Understanding Contamination in Lubrication Systems
- Particulate Contaminants: These are solid particles such as dirt, metal shavings, or dust that can enter the lubrication system through various pathways, including seals and improper handling.
- Water Contamination: Water can enter lubrication systems through condensation, leaks, or a byproduct of specific processes. Once inside, it can cause rust, reduce the lubricant's film strength, and lead to the formation of emulsions.
-
Chemical Contamination: This includes unwanted chemicals that can mix with the lubricant, altering its properties and reducing its effectiveness. Common sources include incompatible lubricants, cleaning agents, and process chemicals.
The Impact of Contamination on Machine Reliability
Strategies for Effective Contamination Control
Air Sentry Desiccant Breathers
Implementing a proactive contamination control strategy is essential for maintaining machine reliability. Here are some critical steps that can help achieve this goal:
- Filtration: High-quality filtration systems are the first line of defense against contaminants. Filters should be selected based on the type of lubricant and the operating environment. Regularly replacing and maintaining filters is crucial to ensure they remain effective.
- Breathers and Seals: Contaminants often enter lubrication systems through breathers and seals. Aside from ensuring seals are in good condition, using desiccant breathers can help prevent moisture and airborne particles from entering the system. Finding the right breather for your needs depends on several factors including environment, reservoir capacity, application, and more.
- Regular Oil Analysis: Conducting regular oil analysis is vital for detecting contamination early. By monitoring the condition of the lubricant, you can identify potential contamination issues before they lead to significant problems. This allows for timely corrective actions like oil changes or system flushes.
- Proper Handling and Storage: Contaminants can be introduced while handling and storing lubricants. It's important to use clean containers, avoid open environmental exposure, and ensure that lubricants are stored in a controlled environment. Educating personnel on proper handling techniques can further reduce the risk of contamination.
- Maintenance Best Practices: Implementing maintenance best practices, such as routine inspections, timely repairs, and proper equipment operation, can help minimize contamination risks. Regular maintenance checks should include inspecting seals, breathers, and filters for signs of wear or damage.
The Role of Training and Awareness
Conclusion: The Payoff of Proactive Contamination Control
Supplier Spotlight
Pulsarlube USA 1480 Howard St., Elk Grove Village, IL 60007 847-593-5300 | Pulsarlube.com
Pulsarlube provides the most innovative and reliable Automatic single-point lubricator on the market. Backed by years of research and development, Pulsarlube offers a wide range of superior products to meet the needs of our customers. Pulsarlube provides high-quality products and services worldwide through its well-established distribution network.
Esco Products 2501 Central Pkwy, Suite A-5, Houston, TX 77092 800-966-5514 | EscoPro.com
Esco provides solutions for maintenance and lubrication problems in any industry that uses reciprocating and rotating equipment with oil reservoirs. In addition to our revolutionary Visual Oil Inspection product line of sight glasses, Esco is one of Dow & Dupont’s largest distributors of Dowsil sealants and Molykote high-performance lubricants. As a DesCase partner, we offer their full line of breathers and fluid handling equipment. Contact us today to learn more!
Fluid Metrics 4514 Chamblee Dunwoody Rd. #252, Dunwoody, GA 30338 p: 770-393-8636, f: 770-393-8631 | FluidMetrics.com
Founded in 2003 by a compressor industry veteran, Fluid Metrics utilizes the latest lubrication technologies to maximize compressor performance and reliability. When combined with a proactive, condition-based maintenance plan, our advanced compressor oils, purifiers, and conditioners are proven to dramatically increase compressor reliability, slash your oil and parts consumption, and save you time and money. Give us a call today to learn how much easier and better compressor oil maintenance can be.
ITW Pro Brands 4647 Hugh Howell Road, Tucker, GA 30084 800-241-8334 | www.itwprobrands.com
ITW Pro Brands’ innovative product offering includes LPS, SCRUBS, DYKEM, Accu-Lube, Rustlick, and Spray Nine. These premium maintenance/repair/operations chemicals deliver improved performance, inventory simplification, waste reduction, and overall cost reduction. ITW Pro Brands’ extensive product portfolio can be used throughout your facility — from front office to production to warehouse.
Royal Purple One Royal Purple Lane, Porter, TX 77365 281-354-8600 | RoyalPurple.com/industrial/
Formulated for demanding industrial operation needs, Royal Purple® high-performance synthetic lubricants improve reliability, extend drain intervals, reduce lubricant consumption, lower operating temperatures, decrease downtime, and reduce maintenance and energy costs- transforming your Total Cost of Ownership into an investment in excellence.
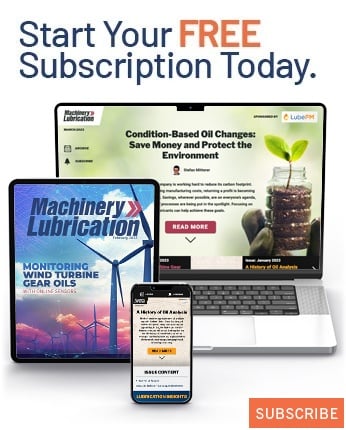