Oil analysis plays a critical role in a lubrication program, allowing you to have confidence in the quality of the lubricant in a machine and to analyze the health of the machine in its current state. The problem is that several facets of oil analysis must be performed correctly or the integrity and validity of the entire program will be at risk.
The first requirement for effective oil analysis is to obtain a representative sample. This involves using proper sampling bottles (discussed in Part 1 of this series), employing appropriate extraction tools and procedures (detailed in Part 2), and determining the optimum sampling location and frequency, which is the focus of the third and final part of this series of articles.
64% | of lubrication professionals rate machine criticality as the most important factor to consider when adjusting oil sampling frequency, according to a recent survey at MachineryLubrication.com |
Where to Sample
In all the time I’ve spent walking around heavy machinery at plants, the one thing I seem to always find lacking is the proper location to sample oil. If a sample is not taken at the right location and in the correct manner, it becomes increasingly difficult to ensure the representative nature of the oil analysis results. Successfully trending data becomes even less of a possibility.
5 Variables for Calculating Sampling Frequency
- Economic Penalty of Failure – Sampling should be taken more frequently when the cost of downtime, repair, rebuild, interruption to business and/or impact of product quality are high.
- Fluid Environmental Severity – Sampling should be taken more frequently when demands placed on the lubricant by the environment and/or the machine are high.
- Machine Age – Based on the “bathtub curve,” sampling should be taken more frequently when the machine is young (infant mortality) or old (surpassed maximum useful life).
- Oil Age – Same as machine age, during the life of a lubricant in a machine, samples should be taken more frequently when the age of the oil is new or old.
- Target Tightness – Sampling should be taken more frequently when oil analysis targets (such as ISO particle counts) are approaching or consistently near the goal-based limits.
Choosing the sample location should be based on obtaining fluid in a machine’s most important lubrication zone - the live zone. For a rolling-element bearing, this would be the lubricant between the rollers and the race. For a gearbox, it would be the lubricant between meshing gear teeth. While it may not always be possible to take a fluid sample adjacent to the gear teeth, attempting to sample in close proximity or where the fluid returns back to the reservoir can be just as effective for maximizing data density and minimizing data disturbance.
Following are sample locations for three types of machines: a dry sump circulating system such as a turbine lube oil system, a wet sump circulating system like a diesel engine, and a non-circulating system such as a bath/splash-lubricated gearbox.
Circulating System Sampling
A dry sump circulating system contains a central reservoir, a pump, various components to be lubricated, a filter and piping to connect them all together. A sample for this type of system should always be taken just downstream of components that may produce wear, since any wear particles produced will be among the most important properties of the oil.
Because several components are being lubricated, the “live zone” for sampling is in more than one location. This requires a sample to be taken after the lines converge on the return lines but before being passed through a return-line filter and back to the reservoir (in the case of a hydraulic system). This sampling location provides a good representative oil sample for the system as a whole before valuable wear data is removed by the filter.
In addition, it is always best to take a sample where the fluid becomes turbulent. To identify a turbulent sampling location, determine where the fluid is forced to turn and tumble, such as on a pipe elbow. This is important because without turbulence, heavier particles, such as wear debris, can be pushed past sample valve ports, especially with high fluid velocity. This particle fly-by phenomena can result in false low particle readings. If there is sufficient pressure, a sampling tube with an adapter affixed to a minimess valve can be used to draw the fluid into a certified clean bottle once the sampling lines have been flushed. If there is not sufficient pressure, a vacuum sampler pump will be required.
When abnormal wear is evident in a primary sample taken after the lines converge, it will be necessary to obtain samples at secondary locations to determine where this wear is being produced. These sampling locations should be positioned immediately after the lubricant discharges from the component (e.g., bearing) before the line branches into the return header.
Circulating Wet Sump Sampling
Taking a representative oil sample from machine live zones can be challenging with a wet sump system, such as a diesel engine or circulating gearbox in which a return or drain line is not accessible or does not exist. In this type of system, there is a pressurized supply line or a kidney-loop filtration system. With a system containing a pressurized supply line, the most appropriate sampling location may be after the pump but before the filter. Because the sample is taken at a pressurized point, the best sampling valve option is a minimess valve, which ensures no disturbance to the machine’s operations.
Wet sump sampling after the pump but before the filter
If the wet sump is configured with a kidney-loop filtration system, a similar sampling location can be selected. For this configuration, a minimess valve for sampling can be installed after the pump and before the filter in the same manner that the supply-line system was equipped, since the system is also in a pressurized state. Many filter housings have convenient ports just upstream of the filter, which are often used for pressure gauges.
Non-Circulating System
In systems without any circulation of lubricating oil, the primary means for obtaining a sample will be through the system’s sump casing using a pilot tube from the sample valve to draw fluid from a turbulent, live-zone location. These types of systems will have a drain plug either near or at the bottom of the sump. This is where the sample port can be installed along with a T-adapter to allow for the addition of a ball valve for draining. Minimess valves can be installed at an oil level port where a sight glass is typically situated. If this port is the most accessible, then a device that enables both sampling and sight glass functionality will be necessary.
During installation, the pilot tube should be carefully positioned so the tip is in an ideal live-zone location. Generally, this will be halfway up the oil level and a sufficient distance from any walls. It must be close to turbulent areas but no closer than two inches from any moving elements or walls within the system. The best hardware to use in conjunction with the minimess sample port would be a vacuum sampler. This helps ensure that the sample never comes in contact with the environment.
Sampling Frequency
How often should sampling be performed? This is not a simple question. Basically, it is a tradeoff. Sampling less frequently can risk missing a machine or lubricant failure, while sampling more frequently can risk wasting time and money (and even lubricant). A better question would be, “What are the variables that help calculate the optimum sampling frequency?” These variables would include the machine age, oil age, target tightness, fluid environment severity and economic penalty of failure. For a description of each variable, see the sidebar above.
Sampling Frequency Variables
All of these variables are best determined by the individuals who are most familiar with the machine being sampled. Many of these questions asked about the machine are subjective, and the most effective way to develop appropriate answers is to use historical information related to past machine failures, machine criticality, lubricant type, failure modes, lubricant change-outs and top-ups, adjustments to oil analysis targets over time, fluctuations in environmental conditions, etc.
Simply stated, the more you know about the machine, the better you will be able to calculate the optimum sampling frequency in relation to the key variables. Often you need to make intelligent adjustments to machine sampling frequency to optimize the value gained from oil analysis. This subject is discussed more extensively in Jim Fitch’s column on Unified Condition Monitoring..
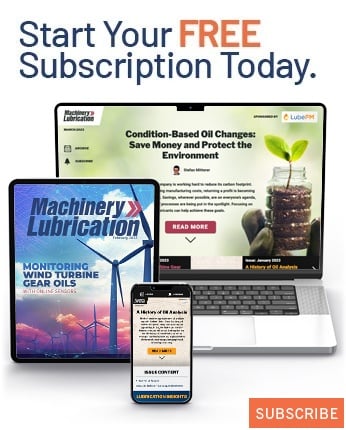