How It
Works
Users are assigned an e-mail address to give to their lab. The lab then sends
reports as attachments to the customized address. The information contained
in the report is then added to MaintenanceGuy and the user is notified of the
new information via e-mail or pager.
Step 1. Lab E-mails Results to Customer@dingo.com.
Step 2. MaintenanceGuy Alerts Customer of New Results by E-mail or Pager.
Step 3. MaintenanceGuy Automatically Adds New Results to Customer Account on the Web.
User
Controlled Data and Reports
Because MaintenanceGuy is similar to other software applications, users control
their own data. They can add, edit, delete and save equipment and data just
like a regular PC application. Users can also select equipment for customized
reports. Installation, maintenance and data backup is provided through this
service and because the program resides on a central server, software upgrades
occur automatically, meaning that users always have access to the latest version
whenever they login.
User
Defined Trend Groups
MaintenanceGuy’s trending module enables users to configure and save specific
graphs and trend lines customized for specific equipment and site conditions,
allowing user-friendly visual detection of problem trends. Some examples of
customized view groups that have been setup by users include data trends to
identify blow-by in diesel engines, coolant leaks, dirt ingression, bearing
wear, as well as ISO particle count trends to monitor the progress of contamination
control efforts. Each component in the database can also have a unique default
view.
Collaboration
The Internet enables collaboration as never before, and MaintenanceGuy encourages
this. Customers can give key suppliers access to a MaintenanceGuy Internet account
so that vendors can add their expertise to help diagnose and solve problems
making MaintenanceGuy a truly unique problem-solving tool.
According to Dingo, the software will allow the lubricant supplier to review how his additives are performing at the same time an OEM is providing metallurgical insight to the meaning of current wear metal trends. MaintenanceGuy also enables lab technicians and mechanics to login and add comments, which can then be viewed by assigned vendors.
One of the biggest advantages for multisite operations is the ability to compare oil analysis information from similar units at different sites and pool the results to make better-informed decisions.
Backup
Dingo’s secure servers back up all data on a daily basis.
Information can
also be backed up to an Excel file on a CD upon request.
Independence
MaintenanceGuy operates independently of oil analysis labs, equipment suppliers
or other vendors, and Dingo provides its services directly to the end-user.
MaintenanceGuy enables users to contract with any testing lab or even multiple
labs if they prefer. The software also supports onsite testing equipment, allowing
data from both lab analysis and onsite measurement to be combined into one database.
The biggest advantage to this independent approach is that if a user changes labs, all historical data remains intact, and results from the new lab can be routed to the existing database, ensuring consistency and continuity.
The online application reduces the administrative aspects of oil analysis - such as paperwork and filing - without adding the hassles of maintaining and upgrading software. MaintenanceGuy provides oil analysis practitioners with a useful tool for professional oil analysis management.
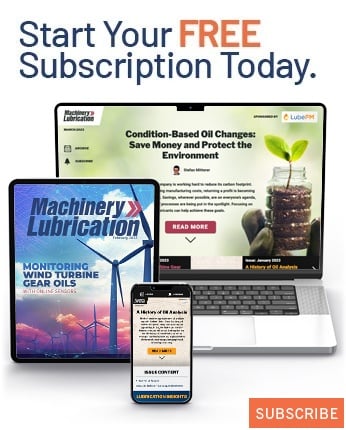