"Varnish contamination is a common problem in many gas turbine oils. Does this type of contamination have polar properties? Numerous papers are available discussing varnish contamination, its causes and remedies. In most of these papers, the polar properties of varnish content have been accepted as proven fact, but our research and experiments do not support this. What is your opinion on the matter?"
In general, varnish is known to consist of polar properties. However, it can also contain non-polar constituents. Varnish is not easy to define because there is no single type. Many things affect the kind of varnish that forms, including the operating conditions, the type of oil and the environment.
Rather than attempting to place specific parameters on the properties of varnish, below is a list of 10 things that should be understood about varnish as it applies to lubrication.
- Varnish formation can begin from the oxidation and polymerization of lubricants and other fluids or pressure-induced thermal degradation and dieseling. The figure below illustrates the primary mechanisms for varnish formation. Although there are many other causes of varnish, these are the most notable.
- Varnish typically is submicron in size and primarily consists of adherent oxide or carbonaceous material. Its constituents can be sourced from thermo-oxidative compounds of base oil molecules and additives as well as wear metals and contaminants like dirt and moisture. Cyclical transitions between heating and cooling expose the oil to thermal degradation and oxidation.
- The formation of varnish and sludge results from the precipitation of high-molecular-weight insoluble oxides from the oil. As primarily polar substances, these oxides have limited solubility in non-polar base oil like turbine oil.
- This creates a thin, insoluble film that coats the interior surfaces of machine parts and causes sticking and malfunctioning of close-clearance moving parts like servo-valves.
- The appearance of varnish on interior machine parts can transition from a tan color to a dark lacquer-like material.
- Varnish can also be caused by entrained air bubbles undergoing an adiabatic compression in load zones. These air bubbles are compressed rapidly, leading to thermal decomposition of the oil and additives.
- During the initial stages of oxidation and the formation of oxidation byproducts, Group II base stocks are more resistant. However, as more oxidation byproducts form, these base stocks can be more susceptible to varnish issues due to their higher level of polarity.
- Operating conditions such as high-pressure differential zones, long dwell times and contaminants like water can promote oxidation.
- In addition to a darkening of the oil, the varnish potential can be visually monitored by recognizing any residue, tar or gummy-like material in sight glasses, interior machine surfaces, filter elements and centrifugal separators.
- Varnish potential can also be monitored through oil analysis using Fourier transform infrared (FTIR) spectroscopy, an ultracentrifuge, colorimetric analysis, gravimetric analysis and membrane patch colorimetry (MPC).
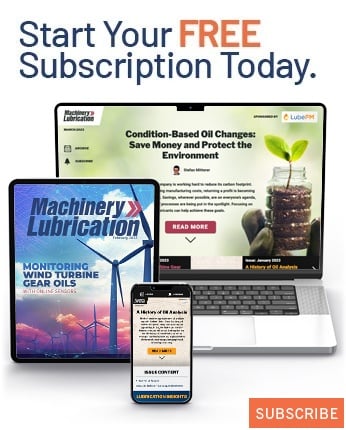