At a recent site meeting where I was investigating a series of premature hydraulic pump failures, the client opened the proceedings with a brief history on the machine, an account of the events leading up to the failures and then pushed a stack of oil analysis reports across the table.
After I finished taking notes on what I’d just been told, I inquired about the hydraulic system’s normal operating temperature range. An uncomfortable silence filled the room. Eventually, the client shrugged his shoulders. I then asked about the hydraulic system’s operating pressure range. With a blank and partly worried look, the client replied, “Err... dunno. We don’t monitor either of those things.”
90% | of lubrication professionals say a lack of attention has negatively impacted the reliability of equipment at their plant, based on a recent poll at machinerylubrication.com |
At the end of the meeting, we took a walk to the control room. As it turns out, both operating pressure and temperature were displayed on the default screen of the programmable logic controller (PLC). This crucial data, from a reliability perspective at least, was hidden in plain view among a lot of apparently more important and closely watched production information.
In my experience, such narrow concentration of attention within departments is not uncommon. The result is something called inattentional blindness - too busy looking at one thing to see some other thing that is equally or even more important.
It might sound trivial, but inattentional blindness can be fatal. On Dec. 29, 1972, Eastern Air Lines Flight 401 was forced to abort its initial approach for landing into Miami, Fla., because the light that indicates when the plane’s nose wheel is down and locked into position had failed to illuminate.
After flying around and pulling up to 2,000 feet, the captain and his co-pilot became so fixated on the suspect light fixture that they failed to notice that the autopilot had been disengaged.
As the plane dropped through 1,750 feet, an altitude warning alarm, which was clearly audible on the black-box recording, went off in the cockpit. However, both pilots were so focused on the light fixture that neither of them consciously registered the noise.
Co-pilot: “The tests didn’t show that the lights worked anyway.”
Captain: “That’s right.”
Co-pilot: “It’s a faulty light.”
Directly in the pilots’ line of sight, the altitude meter was spiraling downward. It’s possible both pilots actually looked at it but failed to register what it was telling them. Only when the plane was 7 seconds from impact did the co-pilot finally realize that something was seriously wrong.
Co-pilot: “We did something to the altitude.”
Captain: “What?”
Co-pilot: “We’re still at 2,000, right?”
Captain: “Hey, what’s happening here?”
The captain pulled back hard on the stick, but it was too late. The plane crashed into the Florida Everglades, killing 101 people. The nose wheel did in fact lock into position during the initial approach. It was the $12 indicator light that was faulty (the bulb had burnt out).
The Importance of Visual Inspections
Many equipment inspections are visual, and checking oil levels is the most common visual monitoring activity. Numerous potential machine failures are prevented by an attentive individual who notices a low or nonexistent oil level. Other valuable functions can also be performed as part of the visual inspection. Lubricant issues such as oil contaminated with water or other materials, badly degraded or oxidized oil, and excessive foaming, as well as other machine conditions including excessive vibration, loose belts, loose drive chains and loose or missing fasteners are all examples of what should be routinely documented and scheduled procedures. This should serve as the foundation of a condition monitoring program, no matter how sophisticated.
This is a dramatic (and tragic) example of being too busy looking at other things to see something that’s really important - and one that had dire consequences. On a different level, I see this a lot in my consulting work. Clients often come to me fixated on one issue or problem, when in fact there is a more significant one staring them in the face that warrants their attention first. Usually this is not due to a lack of understanding but rather a lack of attention or, more precisely, a misallocation of attentional resources between or within departments, similar to the situation described at the beginning of this article.
One of the best assets a consultant in any field brings to the table is a fresh set of eyes. Had a third pilot walked into the cockpit of Eastern Air Lines Flight 401 as the drama was unfolding, it’s highly likely his “fresh eyes” would have immediately seen what the incumbent pilots could not.
My wider point is that none of us is immune to inattentional blindness. The first step in avoiding its pitfalls is to be conscious of it.
The crash of Eastern Air Lines Flight 401 changed the way pilots are trained. The problem with the faulty light bulb was not just that the captain fixated on it, but that the co-pilot did, too. The entire available pool of attentional resources was focused on a single thing.
To avoid this situation whenever you are operating, maintaining or troubleshooting hydraulic equipment, regularly ask yourself: What else should I be paying attention to right now?
.
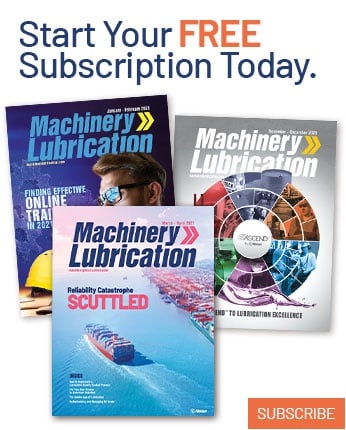