The Curtis Bay plant recycle blower M53304 has a large 1000 HP Babbitt motor and fan oil-lubricated bearings, critical to optimal plant performance. Multiple motor failures resulted in lost production and increased maintenance expenses. Although monitored with an online vibration system utilizing eddy-current displacement sensors, these motor failures have been an ongoing problem for a long time.
It was only resolved with detailed vibration diagnostic information from the online vibration system to help address this problem. Connecting an AMS 2140 to the motor's online vibration monitoring system enabled the plant reliability staff to obtain detailed rotor displacement peak and phase vibration data. This route-based spectral, waveform, and phase data were combined in the AMS machinery manager software in an orbit plot format to help identify faults, such as:
- Imbalance
- Bent or bowed shaft
- Eccentricity
- Shaft preload
- Resonant response
- Machinery stability
- Mechanical looseness
- Rotor rub
- Misalignment in the drive shaft
- Cracked shaft behavior
- Foundation considerations
- Oil instability (Oil whirl and Oil whip)
In this case, we can correct a dynamic misalignment.

The Challenge
These critical plant assets are routinely monitored with online vibration systems for shutdown protection through a Bently Nevada 3500 rack and/or overall vibration data indicated on an operator's control panel. Although these online vibration systems are functional, in some cases, the lack of diagnostic information hinders the reliability team from assisting the plant with improving the asset operation. A failure of that asset can decrease plant production and incur additional unplanned maintenance shutdown expenditures. Employing the capabilities of the portable data collector to extract vibration data from an online system's buffered outputs with route-based measurements can enable the utilization of in-depth vibration information for monitoring & diagnostic purposes consistently.
Interfacing the Portable Data Collector with an Online Vibration System
The data collector has an accelerometer and volts inputs, which can be used to measure online accelerometers and eddy-current displacement sensors via a connection to the online systems buffered output. Vibration data can be obtained from the routes, advanced analysis testing or transient firmware and then that data can be saved as a job in the AMS machinery manager software.
As the system already powers online sensors, caution must be taken to ensure the data collector does not have sensor power turned on when connecting to the online system for measurements. One method to ensure this would be to create machine points in the software with the sensor power 'turned off' and then create a separate online system route to ensure that no power could be input to the online systems' buffered output connectors. Collecting the online vibration data with a dedicated route would also allow that information to be trended over time for comparison to data/outputs from the online protection system. Energy bands included in the route points could be used for enhanced trending and alarming, making it easier to interpret the data.
Vibration Data
One recurring plant maintenance concern was an asset on a critical system impacting plant operations when a motor had repeated DE bearing alarms but lacked diagnostic information to provide corrective measures to resolve this problem.
The alarms came from the dynamic displacement when we started the equipment and the shaft floating over the oil from the babbitt bearing in an offset position.

The Curtis Bay reliability team utilized the D25688 \ Splitter Cable, 8-pin M12 to BNC 0.2m" red, blue (Volts A & B) and tack, which plugs into the data collector Turk connector to collect measurements. This cable allows you to connect to 2-eddy-current probes and a TACH signal from the protection rack for displacement peak & phase data.
Once the measurement points and route were built, the reliability team successfully collected rotor displacement vibration data at 1185 RPM on the two fans for analysis. Our measurement points parameter settings include subharmonics, 1xRPM Peak-Phase, 2xRPM Peak-Phase, 3-4xRPM, and DC Gap Voltage parameters be included in this monitoring. As standard sensor measurements are configured with the analyzer sensor power turned on, it was also recommended to configure these points with the analyzer sensor power turned off. An additional precaution was to have these measurement points built into a special online system vibration route to ensure no power was accidentally input to the online system buffered outputs.
Machinery manager software was then used to view the fan trend, spectrum, waveform, orbit, and DC gap eddy-current data. This data confirmed the reliability team's suspicion of an alignment problem on the fan where the motor sleeve bearing failures occurred. A decision was made to adjust the motor alignment to 1.5 mils down and 4 mils to the left. The following orbit plots show the motor bearing displacement before and after the alignment change was made.

Eddy-current displacement vibration orbit plot before alignment change.

Eddy-current displacement vibration orbit plot after alignment change.

Motor eddy-current displacement vibration multi-spectrum plot before and after alignment change.

Motor eddy-current displacement vibration waveform plots before and after alignment change.
Conclusion
A detailed analysis of the machine orbit plots collected with the AMS 2140 from the Bently-Nevada rack 3500 resulted in the recommendation for maintenance to align the motor to the fan differently. The misalignment defect was a primary source of the repeated motor DE bearing alerts and failures on this machine. Since this alignment change, the troublesome motor has run perfectly, and this improvement of the motor operations is considered a success for plant production. While the examples above were identified using a portable machinery health analyzer, the Curtis Bay FCC and reliability team continued monitoring online vibration spectral, waveform and orbit data.
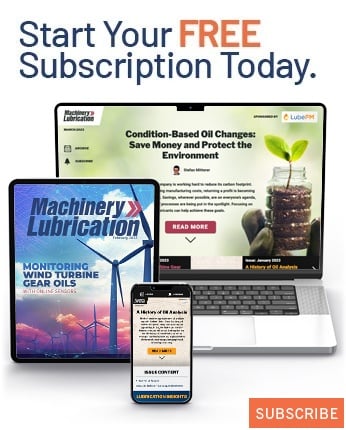