"Recently I've read that it's possible to analyze used oil filters for troubleshooting. Do you recommend this?"
Used oil filter analysis may provide your best evidence of machine degradation, tracing a history of machine particles created and contaminants ingested over a period of time.
Filters are often discarded when changed or not analyzed as a part of a root-cause failure investigation. This disregards a potentially powerful analysis tool.
Ask your used oil analysis lab to perform a filter analysis for you. The filter is sectioned, and the particles contained within are liberated into a solvent with mechanical and/or ultrasonic agitation for analysis. Typical tests include ferrography and elemental analysis. This could unlock the key to your equipment reliability problems.
For example, consider the failure of a highly critical gearbox. During a routine lubricant and filter change, a large amount of metal wear debris was noticed on the filter. An internal inspection revealed a broken gear tooth. Because it was a filtered gearbox, an oil sample from the sump, as well as a filter sample, was sent to the lab for failure analysis.
The results of the oil sample were alarming at first, because no adverse conditions were readily apparent. It was obvious that some evidence of failure must exist in the lubricant, given that this was indeed a mechanical failure of the gearbox. A request was made for the laboratory to perform analytical ferrography on this sample to determine the root cause of failure. Even with in-depth analysis, a final conclusion could not be made.
The decision was made to run wear metals testing on the oil trapped in the filter. This oil told a completely different story.
As expected, spectrometric analysis differed significantly between the sump sample and the filter sample, which can be explained by several factors. First and most important is the sampling method. This gearbox sump was sampled via drop-tube sampling. Drop-tube sampling is not consistent with best practices because it is difficult to obtain a representative sample. It is likely that this gearbox had been shut down long enough for wear debris to settle to the bottom prior to sampling. Secondly, the aftermarket submicron filtration resulted in the removal of severe wear debris, which caused a higher concentration of these fines in the filter sample.
Analytical ferrography was also performed on the filter sample. Wear particles in excess of 30 microns were observed from the filter, and abrasive contamination as large as 125 microns was present. These results suggested that the failure was caused by excessive environmental contamination. In this case, the contamination was most likely entering the system via steel mesh-style breathers.
The system filter element in this application contained the secrets behind the failure. The lubrication technician deserves credit for noticing the wear debris on the filter and doing something about it. Without the critical information trapped in the element, this critical component could have run to failure with no detection until the failure.
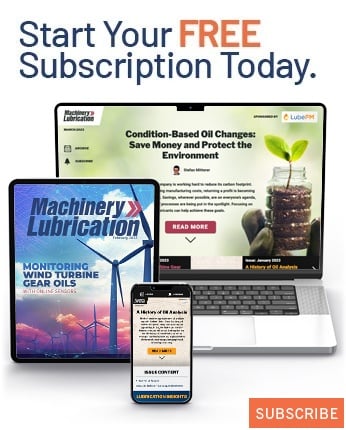