The differences between standard-performance, high-performance and specialty-performance lubricant products are not always clear. The fact that these three categories of products are all marketed to an array of mechanical and operating conditions complicates the selection process.
What are the differences between each of these three quality grades or types of products? Is there a place for high-performance and specialty products in the typical industrial environment? Is there any reason not to select a product that arguably performs at a level higher than the given application? Let’s consider the arguments.
What’s in a Name?
First, let's define the product categories more thoroughly.
Standard-performance products are sold in bulk and perform the minimum function required for effective operation. These are largely purchased for broad-based use through price-driven agreements. Product selections, regardless of the brand name, might be characterized as minimum-performance products because their construction is intended to meet minimum operating requirements. Roughly 80 percent of mechanical components can be effectively lubricated with these common fighting-grade products.
High-performance products are manufactured with specialized raw materials. The materials offer greater performance capability (load-supporting characteristics, higher wear resistance, extended lifecycles) to the finished lubricant. Common examples could be greases fortified with solid film agents (molybdenum and graphite), high VI hydraulic oils manufactured with severely hydro-treated base stocks and ashless antiwear agents, or gear oils fortified with solid film agents to improve sliding frictional resistance. Roughly 20 percent of plant applications would be well served with high-performance lubricants.
Specialty-performance products are intended for use in extraordinary service. Lubricated components used in a radioactive environment, the vacuum of space, or for compressing oxygen and/or pumping corrosive fluids are appropriate candidates for a specialty lubricant. This type of lubricant is considered chemically and physically stable (nonreactive) for the select environment.
These materials operate at temperatures to 600°C, under vacuums, under exposure to contaminants that would quickly destroy other lubricants. The disadvantages of extra stability include that in many cases these products don’t protect surfaces well due to their compressibility, their inability to support useful additives, or their inability to react with a metallic surface under boundary conditions. One to two percent of plant applications would be well served with a specialty lubricant.
The price interval between the specialty and commodity product is approximately 200 to 400:1. The price alone may limit interest in the use of these, literally, space-age technologies, so it is less likely that these will become entangled in lubricant selection debates.
Optimize Lubricant Selection Decisions
Lubricants from each of these product categories can be chosen for a variety of component types, including open and enclosed gears, element bearings, plain bearings, linear bearings, chains, screws, compressors, hydraulic systems, static sumps and dynamic (circulating) sumps. Regardless of the mechanical component interaction, most brands manufacturer a fighting-grade product and a performance or high-end product. Few of the major brands design, manufacture and market “specialty” lubricants.
Is there any real performance difference between the commodity lubricants purchased through price-conscious decisions, and the premium-price lubricants that fluctuate above and below $1,500 per drum mark? Yes, and the performance differences may be clearly measurable. Common differences include:
-
Thicker oil at high operating temperatures (+- 200°F)
-
Thinner oil at low operating temperatures (+- -20°F)
-
Improved separation from moisture, which enhances surface protection and extends lifecycles
-
Reduced formation of hard carbon deposits on noncontact surfaces
-
Better resistance to aging (oxidation), which promotes longer oil lifecycles
-
Improved load-bearing capacity, which promotes reduced component wear
Secondly, is there a justification to select the higher price materials at three to five times the price of other generic products? Yes, but only following a successful outcome from a reasonable business value analysis that includes efficiency and reliability improvements for both production and maintenance interests. A few maintenance criteria to consider include the following:
-
Total lubricant material cost differential per year
-
Differential in annual relubrication labor cost
-
Differential in annual replacements of lubricated machine components, preferably measured over a multiyear baseline
-
Differential in annual component replacements through collateral damage from failure events, preferably measured over a multiyear baseline
-
Differential in annual labor to replace components during the given time periods
-
Differential in apparent wear rates as demonstrated in properly executed oil analysis
Production costs could include the following:
-
Differential in annual lost production opportunity
-
Differential in scheduled and unscheduled downtime for mechanical repair
-
Differential in annual energy consumption
-
Differential in annual scrap production hours or units
Any one of these factors could represent a major cost reduction opportunity in itself, delivering a discounted cash value estimate (return on investment) many times the actual cost differential for the higher cost material.
Once the current-condition cost factors are determined, a reliability engineer can project an improvement plan based on experience, agreeable measurements or comparison to identical operating system (if any exist). In reality, a small amount of demonstrated improvement in mechanical operating conditions leads to the creation of significant new value to the organization, particularly if the plant is in a sold-out position.
Loss of Value
Poorly engineered application of alternative high-performance products can also decrease value. Regrettably, people with good intentions tend to over-apply high-performance materials to machines where the expected tribo-mechanical benefit cannot be realized.
When this condition exists, there should be a concerted effort to modify replenishment volume and/or frequency, in order to minimize the material purchase cost differential. Doubling the traditional sump change interval may be sufficient to offset the increased material cost. Fortunately, sump change intervals can be extended four to five times the traditional interval with careful condition analysis of the lubricant.
Although real impact to plant profitability (from the pointless use of a high-performance material) is low, there is no reason to waste resources.
Lubricant Purchases: Less than a Rounding Error
The relative impact of lubricant purchases to the net profitability of an enterprise over the course of a year - regardless of the lubricant’s cost per gallon - is irrelevant. Cumulative lubricant purchase dollars represent approximately one to three percent of annual maintenance purchases in most plants. While there is no norm for maintenance expenditures as a portion of total operating costs, eight to ten percent is not uncommon. Assuming that the maintenance portion is ten percent means that for every dollar of goods produced, the company will spend 1/10th of one cent on lubricant purchases.
Properly selected high-performance lubricants may create cost reductions many times greater than the price differential between the product types. Selecting a performance option should be based on the effect derived from a carefully engineered change, with the expected results calculated into commonly accepted financial terms.
Need help optimizing lubricant selection for your machinery? Noria Corporation provides vendor-neutral lubrication program consulting and services.
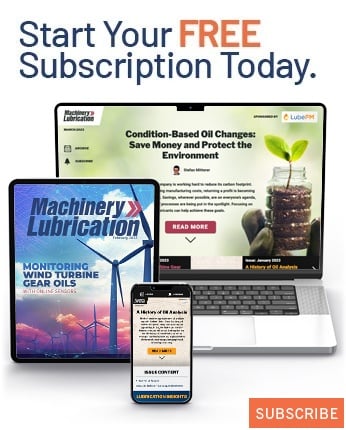