I was recently asked by a hydraulic equipment owner who had just received a new asset to assist him in the development of a change-out strategy for the hydraulic pumps. I was told the hydraulic system comprises a 10,000-liter tank with five Rexroth A4VSO250DP/30R pumps with flooded inlets.
The system has a normal operating temperature of 43 degrees Celsius, pressure and return-line filtration, no suction strainers, oil that is pre-filtered to ISO 15/12 and its condition monitored monthly.
Rexroth A4VSO rotating group cross-section
Unfortunately, there is no reliable “system” for accurately determining pump service life. Historical data is one of the most dependable indicators, but in a new system like this one, you don’t have any. However, there are a range of factors that influence pump life, and when considered together, they can be used to come up with an informed estimate.
The first thing to consider is what do we know about the pump itself.
Rexroth’s A4VSO is an industrial-grade, axial-piston model. “Industrial grade” means it is actually designed for long life (which admittedly, can be a relative term). As I explain in my e-book, Preventing Hydraulic Failures, the fact that it is an axial-piston design means its shaft bearings aren’t heavily loaded and therefore not at high risk of premature failure.
Roller-type, swash-plate bearings in axial-piston designs are prone to premature failure caused by brinelling, but in this pump, the swash bearings are shell-type (more like a bush than a bearing), which means potential brinelling (and subsequent failure) of the swash bearings is not an issue.
Based on my experience and knowledge of this pump model, I’d be looking for a service life of between 10,000 and 20,000 hours. But this is a very wide range, so let’s now consider some of the issues that could determine if achieved service life is at the lower or higher end of this scale.
The type and grade of oil used is a very important factor. If the oil being used is “special purpose,” for example, fire-resistant, this could have a negative influence on achieved service life. The fact the system runs cool (43 degrees Celsius is cool for a hydraulic system) is generally a plus for reliability – both for system components and the oil itself. At this operating temperature, there really is no excuse for temperature-related lubrication issues caused by low viscosity and subsequent loss of oil-film strength.
There is an apparent commitment by the operator to maintain a high level of oil cleanliness, which is known to extend hydraulic component life. The fact that suction strainers are not installed is a plus for pump-inlet conditions, as is a flooded inlet (head of oil above the pump).
These two combined factors indicate that the joint between the piston and its slipper should not be put in tension during intake and that premature failure resulting from piston-slipper detachment is unlikely to occur, assuming the pump-shaft speed stays within allowable limits.
We also need to give consideration to the pump’s actual operating parameters. In other words, how hard is it working? This encompasses how fast it is spinning, at what pressure it is operating and its duty cycle – how many minutes of each hour the pump is under load.
The data sheet for the A4VSO 250 reveals that the maximum shaft speed is 1,500 rpm or 1,800 rpm if the pump’s maximum displacement is reduced or its inlet pressure is boosted.
If the pumps are coupled to six-pole electric motors on a 60 Hz AC supply, they will be spinning at 1,200 rpm, which bodes well for long pump life. If, on the other hand, they are spun by four-pole motors, they will be right on the limit at 1,800 rpm, which is not as conducive to long service life.
Similarly, the A4VSO series of pumps is rated at 350 bar (5,076 psi) continuous. If the pumps’ pressure compensator is set at 280 bar, this is a big plus for service-life extension. Conversely, a setting at or near 350 bar is obviously not as beneficial for long life.
Likewise, if the pumps spend 54 minutes out of every hour (90 percent duty cycle) on load, they are not as likely to be a candidate for an achieved service life at the high end of the scale as they would be if they were on load 42 minutes out of every hour (70 percent duty cycle).
To summarize, if these particular pumps are running on a mineral oil of the correct viscosity, with a cleanliness level of ISO 15/12, with an unrestricted and flooded inlet, are spinning at 1,200 rpm, with their pressure compensators set at 280 bar and at a duty cycle of 70 percent, then it wouldn’t be too unrealistic to expect a 20,000-hour service life and perhaps more.
On the other hand, if they are running on a special-purpose oil with properties inferior to that of mineral oil, are spinning at 1,800 rpm, with their pressure compensators set at 350 bar and at a duty cycle of 90 percent, then a 10,000-hour service life could be quite a challenge.
Of course, this is just an informed estimate based on what we know about the pump and its installation. In a new system like this one, there’s always the possibility a hidden design flaw in the hydraulic circuit may compromise pump life.
For example, the pumps may be subjected to intermittent pressure spikes due to rapid valve shifts and the absence of a spike-relief valve or accumulator. This may only become obvious over time, i.e., after a pump failure.
Since running a hydraulic pump to failure is never a good idea, because there is always the risk of consequential damage to other components, and the pump’s rebuild cost increases significantly, the task here is to manage pump change-outs in a way that minimizes this risk while reliable, historical data on achieved service life is collected.
For example, if we are thinking 20,000 hours is the right number, we might pull out the first pump at 12,000 hours. When it is torn down and inspected, if everything looks fine, we then might pull the second pump at 15,000 hours. If it looks good, pull the next at 17,500 hours.
If that looks OK, the next stop could be 20,000 hours. There will come a point where, if the service-life envelope is pushed too far, the risk of an in-service failure dramatically increases. One shouldn’t get too greedy.
This approach also presupposes the changed-out pumps will be torn down and inspected by someone who knows what he is looking at and who will report his findings with respect to possible service-life extension in an unbiased way.
Although not always conclusive, condition monitoring could also be implemented in an effort to aid decision-making in the staged change-out approach discussed above. However, when it comes to hydraulic pumps, effective condition-monitoring techniques are limited.
In the case of a piston pump, the case-drain line is probably the best source of information, both in terms of leakage rate and wear-metal generation. Of course, to be meaningful, any changes in either of these indicators must be trended over time.
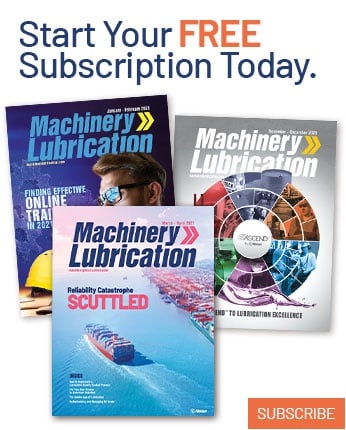