What is an Electric Motor?
An electric motor is a device that converts electrical energy into mechanical energy. It is a common type of motor used in various applications, ranging from industrial machinery and household appliances to electric vehicles and robotics.
The basic principle behind an electric motor involves the interaction of magnetic fields and electric currents. Typically, an electric motor consists of a stationary part called the stator and a rotating part known as the rotor. The stator contains a set of electromagnets that generate a magnetic field when an electric current flows through them. The rotor, usually equipped with coils of wire, carries the electric current.
When an electric current is applied to the motor, it creates a magnetic field in the stator. This magnetic field induces a force on the coils of wire in the rotor, causing them to interact with the magnetic field and generate a rotational motion. The rotor starts to spin, resulting in mechanical output.
Electric motors can be categorized into various types based on their construction and operational characteristics. Some common types include:
DC Motors: These motors operate using direct current (DC) and are commonly found in applications like electric vehicles, household appliances and small machinery.
AC Motors: These motors operate using alternating current (AC) and are widely used in industrial machinery, HVAC systems and household appliances. The most common type of AC motor is the induction motor.
Brushless DC Motors: These motors are similar to DC motors but do not use brushes and commutators for current switching. They offer improved efficiency, reduced maintenance and higher reliability.
Electric motors are crucial components in modern technology, providing the mechanical power required for a wide range of devices and systems. Their efficiency, controllability and versatility have made them indispensable in various industries.
Why Regrease an Electric Motor?
Regreasing an electric motor is important for several reasons:
Lubrication: Electric motors have moving parts, such as bearings and gears, that require proper lubrication to reduce friction and wear. Grease serves as a lubricant, creating a protective film between the moving parts, reducing friction and preventing metal-to-metal contact. Regular regreasing helps maintain optimal lubrication levels and ensures smooth operation, which can extend the motor's lifespan.
Heat Dissipation: Electric motors generate heat during operation due to the electrical and mechanical energy conversion processes. Adequate grease helps dissipate this heat by acting as a thermal conductor. It absorbs and transfers heat away from the motor's components, preventing overheating and potential damage. By regreasing the motor, you ensure that the grease is fresh and capable of effectively dissipating heat.
Contaminant Protection: Electric motors are often exposed to various contaminants, such as dust, dirt, moisture and chemicals. Over time, these contaminants can enter the motor and mix with the existing grease, leading to the formation of abrasive particles or a breakdown of the lubricating properties. Regular regreasing allows for the removal of old grease along with any contaminants, providing a clean environment for fresh grease to be applied.
Noise Reduction: Properly lubricated motors tend to operate more quietly compared to poorly lubricated ones. By regreasing the motor, you can reduce the friction and associated noise generated by the moving parts. This can be particularly important in applications where noise reduction is crucial, such as in residential or office environments.
It is important to note that the regreasing frequency and procedure may vary depending on the motor type, application, and manufacturer's recommendations. Consulting the motor's user manual or seeking guidance from a qualified technician can help ensure proper regreasing and maintenance practices for your specific motor. It is important to follow the motor manufacturer's guidelines and recommendations for greasing intervals and procedures. Regular maintenance and periodic regreasing can help ensure the motor's optimal performance, longevity and reliability.

How to Properly Regrease an Electric Motor
- Gather all the appropriate tools required to perform the procedure.
- Verify that the grease gun's LIS code matches the recommended lubricant used in the electric motor bearing.
- Clean the external surface and the area around it with a brush and a lint-free rag.
- Remove the plug if fitted from each purge relief port and clean any hardened grease with a pipe cleaner.
- Remove the dust cap if fitted from each, and clean off any grease with a lint-free rag.
- Stoke the lever one or more times until clean grease discharges from the gun nozzle.
- Wipe the discharge grease from the grease gun nozzle with a clean, lint-free rag.
- Attach the grease gun nozzle to the grease fitting; do not hold the nozzle with your hand while applying.
- Slowly at 3-5 seconds per stroke, apply 1/2 of the volume.
- If you observe grease emerging from the bearing seals or purge relief port, discontinue greasing and record the amount added.
- If you feel any abnormal back pressure, stop greasing and look for obstructions in the grease passages; use a pipe cleaner to remove the obstruction.
- Gradually apply up to the maximum amount of grease to the bearing while observing the purge relief port.
- Stop regreasing if you see grease emerging from the bearing seal or purge relief port.
- Do not exceed the maximum calculated amount of grease for the bearing.
- Disconnect the grease gun.
- Repeat the steps for an outboard bearing grease fitting.
- Record the volume of grease added for each bearing.
- Clean the grease fitting and replace the grease cap.
- If no cap is available, leave a dollop of fresh grease on the fitting.
- Wipe up any grease from the grease gun nozzle and replace the cap.
- If purge fitting is the plug type, allow the motor to run for 15 minutes to expel any excess grease.
- Wipe up any grease purged by the relief port.
- If fitted, replace the plugs on the purge port.
- Collect and dispose of all consumables used during the procedure.
This article is based on the "Regreasing an Electric Motor" video from Noria's Task-Based Training series. To purchase this training course, visit the Noria Store.
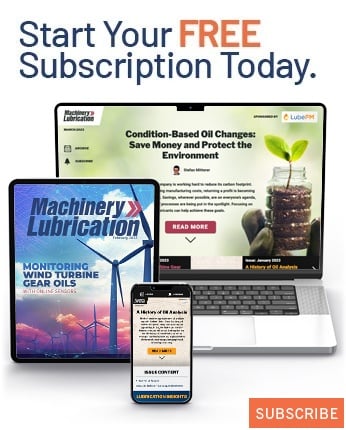