In some applications, it is nearly impossible for oil to remain fluid at all ambient temperatures. In these situations, the use of an oil heater is recommended. However, there are several things that must be considered before a heater is applied or even selected. In some cases, these devices can be counterproductive for your machines as well as your lubricants.
Why Utilize Oil Heaters?
There are several reasons why you may wish to utilize a lube oil heater for your systems. For instance, if your machine has splash-lubricated components, it will be important for the oil to remain fluid, as it will require a certain amount of fluidity for the oil to splash and lubricate the various parts inside the compartment. As the oil’s viscosity increases at colder temperatures, this splashing action is minimized and can result in premature machine wear.
Other lubrication systems utilize circulating oil. In this type of system, if the viscosity becomes too high, the oil may not properly flow through piping or may not even get pumped to lubricate the different parts inside the equipment’s lubrication circuit. In both of these cases, it is beneficial for the oil to remain fluid enough to do its required work inside the equipment.
The Importance of Oil Viscosity
Viscosity is one of the first properties to consider when choosing a lubricant. You must select the proper viscosity in order to have an adequate lubricating film at the operating temperature. If a piece of equipment will operate in a very cold environment and the operating temperature is also low, you can help maintain the oil’s fluidity by using a lower viscosity grade that is more in line with the ambient temperature.
To ensure the lubricant will provide an appropriate lubricating film at all in-service temperatures, you must also keep the viscosity index in mind as well. The viscosity index is a measure of how much the viscosity changes within a given temperature range.
The higher the viscosity index, the less the viscosity will change over that range in temperature. Depending on how great the temperature change is, the viscosity index can help determine whether a lube oil heater is needed. If the viscosity never thickens to the point where the oil ceases to flow, then a heater is not required.
Pour Point
Identifying the temperature at which an oil will stop flowing doesn’t have to be an engineering experiment or incredibly difficult. Look for one property in particular - the pour point. During this test, an oil sample is gradually cooled and its flow measured. Once no movement is seen after five seconds, the pour point is recorded as the previous temperature when flow was observed.
For machines that operate at low temperatures, the pour point is very important. If possible, select a lubricant with a pour point at least nine degrees lower than the lowest expected ambient temperature. This ensures the lubricant remains fluid enough at these lower temperatures so as not to hinder its movement or splashing characteristics.
Waxes
Wax is another lubricant constituent that affects the pour point. Waxes are commonly found in Group I paraffinic mineral-based oils. While they help contribute to a higher viscosity index, waxes can congeal and cause the lubricant to gel at colder temperatures.
In the refining process, great lengths are taken to remove as much wax as possible. One method known as chill dewaxing involves the oil being mixed with solvents to help absorb some of the unsaturated hydrocarbons, then chilled to congeal the wax and filtered to remove as much of the wax as possible. This is commonly found in Group I and II base oils.
Some Group II and most Group III oils undergo a process known as hydroisomerization. In this process, the normally straight paraffin chains are stressed and reformed into branched chains, which helps minimize the free wax and lower the pour point. If the oil in the machine is less refined or has a lower quality base oil, the wax content may be high enough that the oil gels much easier, leading to a much higher pour point and making the case for using an oil heater.
Pour Point Depressants
To combat the problem of waxes congealing, most lubricants are formulated with an additive known as a pour point depressant. This additive is commonly made from compounds of alkylated wax naphthalene, polymethacrylates and alkylated wax phenols. As mentioned previously, when oil cools, the wax crystals in the fluid begin to congeal, leading to the gelation of the oil and a higher pour point.
Pour point depressants inhibit the congelation of those crystals, keeping the oil more fluid and lowering the pour point. However, these additives only work down to certain temperatures based on the formulation and the wax content in the base oil. Once the temperature drops below a certain point, the pour point depressants are no longer able to keep the waxes from congealing.
Contaminants
Contaminants not only influence an oil’s viscosity and overall health but also impact its pour point. Soot is a common contaminant found in diesel engines that can increase an oil’s viscosity.
As the soot load builds, the viscosity rises as well. For example, after an engine is parked overnight during winter, the soot load contributes to decreased oil movement in the morning, which can result in delayed lubrication in the engine.
