"As oil ages, it oxidizes. What is the best indicator that the oil has oxidized too much and should be changed based upon the results given in a typical oil analysis? We analyze the oil from our mixer gearboxes and will typically run the same oil in the gearbox for several years as long as the oil analysis comes back with good results."
The first issue here is to define a "typical" oil analysis. Most labs have several test packages to choose from that may or may not give an overall solid feel for lubricant oxidation. In order to identify lubricant oxidation, it is important to include oil properties monitoring as part of your regular test package. This will allow for the extension of drain intervals based on lubricant condition as well as help to identify adverse operating conditions that may exist. In some applications, you may even be able to keep re-using oil indifinitely by implementing an oil regeneration system to remove the nano-size contaminants that conventional filtration cannot address.
Common tests that cover lubricant properties include viscosity, neutralization number (acid number for industrial-based lubricants, base number for mobile equipment) and FTIR. The values of the results in all of these tests will increase as the level of oxidation increases (with the exception of base number, which will decrease as the level of acids increase via the oxidation process).
A couple of common field tests that can help to indicate possible oxidation are darkening color and foul odor. Oxidation usually has a sour or pungent odor, similar to rotten eggs. It occurs when the hydrocarbon constituents of lube oil combine chemically with oxygen. As with the laboratory tests, it is important that sensory testing is compared to that of a virgin oil base sample.
Just like with most chemical reactions, oil oxidation is accelerated by heat and pressure. It is no different than other commonly encountered oxidation reactions, such as rusting. Just like the effects that rusting and other corrosive processes have on metal substrates, oil oxidation results in a catastrophic and permanent chemical change to the base oil molecules. The net effect of prolonged oxidation is that the oil becomes acidic (chemically), causing corrosion, while an increase in viscosity occurs (physically).
Oxidation will generally happen at a slow rate under optimum conditions; however, as the health of the lubricant decreases, the rate of degradation will increase. There are several other factors that, if not controlled, can lead to increased rates of oxidation. These factors include heat, air, water and metallic particles.
Using a combination of these tests will assist in pinpointing positive levels of oxidation. Combined with appropriate equipment monitoring tests and contaminant tests, root causes of oxidation can also be found and controlled.
Eventually, oil oxidation will force you to dispose of old oil to replace it with new, clean oil. However, some plants are beginning to look at oil costs more holistically. Rather than focusing on extending drain intervals (and ultimately still paying to properly dispose of old oil), some facilities have begun to regenerate oil so that it can be used again and again. This is enabled by new technologies, but also represents a shift in how we think about oil serrvice life and the costs associated with lubrication as a whole. In this ever-evolving industry, keeping up with new technologies could lead to transformative results in your lubrication program. Be sure to consider your options and talk with solutions providers who may be able to help you achieve goals in ways you have never considered before.
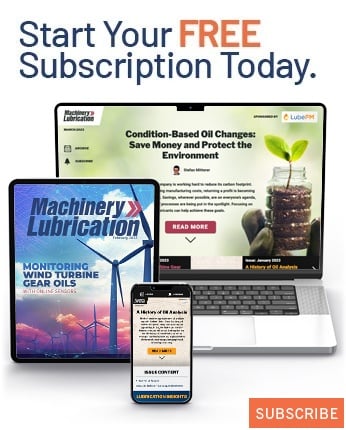