"We use a premium hydraulic oil in our hydraulic system, but copper continues to trend up. It is now at 200 parts per million. The equipment manufacturer says the only copper in the system is the tube in the heat exchanger. Could the copper be leaching into the oil?"
To confirm your suspicions, review the potential contaminants in the system. First, let's assume that copper is a contaminant in the oil. In general, oil contaminants originate from three sources: the machine environment, machine operation and maintenance activities.
Machine Environment
Your equipment is working within a production process environment as well as an atmospheric environment. Contaminants can come from the plant's surrounding area in the form of conventional dust, other minerals or moisture. They may also originate in the plant's transformation process as wood, water, chemicals, metals, etc. In your hydraulic system, the source of copper could be from a mineral or material containing copper being processed in the plant.
Machine Operation
When investigating a machine's internal contaminants, most people think only of the wear debris created during normal or abnormal operation. However, other pollutants can come from seals, gaskets or filters. Contamination may also result from a chemical reaction of the lubricant with external contaminants such as varnish, sludge, etc., or when the machine fails due to a lubrication, thermal or mechanical problem. In this case, consider the contaminants generated in the lubrication system. Heat exchangers made of copper tend to contaminate the oil with copper particles as part of their normal operation.
Oil cross-contamination is also a possibility. This may occur during storage, handling or application activities. It involves the contamination of the lubricant with another in-service lubricant, solvent or assembly oil used in the plant. This type of contamination can be identified by analyzing an oil sample in the laboratory.
The oil distributor or manufacturer's facility is another potential source of contamination. This can be determined by conducting analysis upon receipt of the oil. With this approach, you can confirm that copper is not a typical contaminant or ingredient in your new lubricants.
Maintenance Activities
Maintenance activities are often overlooked when searching for the source of oil contamination. They generally include repairs, part replacement, welding jobs and transferring oil into the machine. Keep in mind that these mechanical tasks should be conducted in a clean environment. The oil must also be cleaned and eventually dried before introducing it into the machine. In addition, oil flushing should be performed not only to remove contaminants from a machine or oil failure but also to eliminate contaminants introduced or generated during repair activities. If the repaired component was the copper heat exchanger, it is likely that copper debris is present in the system.
By reviewing the potential contaminants that could enter your oil along with their sources, you should be able to reach the proper conclusion. Typically, copper in hydraulic systems comes from the wear of mechanical parts or from copper components such as lines and heat exchangers.
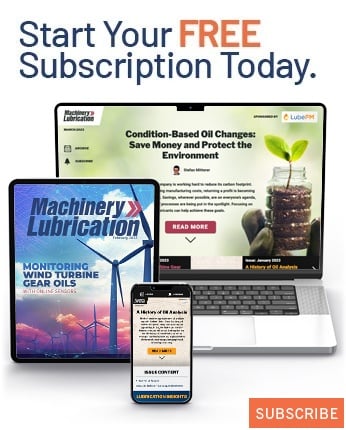