Glycol is another contaminant often found in engines. Similar to soot, glycol can also raise an oil’s viscosity and is one of the leading culprits of oil gelation in motor oils. Routine oil analysis can help to identify both of these root causes of impending lubricant and machine failure. Due to the propensity of engines to produce contaminants, you frequently will see diesel engines in cold environments with oil-pan heaters installed to keep the oil fluid.
Types of Oil Heaters
There are two main types of oil heaters used in industry. The first and probably most common for industrial applications involving a reservoir is a submergible heater (also known as an immersion heater) with a probe that extends into the oil.
The length of the probe and the heating capacity are based on the expected temperature and quantity of oil in the reservoir. If these types of heaters are used, they should be thermostatically controlled, since the elements can heat up and cook the oil surrounding the heater.
The temperature should be set to allow the oil to remain fluid but not too high so as to cause premature oxidation and hot-wall thermal degradation. Most of these heaters must be fully submerged. Otherwise, they can become damaged due to overheating.
The risk of thermal/oxidative degradation from an immersion heater is influenced by four factors: the temperature of the adjacent fluid, the thermal/oxidative stability of the fluid (additive and base oil type factors), the fluid’s viscosity (low oil viscosity is less risky), and the skin temperature of the heating element (heater watt density).
When inspecting the heater, any evidence of sludgy, carbonaceous deposits on element surfaces indicates that the skin temperature is too high. A good rule of thumb is 15 watts per square inch (2.4 watts per square centimeter) maximum for lower viscosity and/or briskly circulating fluids. For non-circulating and/or higher viscosity fluids, a watt density maximum of 10 watts per square inch (1.6 watts per square centimeter) should be maintained.
In the automotive world, many heaters are actually external to the oil sump. They work by heating the surrounding metal, with the heat then transferring to the oil to keep it fluid.
These heaters also need to be thermostatically controlled but have a lower risk of causing localized thermal damage to the oil, as they utilize more of a radiant heating process. The downside to these heaters is that they usually require more energy and take longer to become effective.
In my experience working on refrigeration compressors, I found it was common to use this type of heating apparatus to keep oil moving inside the compressor when it became cold. In the heating, ventilation and air conditioning (HVAC) industry, these are referred to as “crankcase” heaters.
They have a small heating element that wraps around the outside of the compressor. The heaters can then be tied into a thermostatically controlled relay to kick on and off based on the ambient and running conditions.
When Oil Heaters Make Sense
While heaters make sense in areas where the equipment will be operating in extremely cold conditions, this doesn’t mean that they are suitable for all applications. Don’t use an oil heater if the in-service lubricant doesn’t require it. If the lubricant remains fluid enough to move and adequately lubricate at all in-service temperatures, a heater will only put more stress on the lubricant and shorten its life.
In addition, don’t utilize heaters if the lubricant has a chronic problem with fuel dilution, as some heaters can get very hot. Fix the source of the fluid ingression and then continue using the heater. Also, exercise caution with heaters in applications that employ a lower refined oil or one that is at the end of its oxidative life. A heater may just be the catalyst needed to push the oil over the edge and kick-start the oxidative failure process.
By selecting the right oil heater and lubricants, you can help ensure your equipment will work well at all expected temperatures. Just remember that heaters are not a one-size-fits-all solution to problems involving high viscosity brought on by lubricant cooling. However, if you do your homework and routinely inspect your heaters and oils, they can provide tremendous benefits to your lubrication program.
66% | of lubrication professionals use oil heaters in their plant, according to a recent survey at MachineryLubrication.com |
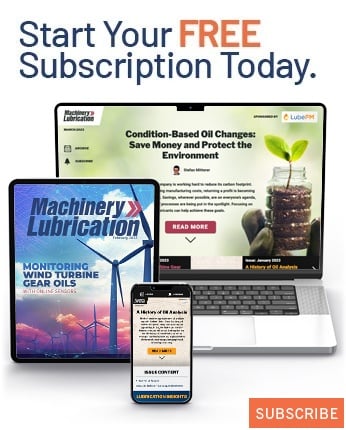