"What are the corrective actions to take on the basis of grease analysis results? How do you define used grease limits like used oil?"
Grease sampling is becoming more common for organizations looking to enhance their reliability programs. However, in many cases, grease analysis is performed only after damage or a breakdown has occurred. Trend analysis of grease samples has proven that early detection of grease or bearing failure can be caught well in advance with a good analysis program.
Before corrective actions can be taken, you must know what you are looking for and what tests need to be performed to obtain the necessary information. Alarm limits must be set to monitor the health of your grease and the well-being of your bearings. By looking at these results, you often can detect the root cause of a premature bearing failure, permitting appropriate corrective action to be taken.
The image on the right shows a large concentration of abrasive silica in grease, suggesting contamination from an external source (dirt from outside the bearing). In the image below, severe cutting wear indicates the source of grease contamination is coming from inside the bearing. Surfaces within the bearing are coming in contact with each other, which is tearing it apart.
Further testing of the grease could help identify the root cause of the bearing failures. If the test results for viscosity and additive health are below the acceptable limits for the bearing, this may reveal that the remaining useful life of the grease was depleted and that the grease should have been changed much earlier.
Limits for grease in service should be set to establish what is normal, abnormal and critical for the machines. These limits can be determined by the standard deviation average, taking grease samples from the same types of components at the same time (intervals). From these repeatable results (averages), you can identify what is normal for the components. You can then decide what is outside of normal by using the standard deviation average.
For normal samples, the average of all normal data is added to the standard deviation of all normal data. These samples are considered "normal."
Abnormal samples are two times the standard deviation of all normal samples plus the average. These samples are considered "alert."
Critical samples are three times the standard deviation of all normal samples plus the average. These samples are considered "alarm."
As with regular oils, the oil in the grease is the component doing the work (carrying the load), so it is essential that the following grease properties are also checked: viscosity of the oil in the grease (ASTM D445), the remaining useful life of the additives (ASTM D5483), the moisture level (ASTM D6304 or D6304), wear debris and particle count (ASTM D7690), dropping point (ASTM D566-02), and consistency (ASTM D1092).
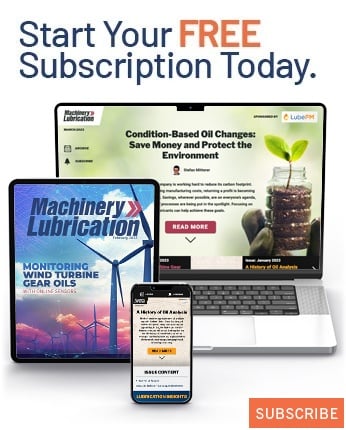