"How can I keep the pressure from my grease gun low to avoid damaging components?"
The key principle to remember for a fixed output grease gun (which covers nearly all grease guns) is this: grease volume and pressure vary with the speed of the lever stroke.
If the grease gun lever is worked quickly, the momentary surge of grease flow through a fixed chamber increases the discharge pressure and will localize the pressure toward the path of least resistance. In a motor bearing cavity, this could cause the grease to surge through clearance gaps toward the winding or perhaps press the cage into the roller.
In a pillow-block bearing, the directional pressure of the grease flow could cause the grease to rupture the shield clearance or escape through a lip or labyrinth seal, preventing the uniform replenishment of grease through the bearing.
A slow, uniform press of the level can help minimize this risk, regardless of the rated output of the grease gun. If the lever is worked slowly, pressure is uniformly distributed throughout the chamber.
If the bearing cavity is full and grease is applied under pressure, the grease will pressurize until either the grease passes through a weak point in the bearing or until the grease gun reaches maximum pressure and the lever cannot be moved any further.
Since an off-the-shelf, general-purpose grease gun can generate pressures in the order of 7,000 psi, it stands to reason that the grease will either find a weak point to pass or will rupture a clearance, seal or passageway and create a new weak point.
To avoid this likelihood, the lube technician may need to install and use a pressure gauge on the output side of the grease gun or “sense” the change in pressure based on resistance at the handle. Once resistance is reached, the lube technician will choose to disconnect the gun and “waste” the remaining stroke.
Zerk fittings with pressure shut-off valves can be most helpful in reducing overpressurization of cavities. A 500 psi limit is desirable for the great majority of applications.
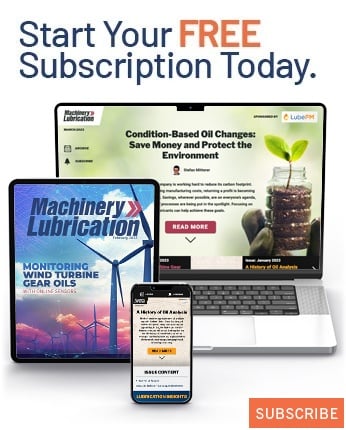