"Can you share any experience you might have regarding the use of thermal imagers to identify tribological problems, especially in the case of bearings? Is there any standard or reference for comparing results (temperature profiles) and drawing conclusions? I often get different types of profiles, which makes it very difficult to draw any conclusions."
As with most predictive technologies, thermography's real value comes not from an instantaneous measurement but the trending of data and the further analysis of that data. Heat is often a symptom of eminent machine failure or malfunction.
A non-contact infrared imager can be used to quickly obtain a multi-point temperature profile that can easily be assessed. This inspection can be performed with little to no disruption to the facility's operations and can be utilized as a screening tool as part of a daily or weekly inspection.
The constant feedback from these inspections can be used to analyze any changes. These changes are the “real” data.
While there exists no standard of reference for the temperature profile of a specific machine component, there are some expectations. The variables that feed these expectations include but are not limited to speed, load, viscosity, contamination, size, base oil type, etc.
There are so many variables that can contribute to the generation of heat that it would be nearly impossible to consider them all to generate such a profile.
Think of the data you get from your thermal imager as pieces to a mystery puzzle. At first, you don't know the shape of the puzzle or even what the picture on it looks like. Alone and incomplete, this puzzle may force you to guess as to what the issue is or make it difficult to identify the root cause.
With more pieces of the puzzle, which can be obtained through other methods such as sensory inspections, oil analysis, vibration, acoustics, etc., you can begin to see how these pieces are assembled and what image they are starting to form. Data is king, and the more you have, the better your chances of solving the puzzle.
Field experience has demonstrated that by appropriately combining and relating the results of different inspection options and tools, maintenance professionals can create a synergistic solution. This approach is much more thorough than one based on only one test or on several non-integrated inspection methods and often results in a much better diagnosis.
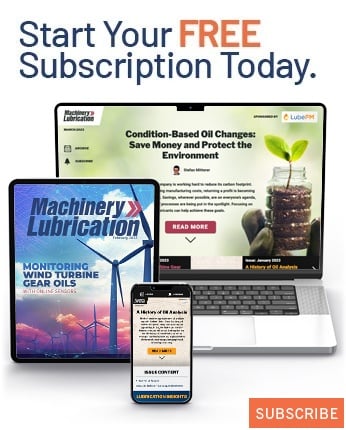