors and shapes. Visit www.machinerylubrication.com to see my November/December 2010 article for photos and additional details.
Handling
The next major mistake-inducing variable of a lubrication program stems from improper lubricant handling. You may have created the nicest lube room and the most intelligent labels, but if you cannot get the lubricant from the lube room to the machine without subjecting it to various forms of contamination, all of your efforts and money spent shall be in vain.
Handling is a big misconception for many. It is the same thing most everywhere – dirty old coffee cans, and funnels and grease guns sitting in total filth next to the machines for which they are used.
Proper handling comes from using proper transfer devices, such as washable, sealable and refillable top-up containers with dispensing pumps and nozzles, and grease guns that easily can be filled and cleaned. For large top-ups and drain-and-fills, a filter cart is highly recommended. A cart not only dispenses the oil, but it can be used to decontaminate that oil. Figure 2 depicts proper top-up containers and grease guns. My article from last issue includes a photo of a lube room storage system outfitted with proper dispensing hardware and the previously mentioned labels.
Decontamination
Oil is often changed for the sake of change or is based on the mind-set that the oil is dirty. The only real reasons that oil should be changed are if its physical properties have changed or it has oxidized. You can remove dirt and water through proper decontamination techniques, which can significantly extend drain-and-fills and reduce the costs associated with precision lubrication.
Proper decontamination starts in the lube room. We must not assume that new oil is clean oil, as many times it is not. To properly decontaminate our oils, we must first define our target moisture content in parts per million (ppm) and our target cleanliness levels per ISO Standard 4406:99. These targets will define the level of filtration needed to decontaminate new oil, in-use oil, etc.
To start the decontamination process, first ensure that all drums, totes, storage systems, machines, etc., are equipped with all of the necessary decontamination hardware, such as quick-couplers. Equipping items with quick-couplers will allow for clean, precise and efficient decontamination. Typically, decontamination on machines should be performed on an “on condition” interval. This means that decontamination may or may not need to be performed. It is dependent on the oil analysis report and the current cleanliness level of the oil compared to our predetermined target cleanliness level. Using an “on condition” interval instead of a “time-based” interval will allow for maximization of resources by not performing a task when it may not be needed.
Figure 2. Proper Top-up Containers and Grease Guns
Meeting the Demands
As you can see, lubrication excellence is not just about selecting and using a lubricant and then hoping that it works. Instead, it is about correctly identifying where cost, errors and failures can be reduced by taking the time to properly engineer a complete lubrication program.
The topics discussed in this article may seem to be out of reach for most due to time, money, resources, etc., but they can be achieved through diligence, education and determination. Once you have met the demands of these three major variables, your lube program will be more likely to succeed and receive buy-in from upper management to allow for more development and advancements.
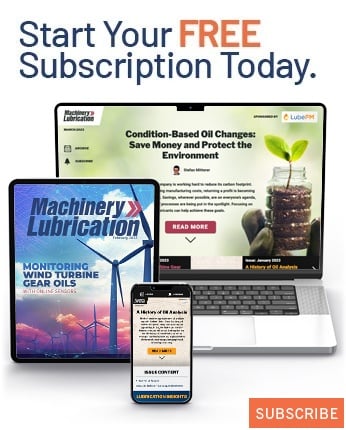