Wind-energy asset owners are confronted with critical business decisions as their wind farms approach the end of their operational lives. This forces these decisions to be made around life extension, repowering or full decommissioning for these assets.
Despite continuous innovation in designs, lubrication systems, improvements in the different materials and lubricants used, maintenance problems in wind turbines still persist. They persist mainly as a consequence of the fatigue of the components or by external contamination (water, air, dust particles), thereby causing a drastic reduction in the useful life of these components.
If we consider the outbreak of the health crisis caused by Covid-19 and the Russia-Ukraine war, the lubricant industry has challenges with the limitation of raw materials, especially processed oil. The lack of this component delays the manufacturing processes of oils and greases, and therefore, requires that end users, in the case of large wind-turbine manufacturers, implement new tasks that allow the life extension of these products before an imminent reduction in their supply.
Through the study of these events, we have been able to understand these modes of degradation, which has led us to propose new alternatives within the OCM – Oil Condition Monitoring programs. These programs have allowed us to improve the early detection of possible failures, thus extending the useful life of the wind turbines.
Introduction
With a service contract including upgrades to improve and extend the original design life, wind turbines can keep producing for up to 10 additional years with minimal risk. Repowering by installing larger and more efficient turbines is also an attractive option, which can be combined with life extension.
However, repowering can be made difficult by lengthy and uncertain authorization procedures. It requires additional investments in decommissioning and new turbines.
Decommissioning the wind turbines may be relevant if neither life extension nor repowering are viable options. In this case, the asset owners incur the immediate costs of clearing the site, as well as the opportunity cost of not having their permits extended.
To do so, the wind-turbine components must be inspected to ascertain their integrity and the risk of failure during continued operation. The type of inspection may vary based on the extent of operational data available and the problems encountered previously by the turbine’s components.
Despite these options that are available to start up, it has been demonstrated that many turbines are able to operate beyond their design lives.
Future Trends To Expect in OCM
According to recent studies from WindEurope, within the next five years, approximately 38 gigawatts of European wind farms will reach 20 years of operations, which means that there is a large number of turbines (around +35,000), representing 16% of installed wind capacity in Europe. Without a doubt, the decision on lifetime extension is complex, and experiences to date are limited. Most of the aging capacity is in Germany, Spain, France, UK, and Italy, which also have out-of-date fleets.
From 2021 to 2028 an average of four-gigawatt turbines per year will safely and profitably extend their operational lifetime. Results indicate that end-of-life solutions will develop a significant market over the next five years.
The application of updated load simulation and inspections for technical lifetime extension assessment differs between countries. A major concern is the uncertainty about future electricity spot-market prices, which determine if lifetime extension is economically feasible.
In several instances, the lifetime of a wind farm may be extended through minor and low-cost repairs. Through this project, it has been possible to demonstrate during the last few years that monitoring the different components through oil analysis and being able to better anticipate possible failures, has helped a lot in the extension of the useful life of these components.
Conclusions
I. Oil Condition monitoring (OCM) has proven to be a very valuable tool within the wind industry and should be installed to identify changes in the turbine’s components. As a result, remedial action can be better planned to maintain reliability in a cost-effective manner.
II. As part of Life Extension through the OCM, all critical components of the load-path of the turbine must be evaluated to secure a thorough maintenance program. These components include: gear box, main shaft bearings, bearing housing, bearing housing (bedplate bolted joint), yaw system, main bearing, blade bearing, and hydraulic system.
III. The level of wear in most of the turbines may have resulted in lower load capacity than originally estimated. As a result, the gearbox of the turbine is often free from significant damage. Therefore, in many cases, the repairs needed to extend the lifetime of the turbine are generally minor and cost-effective.
IV. Many failure modes have measurable response and develop over time. These are the ideal applications for condition-based maintenance (CBM). OCM can provide early warning of potential failure if the measurement parameters are correctly chosen and measured with accurate methodology using the visible spectroscopy (color) technique.
V. It has been possible to apply a very fast technique - color in gearbox oils, that allow us to establish an excellent relationship between certain standard variables, such as acid number or metals by AES-ICP, FTIR.
VI. This new degradation oil method is capable of fully quantitatively determining the color of the oil sample, as well as different characteristics that can be evaluated by analyzing its visible spectrum. This method also makes it possible to detect incipient stages of oil degradation, unlike traditional methodologies that are only sensitive at advanced stages of oil degradation.
VII. The results obtained are only applicable for those lubricating components. This study does not cover other important parts within the turbine for which it is not possible to apply the OCM technique.
Many countries around the world that installed their first wind farms are now reaching the end of their planned service life, meaning decisions will soon need to be made around life extension, repowering, or full decommissioning for these assets. Life Extension is a cost-efficient and profitable method for maximizing the initial investment. The OCM technique can help ensure major decisions like these are made carefully and with consideration to the condition-based factors discussed in this article.
This article was from the authors' conference presentation at the 2023 Reliable Plant & Machinery Lubrication Conference & Exhibition. To learn more about Reliable Plant & Machinery Lubrication 2024, click here.
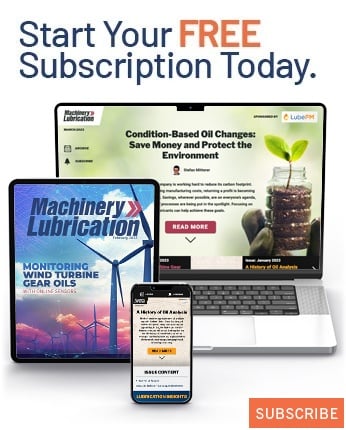